Paper production requires large amounts of power. The Smurfit Kappa plant in Piteå, Sweden, uses its own biomass boilers to meet part of its energy needs. The cleaning system in place for the high-performance steam generator includes a specialized motor management solution to ensure uninterrupted motor operation. At the Smurfit Kappa Kraftliner Piteå paper plant in northeast Sweden, 520 employees produce about 700,000 metric tons of Kraftliner paper per year. Kraftliner is a special type of raw paper made of fresh fibers and serves as the base material for manufacturing high-quality corrugated cardboard packaging. The Swedish plant’s annual power consumption is about 520,000 megawatt hours (MWh). Biomass boilers—which burn organic material such as wood— generate 58 percent of that power, creating added value through efficiency and sustainability. The Piteå production site consists of a pulp mill with two soft-pulp digesters and one hardwood digester and a paper mill with two paper machines. Two boilers produce the energy needed for the mill. One recovery boiler combusts the black liqueur from the process, and a biomass boiler uses mostly the bark from the wood-handling system. The steam from the boiler passes across two steam turbines that generate more than half the electricity required by the mill. This self-produced electricity is a green option because fossil fuel is only required during the startup process.
Lower Costs for Cleaning Routines
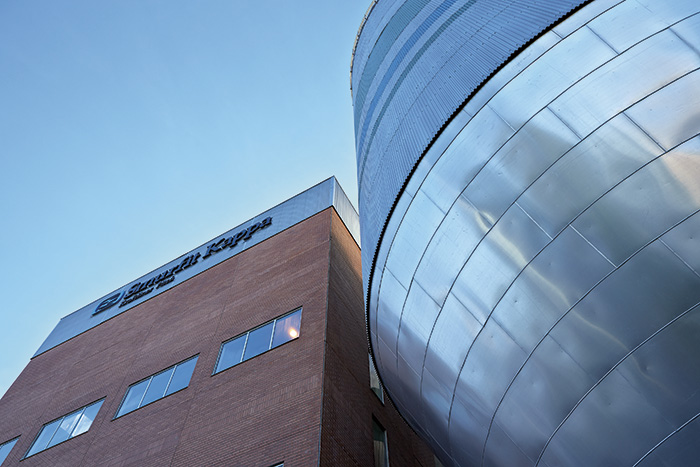
Efficiency & Maintenance Challenges
The previous electrical drives in Smurfit Kappa’s high-performance boiler were complex and difficult to use. The system required mechanical contactors for reversing the rotational direction of the steam cleansing system’s motors and digital outputs for clockwise and counterclockwise control. Analog inputs handled the power input, and digital inputs analyzed the return signals. Wire connected all the devices and individual switching cabinets. Documentation and controller programming were time-consuming with the existing system. Adding drives to the setup was a major undertaking that required expert project management.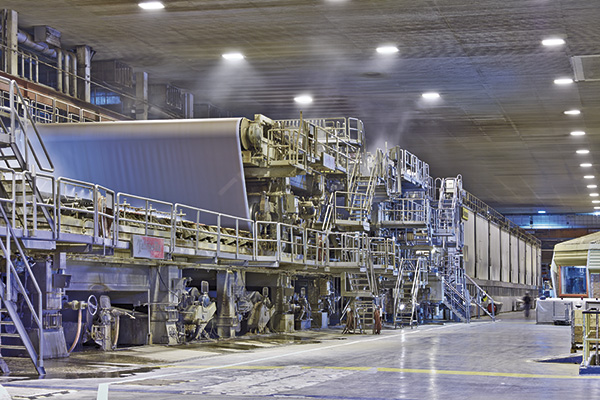
Fewer Wires, More Space
The new motor management system provided several advantages to the steam cleansing system. The program, which included motor management, hybrid motor starters and a fieldbus gateway, detected worn sootblowers before failure. Fewer I/O modules were required, reducing wiring and documentation, and the compact device dimensions opened more installation space. Bus gateways allowed for system expansion during system operation. The gateway forwarded the process data from multiple motor management modules to the control unit, while electronic motor management units (EMMs) handled monitoring and drive protection with active power monitoring. The solution also included hybrid motor starters, which provided non-wearing motor switching. Relays and the system cabling solution quickly and reliably coupled the field devices to the controller.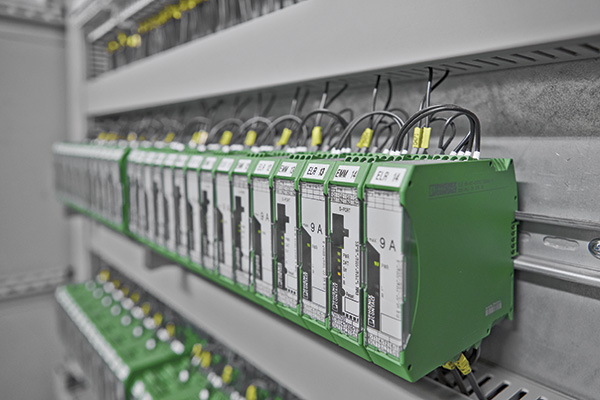
No Need for More Sensors
The 22.5-millimeter electronic motor management unit has built-in current transformers to directly read input currents up to 16 amperes. If the applications’ output is higher currents, other EMM modules read them in combination with external current transformers. The range of available components works for all power ratings. Because the EMM can be easily inserted on the existing motor cable, the operator was provided access to all the measurements for easy and cost-effective motor and system monitoring. The ease of installation eliminates the need for additional sensors. The module can retrofit existing systems, keeping the system up-to-date with all current status values. Separate mechanical or non-wearing semiconductor contactors switch three-phase loads. The digital output of the motor management modules implemented on- and off-switching. Motor management supplied the data for any application, such as monitoring and protecting pumps, controlling valves or tool machines, or analyzing the systems’ power consumption. The choice of control system connection—whether independent or fieldbus—does not impact the system’s data collection.Trusted Connections
Through the program’s fieldbus gateway, which is certified according to European Norm 50170 as specified by Decentralized Peripherals, level V1, 31 motor management modules can be connected to each other. The pluggable design means no wiring is needed (see Figure 1). All process data is transferred to the control system.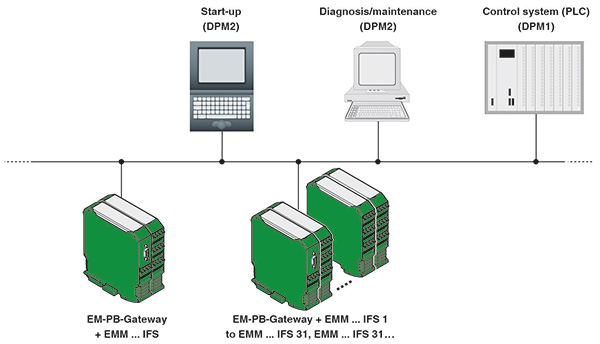