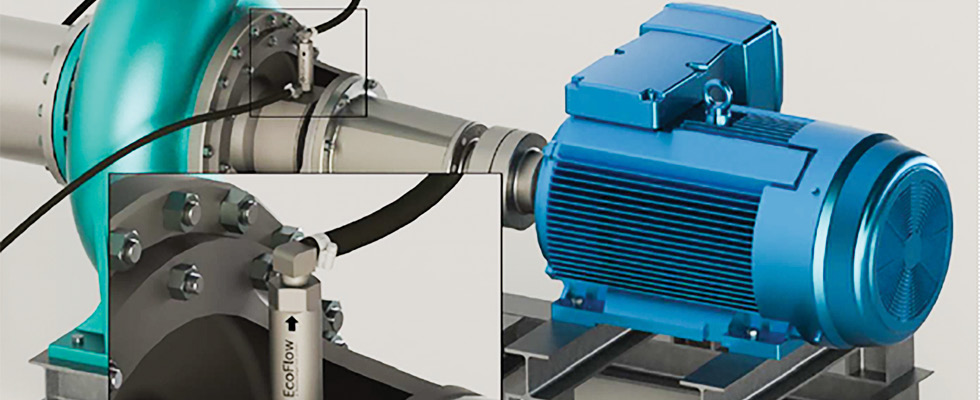
What Is a Thermostatic Valve?
Thermostatic valves are a solution to temperature problems. They can operate autonomously without external power, and their core technology, the wax motor, has existed for over 100 years in countless applications, including washing machines, dishwashers, heating, ventilation, air conditioning (HVAC) systems and even cars. Wax motors are linear actuator devices that use the phase change properties of paraffin wax to convert thermal energy to mechanical energy.
The wax undergoes a volumetric expansion of up to 20% when transitioning from solid to liquid. This expansion extends the piston within the thermostatic valve, producing a usable stroke that opens or closes the valve.
Improving Mean Time Between Failure With Thermostatic Casing Relief
Pumps operating at low or no flow (deadheading) can lead to increased temperature in the casing or volute of the pump. Extended operation under these conditions will result in accelerated seal degradation and potentially catastrophic failures of cast iron casings.
Thermostatic valves are installed on the pump casing and configured with a user-selected open temperature to provide thermal relief.
When the temperature of the water in the pump starts rising to temperatures higher than specified, the thermal actuator within the valve will modulate open, discharging the hot water. Subsequently, the valve will modulate closed again once the temperature returns to acceptable levels. This discharged water can be collected, reused or repurposed to reduce waste.
Conserving Water With Thermostatic Seal Water Control
Mechanical seals are used in pumps to prevent fluid leakage. Quench water is typically circulated around the mechanical seals to dissipate heat and prevent overheating, as overheating can lead to seal failure and pump downtime. In many applications, the water runs constantly to drain regardless of necessity, leading to inefficiencies. Integrating a thermostatic valve on the discharge of a cartridge seal or gland will automatically control the cooling water supply.
The thermostatic valve provides an optimum environment for the seal while drastically reducing water consumption and increasing cost savings. The valve automatically regulates water flow, opening when the seal water temperature reaches the user-specified set-point and closing when temperatures decrease. This eliminates the need for manual valves and ensures seamless operation.
A major United States sugar producer has several hundred pumps throughout their plant, and these pumps either require packing, which demands constant maintenance, or mechanical seals, which need a water supply to cool and flush them.
In the latter instance, the water is usually returned to a sealed tank or dumped into a drain. Any water on the floor or in a drain finds its way back to process and must be evaporated, which can lead to high costs or be sent to wastewater, resulting in an even higher price.
The plant experienced difficulties using mechanical seals on their pumps due to the significant water demand and up-front expense of a closed recirculation system. They also damaged some costly seals yearly due to accidental dry running. The plant installed thermostatic valves after learning how they could help protect mechanical seals and reduce waste. With great success and zero valve failures after two years, the plant doubled its usage to over 40 valves. Since installing the thermostatic valves, the plant has reduced dry running damages from four seals annually to zero. Implementing these valves has also reduced maintenance expenses and the amount of water sent to the drain.
An additional benefit of using thermostatic technology is allowing the facility to install double mechanical seals in places they could not have previously installed without an expensive closed-loop seal water system.