Selecting pumps for chemical pumping can be challenging. The pumped medium's characteristics can lead users to a certain pump style that best fits a given application. This article examines certain issues for selecting pumps to be used in chemical pumping. With flocculants, polymers or reagents that have long polymer chains, certain types of pumps will not be a good fit. For example, a high-sheer pump will destroy the polymer chains. The net result will be an increased consumption of flocculants or polymers. This does not mean that the high-sheer pump will perform poorly, but it will damage the flocculants and cause the user to use significantly more flocculants or polymers. A low-sheer pump will not destroy the polymer chains and will allow the reagents to reach maximum effectiveness, resulting in less overall consumption.
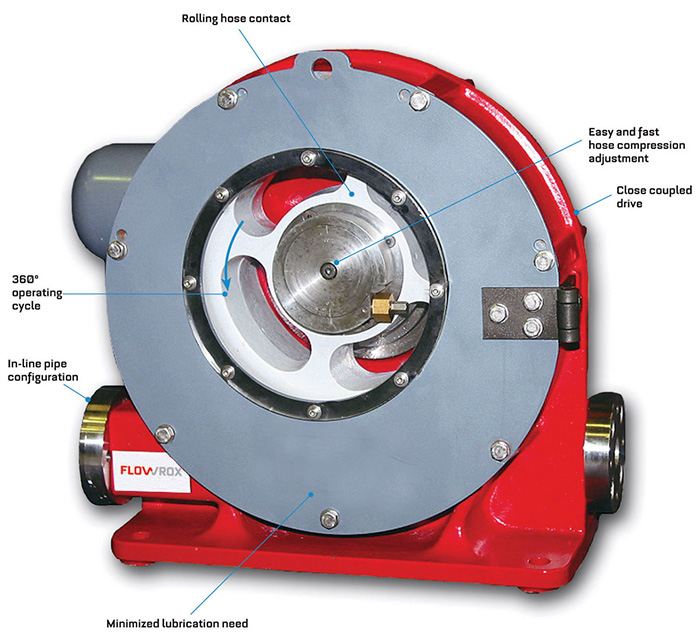
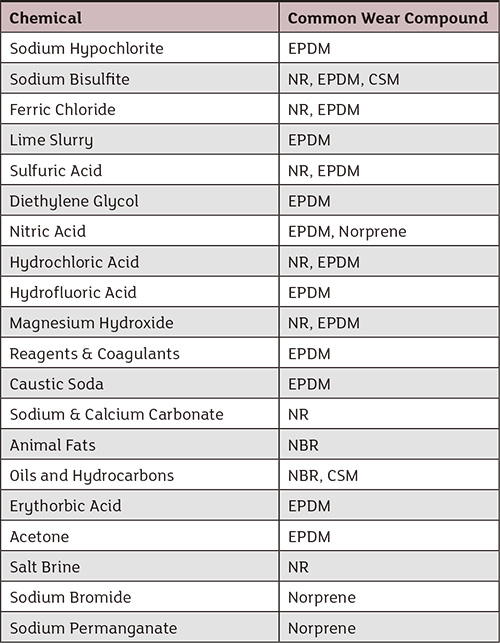
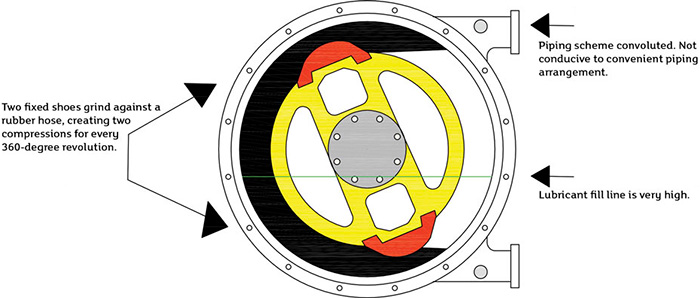
Picking a Peristaltic Pump
If all the variables have been evaluated and the peristaltic pump has been determined as the best alternative for pumping lime slurry, it is time to begin research on the types of peristaltic pumps that are available and decide which type is best for the application. Peristaltic pumps have been in existence for about 85 years. Rubber manufacturing and durability have made quantum leaps in those 85 years. Even just 30 years ago, automobile tires lasted up to 20,000 miles. In 2015, automobile tires are available with 80,000-mile guarantees. This surge in rubber technology has allowed peristaltic pumps to move from laboratory pumps to main production pumps based on their reliability. But the peristaltic pump operating principle limited the production availability until about 15 years ago. In the first 70 years, peristaltic pumps were manufactured with a fixed rotation point in the center of the pump hosing; two metal shoes rotate on fixed arms to compress the rubber hose. This design generates a significant amount of heat that, over time, damages the rubber hose and limits its longevity. To help combat the heat, the pump is filled with glycerin used for both lubrication and heat dissipation. Large amounts of this glycerin help transfer the heat to the pump casing. When the hose in this style of peristaltic pump begins to fail, the acid or slurry starts to mix with the large amount of glycerin. This is a hassle because a large amount of contaminated glycerin needs to be disposed, and the glycerin typically costs more than $100 per gallon. A 2.5-inch or 65-mm shoe design peristaltic pump may require 5 gallons or more of this glycerin. So with every hose change the consumer must dispose of more than $500 of useless glycerin. A chemical plant that has 10 or 15 shoe peristaltic pumps may consume more than $30,000 of glycerin annually. Approximately 15 years ago, a newly designed peristaltic pump entered the market. This new design incorporates a roller fixed on a cam that rolls over the rubber hose rather than grinding against it. In the shoe design peristaltic pumps, there are two fixed points where the shoes compress the rubber hose twice per revolution. The newly designed peristaltic pumps compress the rubber hose once every revolution. A common misconception with peristaltic pumps is that the medium determines how long the rubber hose will last. Of course, the medium has an impact, but the primary determining factor in how long a hose lasts in a peristaltic pump is how many times the rubber hose is compressed. So a pump that only compresses the rubber hose once per revolution is going to have hose life that is twice that of a pump that compresses the hose twice per revolution. The second advantage of rolling rotor design is that it requires only a fraction of glycerin that a shoe design peristaltic pump requires. The reason the rolling design does not require massive amounts of glycerin is that the rolling design does not generate the friction and heat. For example, your car tires drive over the road for hundreds of miles and may get warm, but they do not get extremely hot and require a bath in glycerin to cool them down. The single rolling design peristaltic pump only requires a half-gallon of glycerin for a 2.5-inch or 65-mm pump. This glycerin is required for light lubrication of the rubber hose only and not for the dissipation of heat. This is important because the shoe designs have significant limitations on rotation speed, but the rolling designs do not face the same limitations. Shoe designs will literally burn up the rubber hose if run at a high rpm continuously. Also, the continuous friction caused by two rubbing shoes can have a detrimental effect on a hose's lifetime even in a pump that is rotating at a slow rpm. Rolling designed peristaltic pumps can produce hose lifetimes that are three to five times longer than peristaltic pumps utilizing shoe designs.How a Rolling Design Peristaltic Pump Saved $20,000
The City of Hamilton, Ohio, was using shoe design peristaltic pumps for pumping lime slurry at its municipal power plant. These design differences may not seem significant, but the operating cost differences can be extreme. The facility's operations staff members realized they were spending a significant amount of their budget on replacement parts for their shoe design peristaltic pumps.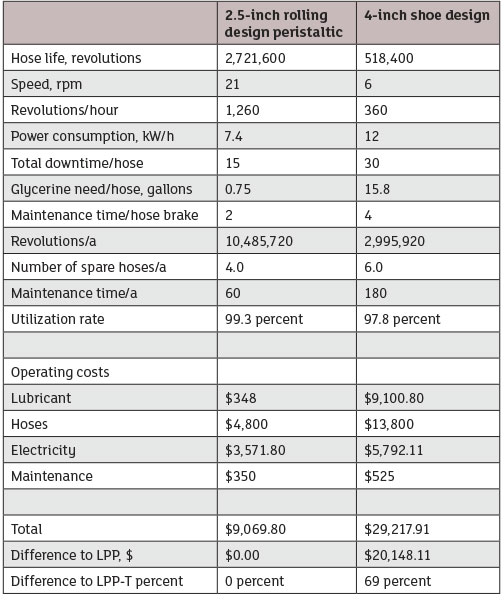