In a typical plant, pumps often are controlled by semiconductors such as microprocessors, power electronics and variable frequency drives (VFDs) to digitally link assets and provide better process control. By using “smart” centrifugal pumps with VFD controls, plant operators can vary the pump and impeller speed, allowing the motor output to match the system requirement for improved system performance. A VFD operates by converting alternating-current (AC) power to direct-current (DC) power, which is then changed back to a pulse width modulated AC waveform in the form of variable frequency and voltage to the induction motor. Feedback from the VFD provides operators with valuable data to determine pump performance. In essence, VFDs give plant operators control of the pump’s speed and output by changing the voltage and frequency to a pump’s motor. Modern VFDs can produce accurate and reliable speed and torque feedback using sensorless control algorithms—offering improved pump reliability, extended product life and reduced energy and processing costs.
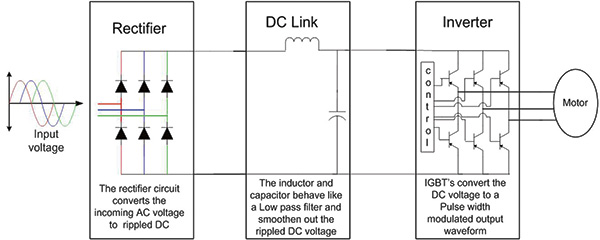
Torque Control for Improved Process Management
Most plant managers synchronize the speed or balance the load of their pumps. However, many operators do not realize that the must factor together speed and torque to determine the pump’s true operating conditions and to best protect a pump system from failure. If torque control is applied to centrifugal pumps, in most applications, plants will see tighter process control loops, higher control resolution and improved response time. Tighter process control means less energy used and an increase in process efficiency. More specifically, synchronizing torque is an excellent way to control a centrifugal pump with a relatively flat performance curve. Figures 2 and 3 show a centrifugal pump head curve and its corresponding torque curves.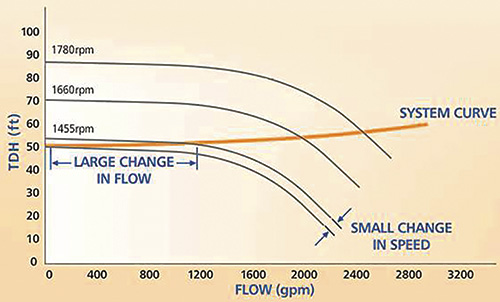
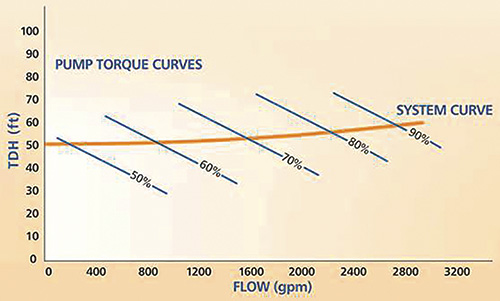
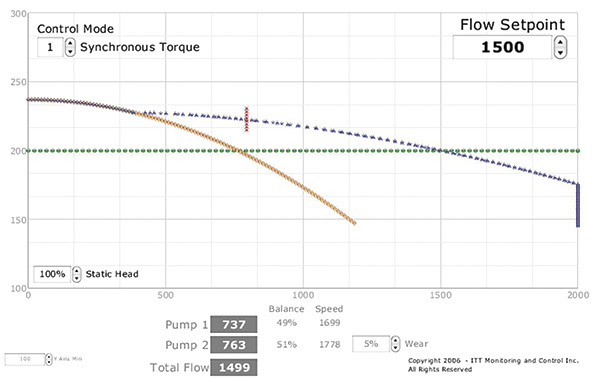
Case Study: Salt Mining
Incorporating sensorless flow control into a pumping system helps the pumps achieve a better flow accuracy without external instrumentation. In many applications, sensorless devices use pump performance data from the VFD to match a pump’s flow with its associated power curve, which leads to improved reliability and productivity. To better emphasize the importance of this technology, an example of how one mining operation used sensorless flow technology to its advantage is detailed in this section. A global producer of salt had sized and designed its water injection pumps for the maximum flow and head at peak production. However, the system curve did not match the original pump designs and fluctuated depending on the back pressure of the system. Since the pumps were designed to meet the requirements of a different system curve, they varied widely in performance. Changing well pressures forced the pumps to operate off their best efficiency points (BEPs), causing runout conditions. The plant needed to provide a constant system flow and used the sensorless flow algorithms in a smart VFD to improve production and reduce downtime. In Figure 5, the green system curve is the design operation. The red curve may be typical performance depending on the backpressure, static level, frictional losses and other factors. Despite fluctuation of the system curve, the pumps needed to maintain a constant flow. While a flow meter could have been used, accurate sensorless flow with precise data obtained from the VFD more than met the plant’s needs.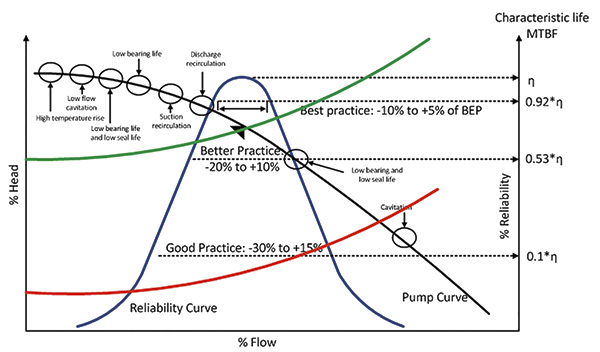
Controlling Multi-Pump Systems with VFDs
Systems with two or more pumps must be controlled differently to ensure that the optimum number of pumps operate to satisfy the process parameters and maintain the life and health of the pumps. How are these systems designed and operated by plant personnel?Benefits of Outfitting Each Pump with a VFD
All too often, operators run each pump in a multi-pump system at all times, increasing the probability that the pumps will run away from the specified curve because of excess energy consumption. To maintain a properly functioning system, each pump should be similar in size, and their output must be monitored based on the real-time application demands. Most plans have specific process demands; however, variability in processes is always present and, in a multi-pump system, each pump has specific demands as well. By equipping every pump within a multi-pump system with a VFD, plants are able to automate optimal staging and de-staging logic based on the system’s unique demand. Incorporating VFDs in a multi-pump system also ensures that all the pumps are adequately balanced to operate in harmony by using the synchronized speed and/or torque feedback generated by the device. Additionally, VFDs alternate pump operation based on runtime hours, balancing wear or decreasing chances of system failures of one pump over the other. This information can also be obtained using soft starters or torque meters with speed measurement. However, acquiring this information with a VFD allows the logic to better control a centrifugal pump according to the system requirements. If operators cannot adjust the speed of the pump, their pump control is limited. Not every pump application requires a VFD for successful operation, but for dynamic control logic, VFD use has distinct advantages.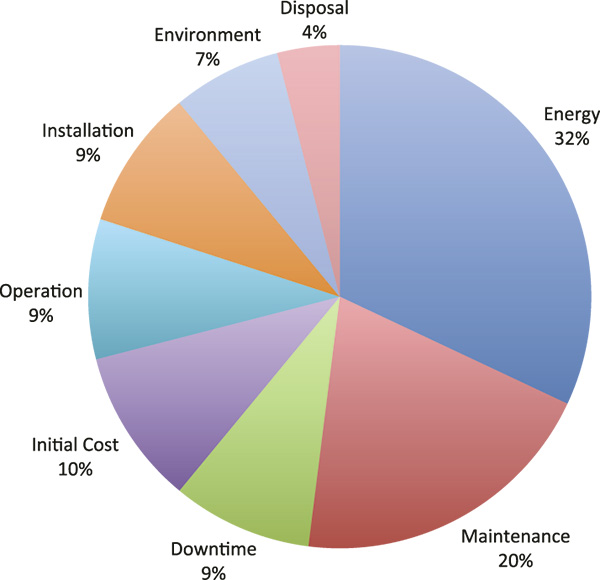