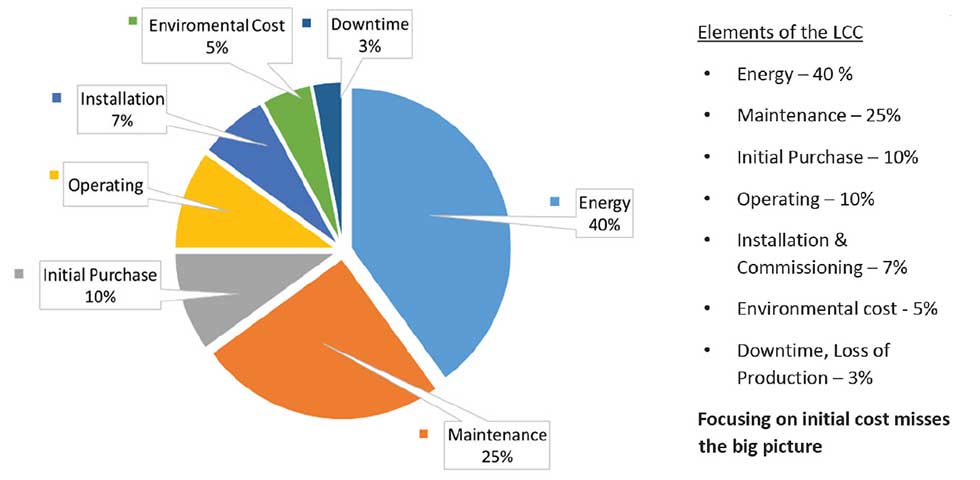
Is it really worth buying the more expensive, efficient pump over a cheaper, less efficient pump?
It is the routine operating costs of energy, maintenance and other recurring expenses that make up the primary components of total life cycle cost (LCC), as illustrated in Image 1 for a typical installation.
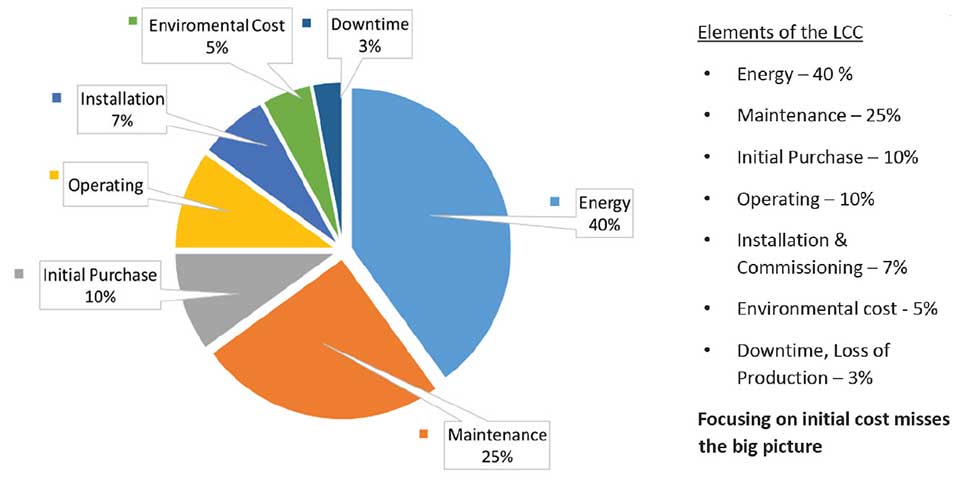
For example, say the initial purchase and installation cost of a 100-horsepower (hp) pump was $30,000. The 100-hp pump running at full load with a cost of electricity of 8 cents per kilowatt hour ($0.08/kWh), operating continuously, would total $52,000 per year.
In just one year, the energy cost is more than double the installed cost. Over a typical life cycle of at least 15 years, the energy cost totals $780,000. In this example, the installed costs account for only 4 percent of the lifetime energy costs.
To compare a more efficient pumping system’s annual cost, we will assume some round numbers and focus on just the pump input power (excluding the motor) for calculation simplicity. Start with a pump that is 70 percent efficiency and compare it to an identical pump that is 75 percent efficient. This change lessens the pump input power required. This difference can be calculated using Equation 1.
Pump input power 1 (hp) x (Pump efficiency 1) / (Pump efficiency 2) = Pump input power 2
Pump input power 2 = 100hp × 0.70 / 0.75 = 93 hp
Equation 1
From this calculation we observe a power savings of 7 hp. To calculate the lifetime cost savings of 7 hp, use the formula in Equation 2.
(Note: this is not taking into account motor loading or motor efficiency)
Where:
- Pump input power saved = Reduction in power due to higher efficiency (hp)
- 0.746 = kW/hp
- Hours/year = Annual hours of operation
- Rate = Electricity cost in $/kWh
Then:
Electrical cost savings ($) = (7 hp) × (0.746 kW/hp) × (8760 hrs) × (15 years) × ($0.08/kWh)
Electrical cost savings ($) = $55,000
Equation 2
It is important to also note that pump operating efficiency is often lower than the rated condition due to oversizing, problems with control valves, poor installation and other factors that result in the pump operating away from the best efficiency point (BEP) or rated condition.
Therefore, it is beneficial to precisely analyze the system requirements, optimize the control systems, and when justified by a life cycle cost analysis, invest money upfront for a more efficient pumping system.