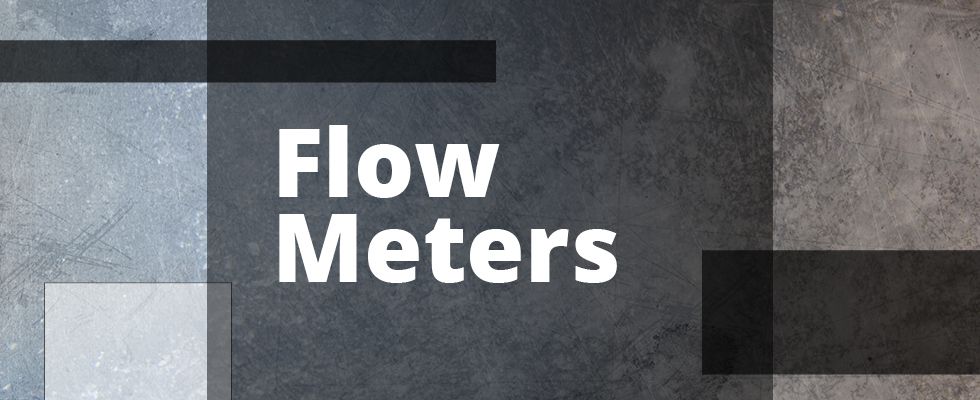
Today, water usage by commercial, industrial and municipal entities is tracked and controlled through tightened government regulations and oversight. As water resources become scarcer, requiring greater oversight and reporting on water draws, it is necessary to add accurate flow measurement into new and existing installations where there may be limited straight runs of piping available.
Flow measurement is a critical aspect in a wide range of industrial operations. Factors including fluid characteristics, flow profile, measurement range and accuracy requirements are all important considerations in determining the right flow meter for an application. Additional considerations, such as mechanical restrictions and installation limitations, can impact the user’s choice.
For water treatment plant operators, for example, it is critical to monitor ground, surface and well water flow to the facility. A stable and trustworthy monitoring solution is also needed for water flowing into booster pump stations and through water mains in water distribution systems. Booster pumps may be needed to handle peak flows in a distribution system, which can otherwise meet the normal flow requirements.
Building design, heating, ventilation and air conditioning (HVAC) and plumbing applications have similar demands for flow measurement performance. Accurate flow information helps facility engineers monitor water consumption, reduce energy expenses and minimize repairs to valuable equipment, as well as manage building cost allocation and hydronic system optimization.
How Piping Affects Accuracy
Water treatment and distribution as well as building design, HVAC and plumbing applications can be complex and often have minimal piping area to install flow measurement devices. The challenges can include zero straight-run environments; proximity to pumps, valves and other devices; and Ingress Protection (IP) Code 68 requirements for permanent immersion or underwater installation of metering equipment.
Different flow meter technologies have different straight-run requirements, based on the inherent character of how each technology works. The requirements are usually expressed in terms of distance away from the instrument in a multiplication factor of the pipe diameter. They are also defined as either being upstream or downstream from the device. It is important to consider straight-run requirements to ensure that the chosen meter will fit in the space and system already in place.
Flow meter accuracy can be affected by many upstream and downstream flow characteristics. This includes piping configurations, such as elbows, tees or reducers. Valves also create flow disturbances, including butterfly, check or control valves. Likewise, pumps discharging into a pipe close to the flow meter often disrupt the flow profile.
Flow disturbers can create an asymmetric velocity profile or swirl, resulting in flow measurement errors. Flow meter inaccuracy can be from underreading or overreading. The amount and direction of inaccuracy depend on factors ranging from flow velocity and profile to the type of metering technology.
Flow meter manufacturers typically specify the amount of upstream and downstream straight pipe required for installation. This may be five to 10 or even more pipe diameters of straight pipe before and after the meter. In some cases, flow straighteners or conditioners can be installed to reduce the amount of straight pipe needed. Several types of devices are available; however, they do not work with all flow meters. Also, pressure losses may occur depending on the type and installation of the flow conditioner.
Although some rules of thumb can be used for each flow technology, each application may have its own considerations for choosing a metering approach. The best option may be to use a flow meter designed for circumstances where a sufficient length of straight-run pipe is not possible.
Finding the Right Metering Solution
When installation space is limited, an electromagnetic flow meter can be an ideal solution. These flow meters do not require much upstream and downstream straight run so they can be installed in relatively short lengths of piping. They typically need only three to five diameters of upstream straight run, and zero to three diameters of downstream straight run from the center of the flow tube. Electromagnetic flow meters are also relatively insensitive to errors caused by nonsymmetrical velocity patterns or swirl.
Electromagnetic flow meters use Faraday’s Law of Electromagnetic Induction to determine the flow of liquid in a pipe. With this approach, a magnetic field is generated and channeled into a conductive liquid flowing in the pipe. The flow of the liquid through the magnetic field will cause a voltage signal to be sensed by electrodes located on the flow tube walls. When the fluid moves faster, more voltage is generated. Faraday’s Law states that the voltage generated is proportional to the movement of the flowing liquid. The electronic transmitter processes the voltage signal to determine liquid flow.
Electromagnetic flow meters produce signals that are linear with flow. As such, the turndown associated with the meters can approach 400:1 or better without sacrificing accuracy.
Electromagnetic flow meters have proven to be an effective tool for measuring the flow of water and chemical additives in a wide range of water treatment and distribution applications. They also help commercial and industrial facility operators ensure the reliability and efficiency of HVAC system components that can impact their bottom line.
Latest Technology Advancements
In recent years, the accuracy and reliability of electromagnetic flow meters have improved thanks to advancements in electronics and the development of
rugged electrode and lining materials and efficient manufacturing methods. Other metering technologies often require a specified amount of straight run upstream and downstream to deliver accurate measurements.
In applications where adequate straight run is not available or achievable, controls contractors and other key stakeholders are opting for electromagnetic meters validated by the Netherlands Measurement Institute (NMi) to Organisation Internationale de Métrologie Légale (OIML)/European Measuring Instruments Directive (MID), assuring they are a suitable solution in tight applications with no space or budget for modifications. These meters typically have no moving parts or strainer requirements that minimize meter vault size and are suitable for potable water, well water, reclaimed water, wastewater and water-based solutions.
Building design, HVAC and plumbing applications are often complexly designed with limited space for meter installation. This rules out meters that require a certain number of straight pipe lengths upstream or downstream as the space is not available.
Additional challenges include proximity to pumps, valves and other devices, as well as IP68 requirements for permanent immersion or underwater installation of metering equipment. Rather than completing expensive modifications or remodeling the application, engineers can deploy electromagnetic meters that eliminate the need for redesign to meet straight requirements efficiently.
Whether designing a new facility or retrofitting an existing site, installing the wrong flow meter can lead to inaccurate measurements and other performance issues that can last for years.