While PC pumps are ideal for high-viscosity liquids, it can present users with unique challenges.
07/17/2015
Persistent maintenance and unacceptable odor prompted a Southwest wastewater treatment plant to replace its sludge-handling system with progressive cavity (PC) pumps. Used to move high-viscosity fluids in the food, wastewater, refining, papermaking and wood processing industries, PC pumps were ideal for this application. While the new equipment reduced spills and maintenance costs, the application of PC pumps can present challenges when sealing the rotating drive shaft. The nature of the viscous, abrasive and/or adhesive fluids presents unique sealing challenges.
The Application
The treatment plant had been using a conveyor to move 2 million gallons of sludge cake per day from belt filter presses to holding hoppers. Two short conveyers then transported the final 19 to 24 percent biosolids to the sludge processing area. This process resulted in spillage, which created significant problems for the plant.
Stuffing Box or Integrated Seal Chamber
PC pump manufacturers may offer a conventional stuffing box or component mechanical seal chamber, or they may integrate the seal chamber into the design via the mechanical seal supplier. The advantage of the conventional stuffing box is that it allows a variety of sealing device solutions. The disadvantage is the additional cost. The integrated sealing solution is supported by the equipment manufacturer and will fit the narrow bearing frame space.Flush Liquid
Mechanical packing or a standard single liquid-lubricated mechanical seal can be used for difficult fluid if a flush is provided to prevent damage to the primary sealing elements. Liquid-lubricated mechanical seals use the pumped fluid as a lubricant. PC pumps handle high solids content or adhesive fluids, which are known to damage the highly polished primary sealing surfaces or cause clogging of secondary seals. Solids can become embedded into braided mechanical packing, causing damage to rotating sealing surfaces on the shaft or sleeve. One method that can be used to avoid this issue and protect pump elements from damage is to provide a clean flush liquid (commonly water) at 15 pounds per square inch gage (psig)/1 bar above the actual sealed pressure. Unfortunately, the flush must be compatible with the process; if the process is designed to remove fluid (such as dewatering), a flush fluid may not be acceptable.Dual Sealing
If a flush fluid is not acceptable, dual liquid-lubricated seals may be required. These seals use two primary sealing elements to trap a higher pressure clean compatible fluid between them. The clean compatible fluid will lubricate the seal faces and prevent clogging of the secondary seals. The higher pressure fluid is known as a barrier fluid. It can be provided by a fluid reservoir and pressurized to 15 psig/1 bar above the sealed pressure or by a plant water source as long as the plant water pressure will provide the seal at least 15 psig/1 bar pressure above the sealed fluid pressure. A Midwest coal-fired power plant uses PC pumps in its flue gas desulfurization dewatering area. Originally equipped with conventional packing, the pumps consistently struggled to pump the sludge of up to 40 percent solids. The operators searched for another method to lengthen service life and reliability from the current four to six months. The braided mechanical packing was replaced with a dual liquid-lubricated mechanical seal with abrasion-resistant seal faces. The dual mechanical seal has been in continual service for more than two years. Mechanical seal manufacturers can offer seals that use abrasion-resistant hard seal faces designed for difficult service. These materials are typically ceramic and offer extreme hardness, which allows them to withstand short-term pressure reversals. If the barrier fluid pressure drops below the sealed pressure, solids can begin to track between the seal surfaces, but hard faces will prevent serious damage. Once pressure is restored, the solids are displaced from between the sealing surfaces. Seal companies can estimate leakage between these surfaces based on the shaft diameter, sealed pressure and properties of the seal or barrier fluid. Many seal manufacturers measure dual seal barrier fluid leakage in parts per million, making this a virtually zero-contamination solution.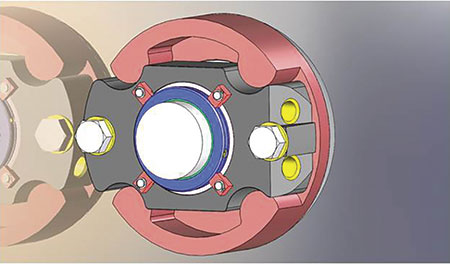
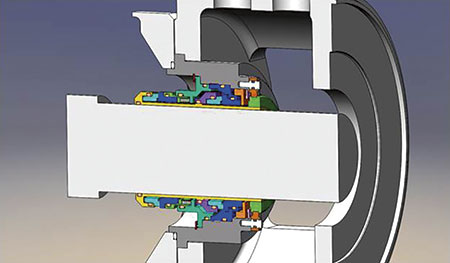
Polymeric Sealing
Another method is to use a polymeric sealing element mounted inside the equipment to replace the common braided packing solution. This polymeric element could be mounted inside a housing on a ceramic-coated sleeve to make installation easier and prevent equipment damage. These polymeric devices can be designed with single or multiple lips sealing on a rotating shaft or sleeve. They can be used with a clean flush liquid or high-viscosity grease to prevent solids from being trapped between the lip sealing element and the rotating sleeve or shaft. However, they are extremely intolerant of radial shaft movement. If the radial support bearing in the PC pump gearbox is worn, end users should avoid this solution. Radial movement will establish gaps, which become clear leak paths.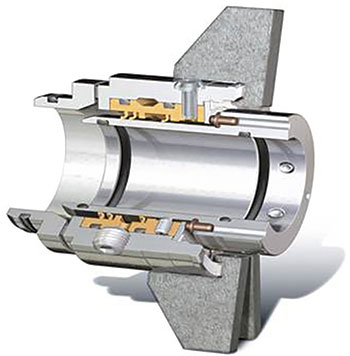