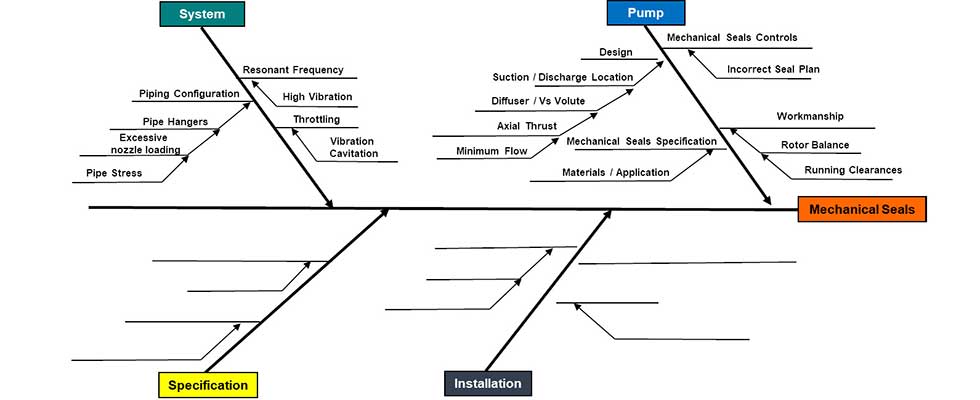
In my August 2020 column, we began populating the fishbone using the cause and effect process. We focused said process on the mechanical seal failures as the other failures (shim packs, bearings) require a separate investigation/root cause failure analysis (RCFA). At some point during the analysis, we may identify cause and effect where the bearings and shim pack failures may be a contributing factor, as I stated in the August 2020 column.
Teamwork
As we continue through the cause and effect process, it bears repeating that teamwork is critical to the success of any RCFA, and this is especially true as you develop the fishbone. Anyone with a vested interest in the pumping system in question as well as equipment OEMs, engineering, procurement and construction (EPC), etc., should participate and provide input throughout the RCFA.
Pump Issues
How would pump-related issues result in premature failure of the mechanical seals? Based on the history and current situation compiled during the initial phase of the RCFA, we found that the mechanical seals were an issue from startup/commissioning. With that in mind, let us begin the cause and effect examination.
Pump cause & effect
- design
- mechanical seal controls
- workmanship
- mechanical seal specification
Design cause & effect
(Design should not to be confused with specification.)
- suction/discharge location—pipe stress/torsional loading
- diffuser vs. volute—axial thrust under off-design conditions
- axial thrust control—axial thrust under off-design conditions
- minimum flow—overheating seals
Mechanical seal controls (plan) cause & effect
- incorrect seal “plan”—heat checking of seal faces
Workmanship cause & effect
When a new or rebuilt pump/system experiences issues during startup and commissioning, quality and workmanship should always be considered.
- rotor balance—vibration
- running clearances (wear rings, balance drum, etc.)—axial thrust
Mechanical seal specification cause & effect
Was the mechanical seal properly selected and specified for the application/service?
When selecting a mechanical seal for an application one must consider:
- pumpage/liquid
- pressure
- temperature
- liquid characteristics
- reliability and emissions
The above considerations will determine the seal’s design and overall construction material, its face and component materials, specifically:
- balanced/unbalanced
- single or double type
- cartridge/component
- metallurgy
- elastomers
- seal face materials/combination
Failure to take said considerations into account will ultimately result in premature seal failure.
This completes the pump bone of the fishbone diagram.
Read more Pump System Standards by William Livoti here.