Q. What are the advantages and limitations of a sealless pump design? A. A sealless pump is used when there is a need to contain toxic, dangerous and/or valuable fluids. Application may be dictated by space, noise, environment or safety regulations. This section outlines types, nomenclatures and components of sealless rotodynamic-type pumps. Sealless pump design is founded on eliminating the dynamic shaft seal between the wetted end of a centrifugal pump and the atmosphere. This is achieved by enclosing the pump and its rotor assembly inside a pressure vessel with the pumped fluid. The pressure vessel or "primary containment" is sealed by static seals, such as gaskets or O-rings. The inner rotor assembly is driven by a rotating magnetic field that is transmitted through a containment barrier. Sealless pumps fall into two categories: magnetic driven pump (MDP) and canned motor pump (CMP), as shown in Figures 5.1.3.1 and 5.1.2.1.
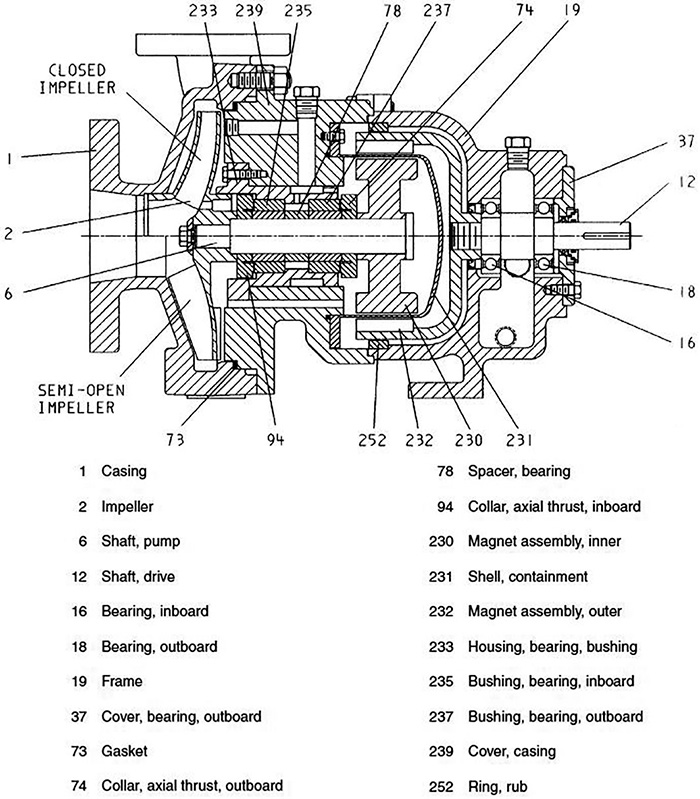
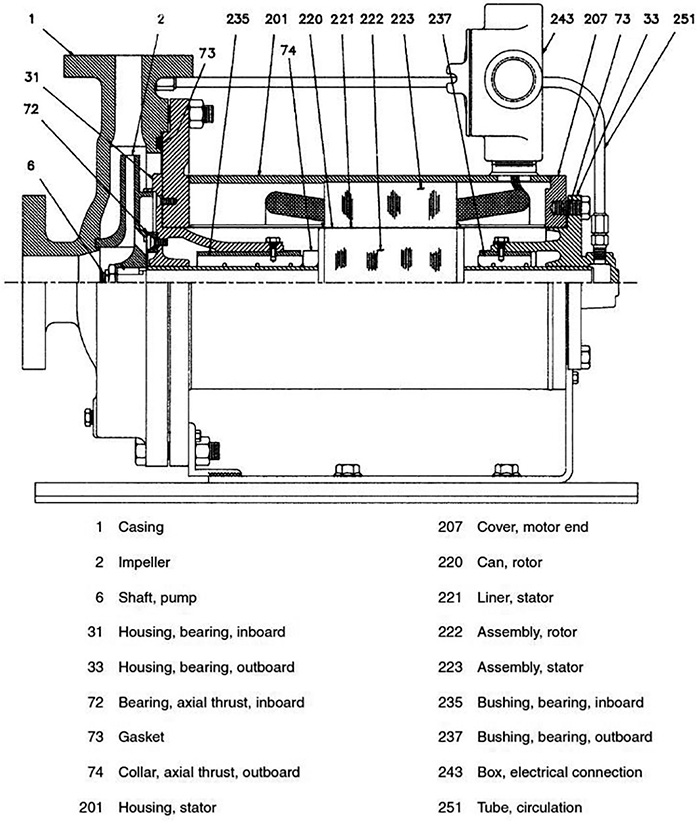
- Improved safety when handling hazardous liquids
- Eliminated leakage through primary containment to the environment during normal operation
- Optional backup secondary containment
- Eliminated loss of valuable liquids
- Lower noise level (CMP designs)
- Suction pressure usually does not affect the axial thrust
- Reduced or eliminated periodic shaft seal replacement cost
- Temperature of motor windings (CMP) or magnet components (MDP)
- Control of bearing environment is required to provide clean non-flashing liquid.
- Primary containment shell is relatively thin, and corrosion potential should be carefully considered.
- Retraining of maintenance personnel may be required.
- Drive-generated heat may affect the NPSH required with some circulation plans for volatile liquids.
- Overheating of drive section may occur with loss of flow or loss of suction.
- Potential for higher repair cost if bearings fail before detection
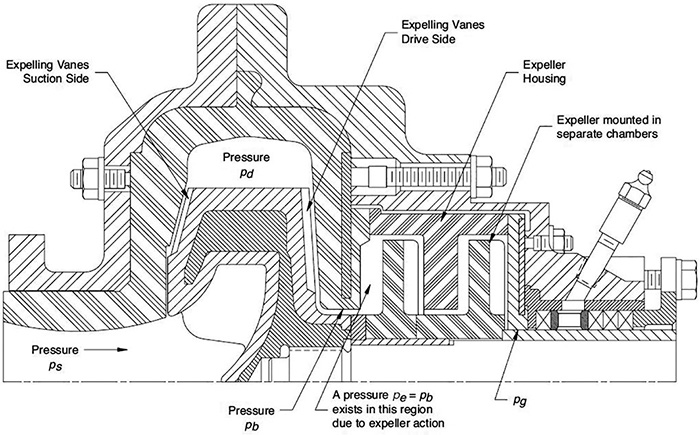