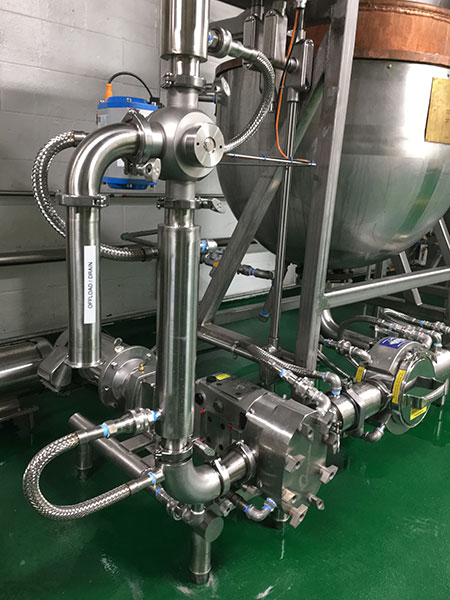
Positive displacement pumps are one of the foundational workhorses of food and beverage manufacturing plants nationwide. As positive displacement pump design has evolved throughout the years, processors now have their pick of pump brands to choose from. Deciding which positive displacement pump is best can be a tricky task. Not only must users ensure the pump is well suited for their application, but other factors must be considered to ensure maximum efficiency, minimal disruption and simple maintenance.
Pump Maintenance Requirements Are Key to Long-Term Success
Simplifying pump maintenance should be top of mind for innovative food and beverage manufacturing plants. Although always an important factor, the emphasis on ease of maintenance has grown in recent years. One reason this is now a top concern of food and beverage manufacturers is the shift in the workforce demographics and the changing talent pool. Skilled labor and experienced maintenance technicians are hard to come by. As such, the industry has placed a stronger emphasis on maintenance requirements when purchasing equipment, including positive displacement pumps.
Food and beverage manufacturers also face other challenges that emphasize the critical need for easy-to-maintain pumps and equipment. Rising operational costs and tight production schedules are two factors impacted by maintenance requirements. Ideally, pumps and equipment should operate in a manner that reduces wear and tear during normal operating conditions. Less wear and tear equates to lower parts consumption and reduced downtime for maintenance. The less frequently users take a pump offline, the better overall operational success will be. Less downtime for maintenance results in more uptime for production.
This article will dive into pump types (focusing on positive displacement pumps), when to use a positive displacement pump and four key questions to assist users with picking the perfect pump for low cost of ownership and easy ongoing maintenance.
Pump Types & Their Uses
Food and beverage pumps come in two primary categories: positive displacement and centrifugal. Each pump type has unique benefits but is designed for different applications. While the primary focus of this article is positive displacement pumps, it is important to understand the basics of both primary categories and where each is best suited for use.
- In general, centrifugal pumps are used for higher flow rate applications that are pumping lower viscous or non-shear sensitive media. Centrifugal pumps are generally found moving water-like fluids throughout manufacturing facilities.
How it works: A centrifugal pump moves fluid through rotational energy created by a motor. The fluid enters the quickly rotating impeller along its axis and is cast outward by centrifugal force. The rotational motion of the impeller accelerates the fluid out through the impeller vanes into the pump casing and toward the outlet.
- Typically, positive displacement pumps are used for pumping high viscous fluids at high pressure and low flow rates. Positive displacement pumps are also a good fit for shear-sensitive products.
How it works: A positive displacement pump moves liquids by first encapsulating a portion of the fluid and then moving it through the pump housing and forcing it into an outlet. Pistons, screws, diaphragms or other means can drive positive displacement pumps used in food and beverage manufacturing.
Positive displacement pumps are comprised of two different categories. There are reciprocating pumps that include a diaphragm, piston and plunger, and there are rotary pumps, which include screw, peristaltic, vane, gear and lobe pumps. Positive displacement pumps are characterized by their ability to move fluids at a consistent flow rate, even at high pressures.
Which Positive Displacement Pump to Pick
While selecting a centrifugal pump can be straightforward due to the often simple nature of water-like media, the various types of positive displacement pumps cover a wider range of product transfer requirements. One way to simplify positive displacement pump selection is by letting the media being moved guide the decision.
- As previously noted, highly viscous food and beverage products or ingredients typically require positive displacement pumps. Rotary lobe pumps are the usual go-to for viscous product transfer, particularly if the fluid does not contain solids.
- Positive displacement pumps are perfect for transferring fluids when it is important to maintain product integrity or structure. Diaphragm, screw or vane pumps are often used for media that contains solids or particulates that cannot be damaged.
- Positive displacement pumps can be used to move water-like fluids in applications where cell structure must be maintained, like pharmaceutical processing. Rotary lobe pumps are typically used for these applications.
Positive Displacement Pumps in Food & Beverage Manufacturing
The most widely found positive displacement pumps in food and beverage manufacturing are rotary lobe pumps. They are a staple in consumer goods manufacturing thanks to their ability to handle viscous fluids with precision, even at high pressures. With the huge install base of these pump types, manufacturers have learned to live with some design flaws that lead to excessive maintenance requirements, messy production floors and unnecessary processing interruptions.
With the expanded emphasis on simple maintenance and overall cost of ownership, many manufacturers are demanding more of their positive displacement rotary lobe pumps. Here are four questions to ask a pump provider to help pick the perfect positive displacement rotary lobe pump.
1. How often do bearings need to be greased?
Pumps are often placed in areas hard to access, making maintenance tricky, but pump lubrication is necessary. Grease or oil helps decrease wear and friction and prevents issues with bearing corrosion and performance.
Many food and beverage positive displacement pumps on the market require bearings to be greased every 750 hours, but some models last up to 3,000 hours between necessary maintenance. If slashing this critical maintenance need in thirds is important to an operation, users should ask their pump provider about the manufacturer’s recommended maintenance schedule.
2. What is the material of the standard gear casing?
Sanitary processing environments endure rigorous cleaning routines and are often subject to caustic cleaning agents. These cleaning processes, although critical to maintaining a clean processing environment, are destructive to non-stainless steel surfaces.
Many positive displacement pumps on the market today have painted gear casings. These painted gear casings chip easily and require frequent repainting, but they are not the only option. There are stainless steel gear casing options that come standard on some pump models. A simple swap from painted gear casings to stainless steel can eliminate the need for repainting for good.
3. How is the gear casing sealed?
Quality construction is important for leak prevention of a positive displacement rotary lobe gear casing. These gear casings are sealed in different ways and vary by manufacturer. Plastic plugs are used on widely known brands but can crack easily and lead to leaks. An alternative method of gear case sealing is stainless steel plugs and gaskets. This minor exchange can have a big impact on leak prevention.
4. What is the pressure rating of the pump?
Finding a pump with a high-pressure rating means users will be less likely to experience contact inside the pump. Internal contact leads to damage that could impact performance and result in repairs. The need for repairs disrupts the production schedule and can be costly when considering the number of pumps in a single plant.
In the dynamic landscape of food and beverage manufacturing, the significance of pump maintenance cannot be overstated. Positive displacement pumps stand as the backbone of production processes, so prioritizing ease of maintenance is imperative for sustained efficiency and profitability. With a shrinking pool of skilled labor and the escalating demands of modern production, the need for pumps that facilitate streamlined maintenance has become paramount. By addressing key questions regarding maintenance requirements, material durability and pressure ratings, manufacturers can optimize their operations for longevity
and success.