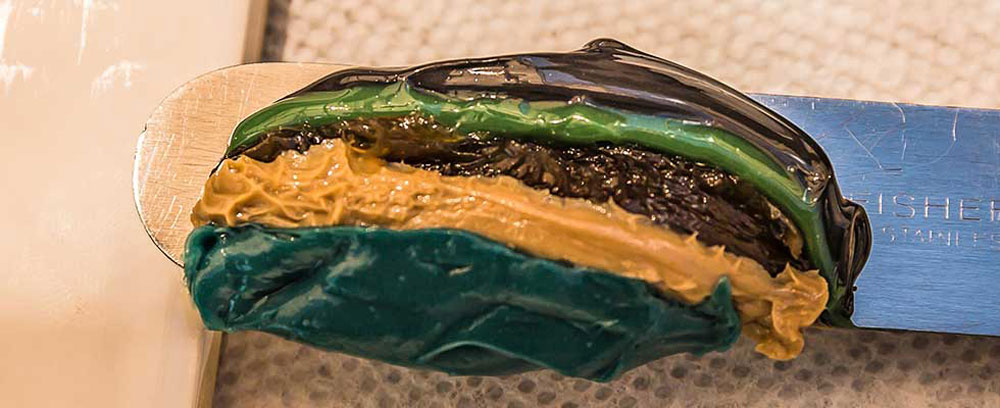
Pumps are critical in moving fluids, slurries or gases (compressors) in industrial plants, municipal water and wastewater systems and chemical processes. The compressed or pumped fluids move from high pressure to low pressure with the energy assist provided by the mechanical action of the pump. Whether the pump is a rotating or positive displacement pump, the goal is to change mechanical energy into fluid energy. In most cases, the prime mover is an electric motor or engine turning a shaft at high speed that adds energy to the fluid to be moved.
The bearings that support that shaft must be lubricated to reduce friction, increase efficiency and prevent wear. When that lubricant is a grease, the lubricant also performs the critical role of sealing the bearing from the ingress of contamination from particulates from the environment or fluid from the high-pressure side of the pump.
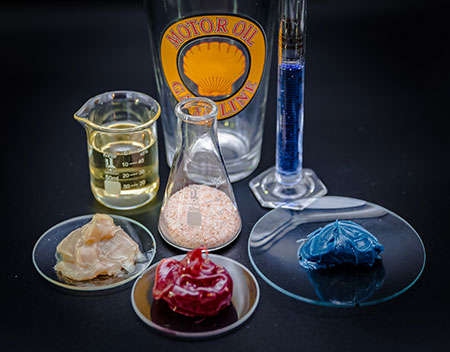
Which Grease Is the Right Grease?
Sometimes the pump OEM provides guidance on grease selection. Generally, the language is vague and unhelpful unless the user is well-versed in lubrication. For example, the pump OEM may say, “Lubricate with a high-quality National Lubricating Grease Institute (NLGI) 2 lithium grease.” In any given plant, there may be multiple greases that are lithium or lithium complex thickened. But how is “a high-quality NLGI 2 grease” defined?
Experienced maintenance professionals may rely on previous practice or hard-learned lessons from the trial and error school that have led to a working solution. Just because a grease solution has worked in the past, does that guarantee future success? Is the working solution optimal? The NLGI recently launched a new grease specification designed to provide guidance and support in determining a level of quality and performance that maintenance and operations staff can use to select a grease that is fit for the purpose and instill confidence.
NLGI’s HPM Grease Specification Detail
The NLGI high-performance multiuse (HPM) grease specification is a performance standard for industrial applications that parallels NLGI’s long-running GC-LB classification system introduced in the late 1980s specifically for automotive chassis and wheel bearing lubricating greases. The HPM specification contains two broad areas: manufacturing conformance/quality and application performance expectations.
Since lubricating greases are manufactured by chemical reactions and mechanical processes, it is important to ensure the finished product meets the manufacturing standard for mechanical stability, oil separation and NLGI consistency. The HPM specification sets constrained limits that define expectations that the user can rely on when buying greases that carry the HPM specification.
Performance expectations vary depending on the intended application for the lubricating grease. The HPM specification sets a baseline performance standard with respect to seal compatibility, load carrying capacity, starting torque (at -20 C/-5 F) and the closely interdependent water resistance and corrosion protection.
To maximize efficiency and component protection, the viscosity of the chosen grease’s base oil is the most important consideration. That is driven by bearing size, rotational speed and operating temperature. If the OEM has taken those items into consideration, users can follow its lead and find success. If the guidance is vague or specific operating conditions are difficult, users may have to look deeper to find the best solution.
HPM Enhancements for Various Operating Conditions
Again, users can consult the NLGI HPM specification to provide guidance. The HPM specification includes endorsements for enhanced performance that may apply to specific pump situations—corrosive media, excessive water ingress potential, vibration or extreme temperatures. The endorsements are:
- WR (water resistance)—In order for a lubricating grease to meet these endorsement criteria, the water resistance must be measurably better in standard American Society for Testing and Materials (ASTM) tests such as water washout (ASTM D1264) and water spray-off (ASTM D4049) than the requirements of the baseline HPM specification.
- CR (corrosion resistance)—Similarly, the CR endorsement builds on the HPM base requirement, and then places additional performance requirements for greases when exposed to corrosive media such as seawater or salt solutions via combined static and dynamic ASTM tests (ASTM D6138).
- HL (heavy load)—Some pump installations may be exposed to vibration and dynamic loading from adjacent equipment. The HL endorsement is intended to certify greases that have enhanced load carrying capacity as illustrated by performance under extreme pressure (ASTM D2596 and D5706) and wear resistance (ASTM D2266).
In addition, consideration is given to fretting protection via two other methods (ASTM D7594 and D4170).
- LT (low temperature)—Because outside installations expose pumps to low-temperature startup, greases that have the LT endorsement have starting torque that meet or surpass bearing OEM guidance at -30 C/-22 F. These criteria reduce the potential for bearing damage at startup due to excessive torque.
As an industry body, the NLGI is brand- and marketer-neutral. While the NLGI membership is made up of representatives from grease manufacturers and marketers, it has additive and raw material suppliers among its members that bring balance and perspective in many cases. The HPM specification process was inclusive of these membership classes. Marketing and manufacturers include major integrated oil companies as well as specialty grease companies and third-party manufacturers. It was mutually agreed that the HPM specification should be challenging but achievable, setting a common performance expectation that gives guidance to the end user. The process involved several iterations among the NLGI members and consultants to establish the performance limits and acceptance criteria.
Grease selection may include many facets—brand, value, availability and local service, for example. Sales and marketing materials from various sources can be confusing or even overwhelming. The HPM specification is intended to provide a common performance expectation for the end user that provides a level of confidence that the product will perform in a specific pump application. The other criteria can help to narrow down a user’s product selection and purchase decision.
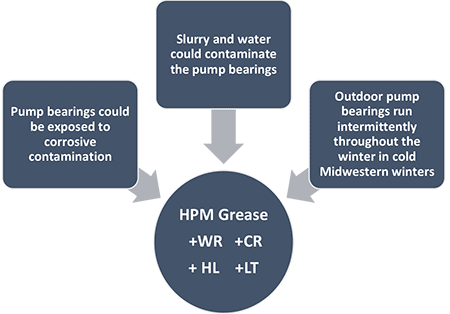
Real World Example Using HPM Grease Specification
A water treatment facility has multiple centrifugal pumps that move water, handling corrosive treatment chemicals and waste sludge. The facility is in the Chicago area where the pumps are in-service both inside and outside, exposed to the elements. The sludge pumps have redundancy built-in, so they operate intermittently. Plant operations staff wishes to increase plant uptime, reduce maintenance spend and simplify lubrication tasks. Based on this scenario, what should the operations staff do? The selection process might look like this.
Once the maintenance staff identifies the potential performance challenges, the HPM basic grease is a good choice. However, a better choice would be to pick a grease that provides performance even when exposed to corrosive process chemicals (HPM + CR) and excessive water (HPM + WR). Considering the pumps may face cold temperatures at startup, a low-temperature grease may be a wise choice (HPM + LT). By choosing to reference the NLGI HPM specification, base performance is established. Additional endorsements for CR, WR and LT will allow the staff to choose one product that can mitigate all of its performance hurdles and simplify its lubrication routine by consolidating to one product for all of the pumps.
Protecting pump components, reducing operational expense and simplifying grease selection are all worthy and attainable goals. Using the NLGI HPM grease specification helps users reach those goals. By consulting a lubricant provider and challenging them to provide quality and performance that meets the NLGI HPM standard, grease users can set and exceed expectations when selecting greases for lubricating their systems.