LNG benefits have increased the demand for this cleaner burning fuel and associated production and distribution equipment.
08/20/2014
Liquefied natural gas (LNG) is natural gas in a liquid form that is clear, colorless, odorless, non-corrosive and non-toxic. It is produced when natural gas is cooled to minus 259 F (-161.66 C) through a process known as liquefaction. During this process, the natural gas—which is primarily methane—is cooled below its boiling point, and certain concentrations of hydrocarbons, water, carbon dioxide, oxygen and some sulfur compounds are either reduced or removed. LNG is less than half the weight of water. If spilled on water, it will float and then immediately vaporize if under atmospheric pressure.
LNG Uses
LNG has been used as a clean burning alternative in power plants and in thousands of vehicles for decades. With the substantial growth of the LNG fuels industry around the world, the opportunity to use LNG as a cleaner and lower-cost vehicle fuel in transportation fleets and heavy horsepower equipment continues to grow.LNG Benefits
LNG has many benefits when compared with other fossil fuels. It is less expensive, has fewer emissions, and is safer and less likely to ignite.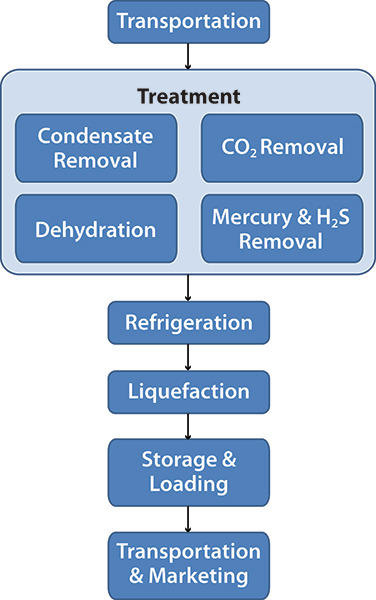
Cost
On average, LNG costs about 50 percent less than gasoline or diesel fuel and delivers the same power and performance. According to the Federal Reserve Economic Database, in 2010, the U.S. spent $552 billion on oil alone, and 61 percent of that was imported. A 50-percent savings could bring many benefits.Emissions
Natural gas is the cleanest burning fossil-based fuel with 50 percent lower CO2 emissions than the next best option. LNG burns almost completely, leaving only a small amount of carbon dioxide and water behind (CH4 + 2O2 = CO2 + 2H2O). LNG produces up to 90 percent lower emissions than gasoline or diesel. LNG’s reduced amount of greenhouse gases makes it the cleanest internal combustible fuel for our environment. It also burns cleaner inside engines, resulting in fewer oil changes and less maintenance. By replacing the traditional diesel engine of one 18-wheeler with an LNG engine, its carbon footprint reduction is equivalent to removing 324 automobiles from the road.Safety
LNG is lighter than air. In the event of a spill, LNG disperses quickly, unlike petroleum-based fuels that pool on the ground and create a fire hazard. It also has a higher ignition temperature, making it less flammable than gasoline or diesel. In addition, LNG is non-toxic and non-corrosive and will not contaminate ground water.Abundance
Canada and the U.S. sit above large natural gas reservoirs. Some analysts believe that these reservoirs contain four times the energy held in the oil fields of Saudi Arabia. During the last five years, shale reservoirs have revealed natural gas deposits that doubled previously estimated recoverable reserves.Other Benefits
Additional LNG benefits include:- Range—LNG is the only option for a truck that needs to travel more than 200 miles. Compressed natural gas (CNG) trucks must add multiple tanks, which increase the vehicle’s weight and cost to attain the same range as an LNG truck.
- Pressure—LNG systems operate at lower pressure than CNG [25 to 200 pounds per square inch (psi) for LNG versus 3,600 psi for CNG].
- Storage—As much as 2.5 times more LNG can be stored in the same space as conventional CNG systems, increasing fuel efficiencies and range.
- Horsepower—LNG offers engines that are more than 400 horsepower.
- Fuel economy—LNG provides better fuel economy. CNG is historically 12 to 18 percent less efficient.
- Weight—LNG is denser than CNG, so more fuel can be stored in smaller, lighter tanks that increase efficiencies.
- Fueling speed—LNG fuels as fast as diesel, at 40 gallons per minute. CNG slow fill takes 6 to 8 hours and fast fill takes 30 to 45 minutes. In addition, only half of the tank can be filled because of heat and pressure buildup. If a fleet operates more than one shift, CNG is not a viable fuel because the vehicles will take too long to fuel.
Design Features of Pumps Used in LNG Applications
Pumps used in LNG service are integrally mounted on the same shaft as the motor, which is submerged without coupling or mechanical seals in the LNG liquid. For a retractable in-tank application, the pumps can be installed inside the LNG storage tanks in vertical pump columns with foot valves at the bottom. This removes the possibility of tank leakage because of piping or other external problems. The pump retraction system permits the unit to be safely removed from an operational tank without venting gas vapor to the atmosphere. By enclosing the entire unit within a suction vessel built to an appropriate pressure vessel code, such as American Society of Mechanical Engineers Standard VIII, the system becomes safe and simple. The pump is factory aligned. It has no couplings and no auxiliary piping for seal purge, bearing cooling or lubrication. This makes it a lightweight, uncomplicated installation. Key factors to consider for LNG application pumps are:- Lubrication and cooling systems
- Thrust equalizing mechanism
- Bearing configuration
- Junction box assembly and electrical penetration
- Cryodynamic inducer design
- Vibration monitoring system
Design Features of Valves Used in LNG Applications
Valves used in LNG service are designed with an extended bonnet to avoid freezing the packing at operating temperatures. This allows operations to cycle valves as required. Valves manufactured for cryogenic applications should comply with type tested to British Standard 6364 or an equivalent standard. Nonmetallic materials should be restricted to polytetrafluoroethylene (PTFE) and graphite. Fire-safe design to prevent internal leakage is achieved by using resilient sealing materials that do not decompose or deteriorate during a plant fire. The edge of the metal seat retainer preloaded by the seat spring comes into contact with the ball (in a ball valve) to shut off the line fluid to minimize internal leakage through the valve bore. The seat retainer also compresses. The flexible graphite retainer packing prevents fluid leakage between the valve body and the seat retainer. A bidirectional flow sealing mechanism is employed so that each of the upstream and downstream seats of the valve adequately contacts the ball with a seat spring. Line pressure further maintains this contact method. The cavity pressure relief is designed to avoid trapped volatile liquid releasing into the downstream flow. Key factors to consider for valves in LNG applications are:- Extension bonnet—The thermal conduction and heat transmission from the low temperature fluid should be suppressed to a minimum while a cooling effect is provided. The packing is not exposed to the low temperature liquid, and a secure seal is achieved.
- Surface hardening treatment—Treatment with stellite alloy is recommended for better performance.
- Cavity pressure relief—This feature should be included.
- Seat lapping—Seat lapping is done to achieve bubble-tight zero leakage when closing a valve. After machining a seat to achieve mirror finish the seat is lapped on the lapping machine.
- Stem binding prevention—This is achieved by having a back seat in PTFE + PFA (form of fluoropolymer) construction bush.
- Low emission type packing—This helps avoid compression creep stress that’s caused while packing stem with packing.
- Design—The design needs to accommodate the prevention of abnormal pressure within the cavity. It should also be designed to have little to no pressure loss and be fire-safe.