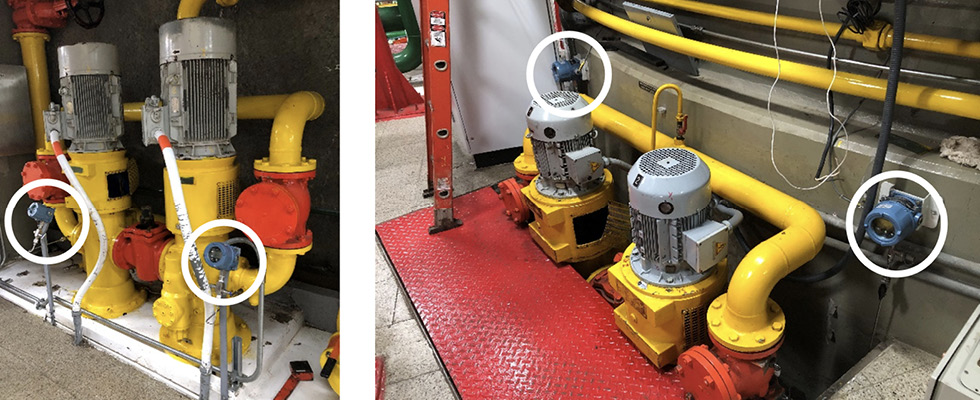
Pumps ensure the reliable and precise transfer of media, such as liquids and gases, across production stages. Within the chemical industry, pumps handle the movement of raw materials, intermediates and finished products between critical process equipment such as reactors, separators and storage tanks. The performance of these pumps is thus crucial to optimizing productivity and ensuring compliance to stringent safety standards. Deploying the right instrumentation on these pumps is vital, as it ensures the pump operates within specified conditions and, if necessary, can execute a shutdown to safeguard the equipment and environment from catastrophic damage.
Importance of Instrumentation Diversity
Pump instrumentation failure can result in hazardous scenarios such as pump overpressure or overheating. It is critical for operators to deploy a variety of instrumentation technologies to minimize the risk arising from a common mode instrumentation failure. Common mode failure is defined by the American Institute of Chemical Engineers (AIChE) as “concurrent failures of different devices characterized by the same failure mode (i.e., identical faults).”1
While older pumps are generally installed with mechanical instrumentation, newer pumps are designed with electronic instrumentation that provides the user with process data for informed decision-making. Since each instrumentation technology has its own pros and cons, it is the pump operator who skillfully leverages the advantages of each instrumentation technology to create significant operational, maintenance and cost efficiencies for the organization. These efficiencies are demonstrated through:
- Increased reliability and system redundancy – Relying on a single instrumentation technology can expose operations to significant risk, especially if the technology is susceptible to failure under similar conditions. Diversification introduces redundancy and ensures continuous production even if one system encounters issues. Downtime can be minimized and operational disruptions prevented.
- Improved data accuracy and faster control – While electronic instrumentation technologies can be more accurate and excel in capturing specific process data, mechanical-based instrumentation offers unparalleled speed of response. By integrating a diverse range of technologies, the operator can achieve data accuracy while ensuring split-second emergency shutdown control, optimizing the facility’s performance safely.
- Greater flexibility and future-proofing – As industrial processes evolve, a diverse instrumentation portfolio allows the user to adapt quickly to new challenges and requirements. Facilities that rely on a single technology may face costly upgrades to stay current. Diversification allows for smoother integration of new technologies, easier scalability and compliance with evolving industry standards without extensive system overhauls.
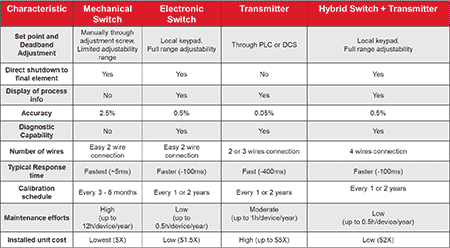
Types of Instrumentation Technology
There are several types of mechanical and electronic instrumentation technologies that are used in industries today.
- Mechanical switch – These devices provide the fastest emergency shutdown response (~5 milliseconds [ms]) to a process change, which is ideal for positive displacement pumps. Switches have been proven-in-use for decades and are easy to install and operate, but they require periodic maintenance. There are switches that are designed with wide adjustable deadbands to protect against pump cycling. Mechanical switches do not require any power to operate and are often considered to be a final line of instrumentation defense in an industrial plant (e.g., during a power outage).
- Electronic switch – These are viewed as upgraded versions of the mechanical switch. While a little more costly than a mechanical switch, they offer expanded functionality, such as programmable set points and deadbands across the entire range, and they possess better repeatability compared to a mechanical switch (up to four times). They have very fast response times at <100 ms and have the capability to provide a basic level of diagnostics about device health. Less time is required to maintain (i.e., uninstall, calibrate, set and reinstall) these electronic switches compared with traditional mechanical ones, thereby improving maintenance efficiency.
- Transmitter – Transmitters are ubiquitous in industrial plants. They are able to transmit data from the field to the control system through standardized output signals like 4-20 milliamps (mA), 0-10 volts (V) or a digital signal. Transmitters are costly but are highly accurate and possess advanced device diagnostics. Their response time is typically slower (at <400 ms) than mechanical switches.
- Hybrid switch and transmitter – This technology represents a hybrid between the functions of a transmitter and a switch, offering the advantages of a transmitter (availability of data) as well as the benefits of an electronic switch (ease of operation and maintenance).
Various instrumentation technologies can work on most types of pumps and applications, but the primary differentiators are speed of response, pump requirements and price.
Case Study 1: Hybrid Switch & Transmitter on Lubrication Oil Pumps
Application challenge
In one plant of a major industrial end user in South America, some of the mechanical switches installed on pumps for the lubrication oil system were old and out of service, posing a few challenges to the instrumentation team. First, the process variable was hard to verify, as there was no display on the switches and the line gauges were located in hard-to-reach areas. Second, significant maintenance time was spent on the switches—about one hour of maintenance per switch—with at least two maintenance cycles per year.
Solution
The user replaced 24 mechanical switches with a shutdown hybrid switch and transmitter. The hybrid technology was chosen to ensure that when the oil pressure fell below the 32 pounds per square inch (psi) setpoint, the backup lubrication oil system would kick in to avoid any lapse in oil flowing through the turbine system. The hybrid instrumentation technology enabled the pump operator to:
- Program setpoints and deadband locally on the device, which simplified setup, calibration and maintenance of the instrumentation
- Derive device diagnostics to verify the instrumentation was working optimally, reducing service maintenance time
- Exercise the option of extracting the 4-20 mA output to trend pump process data and develop a predictive pump maintenance program in the future
Case Study 2: Mechanical Switches as a Final Line of Defense
Application challenge
A global pump manufacturer (OEM) supplies pumps to the chemical industry. Pressure and temperature mechanical switches were installed on their dry screw pumps for emergency shutdown function. The user was facing reliability and quality issues of the switches installed. The risk lay in a situation where the switch on the pump did not reliably shut down the pump when needed. This could damage the dry screw pumps and incur high repair costs.
Solution
Temperature switches were installed on the water jackets as well as pump exhaust to prevent pump overheating. In addition, pressure switches were installed on the pump exhaust and set to 5 psi to prevent overpressure.
Safety integrity level (SIL)-certified mechanical switches were selected, as they had proven-in-use reliability, minimizing the possibility of instrumentation failure. Although there were transmitters installed on the pump systems to transmit process data and turn off the pump when needed, the switches were critical for emergency shutdown purposes, when response time is crucial. The switches were a necessary complement to the overall pump instrumentation architecture,
serving as a last line of defense to prevent pump damage.
Every instrumentation technology has its advantages and disadvantages. Pump operators who know how and when to leverage these advantages for their instrumentation application, or even deploy multiple technologies to create layers of necessary redundancy, are able to build a robust, sustainable instrumentation architecture for plant safety. The limitations of each instrumentation technology accentuate the importance of instrumentation diversity.
References
aiche.org/ccps/resources/glossary/process-safety-glossary/common-mode-failure