12/30/2013
Recently, I received a call from a plant operator in Ohio. He said, “We have a big contract from a customer to supply multiple oil heating systems and have just completed the first unit. It is ready to ship. These systems are assembled on mobile skids with a centrifugal pump that transfers oil from the tank to the filling containers. We designed the system for 30 gallons per minute (gpm) and tested each system at the shop’s test facility. When we set it up on a mobile unit and connect the suction line to the supply tank, we get different results. What’s wrong?” Steve provided the system details, which were:
- The pump is a Goulds’ 1 x 1.5-6, with a 5.12-inch impeller—outside diameter.
- The system pumps oil through a heat exchanger and then to fill containers.
- The process is mobile and has a short suction pipe, which the customer connects to the large tank to supply the filling stations.
- The pipes are sized large, especially the suction pipe, to ensure that friction losses are negligible.
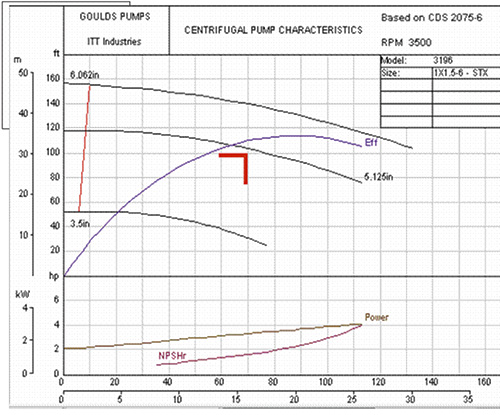
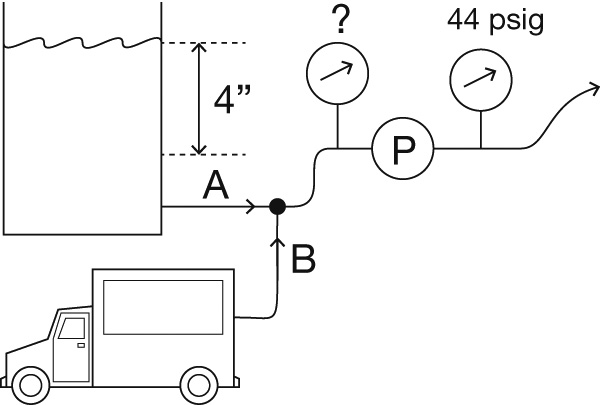