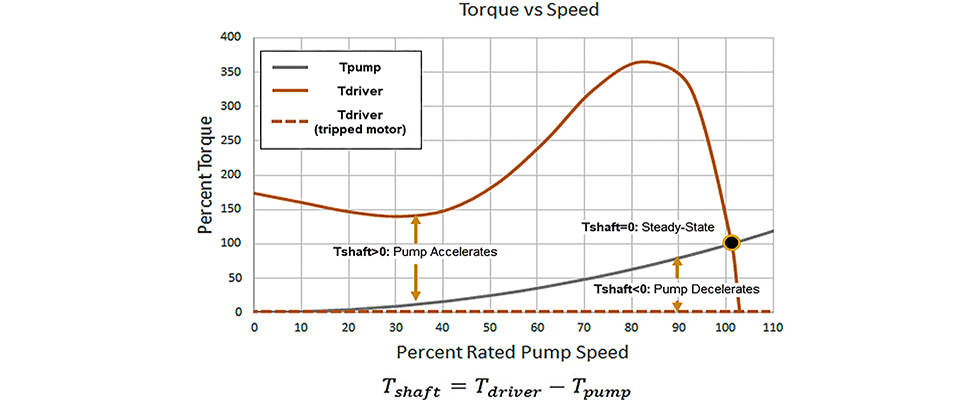
Centrifugal pumps are designed for optimal steady-state operation; however, inevitable deviations from steady state as pumps start and stop can introduce dramatic, and often dangerous, pressure responses within a piping system. Pump transients can be as routine as a startup during initial commissioning or shutting down for maintenance.
Why Should Pump Transients Be Concerning?
Often, water hammer or surge is associated with the high-pressure response following a rapid valve closure. Put simply, a valve closure converts fluid momentum into pressure as the fluid slams into a closing valve. The resulting pressure could exceed pipe or equipment pressure ratings.
Trailing fluid then slams into the stopped fluid, causing a high-pressure wave that transmits backward through the system causing unbalanced forces. These events can also cause low pressures, resulting in reverse flow, vacuum conditions or vaporized fluids at high points in the system.
While valves are the quintessential cause of fluid momentum converting into pressure (and vice versa), pumps similarly cause surge as they affect flow by the pressure they create. Suddenly adding or removing a pump pressure source will transmit high- and low-pressure waves through a piping system.
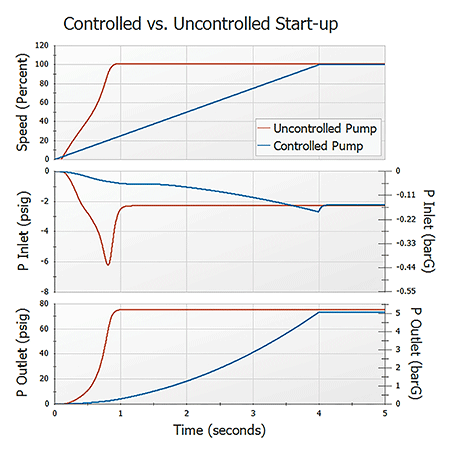
Like valve closures, rapid changes in pump operation result in more dramatic pressure and flow responses. Modeling software can quantify these effects as waves transmit and interact, providing engineers flexibility to model a wide range of pump transient causes.
What Causes Pump Transients?
Many pump transient events can be predicted. This can happen during initial commissioning of a system, through anticipating and following routine maintenance or when accommodating variable demand with additional pumps. These routine transients should follow a procedure to minimize negative transient effects by smoothing the transition between operating conditions.
There are also reactive events where the pump responds to an unplanned issue, such as equipment failure or an emergency. Power loss is often the worst-case scenario, as any processes designed to smooth a pump’s transition between states are unavailable. Power loss concerns are compounded if power is restored to suddenly restart a pump.
Multiple pumps in a single system have additional considerations, such as parallel pumps causing check valve slam if a single pump trips. Simultaneously tripping or starting all pumps will also cause surge concerns, though multiple pumps can serve as an asset to gradually transition a system between operating conditions when turned on/off incrementally.
Pump Transient Theory
Pump transients can be distinguished into two categories: controlled and uncontrolled.
Controlled pump transients use an external controller, such as a variable frequency drive (VFD), to ease a pump between states by controlling its speed. This allows the operator to gradually accelerate fluid to cause a less dramatic pressure response. Gradual changes to the system are also easier for protection systems like check valves, avoiding secondary transient effects. Controlled transients could be modeled as pump speed versus time to replicate a VFD.
Controlled transients require power to control the pump. However, following a power loss, the speed of the pump is dictated by the system. A power loss pump trip demonstrates an uncontrolled pump transient.
Uncontrolled does not imply a pump transient is unpredictable, but that a pump’s behavior is dictated by the system rather than a fine-tuned electronic controller. For example, a routine pump startup might start against a partially closed valve or check valve to avoid runout, then the valve would be gradually opened to achieve the intended operating point. Although the overall process is routine, the pump is simply turned on and develops flow depending on its surrounding system.
A Delicate Balance of Torque
While VFDs offer one surge mitigation approach, engineers can similarly mitigate surge by understanding the underlying mechanics of uncontrolled pump transients. This understanding is critical in power loss circumstances where there is no alternative to control the pump.
Uncontrolled pump transients depend on the rotational mechanics of the pump and its system. At steady state, all component torques are applied to the pump by the motor and fluid balance. This point is labeled in the torque versus speed diagram in Image 2. However, during a transient, the pump accelerates due to unbalanced torque. In the case of a pump startup, the motor applies more torque than the system’s resistive torque, accelerating the pump. In the case of a pump trip, the motor torque goes to zero and the pump decelerates, potentially reversing direction if unaddressed.
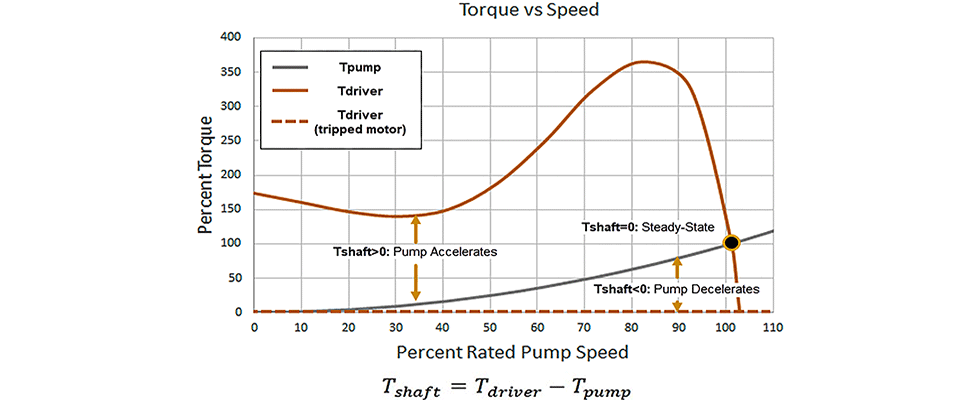
The rate of acceleration depends on the inertia of the pump impeller and fluid, so it can be modified to create smoother transitions between states. This is often why pumps, especially large pumps, attach flywheels to increase pump inertia. The increased inertia is beneficial in both startup and shutdown cases to ease between operating states.
Considering this, interaction between torque, inertia and the surrounding system is critical to modeling uncontrolled pump transients accurately.
Addressing Pump Transient Concerns
General surge concerns are mitigated by smoothing the transition between states. Controlled pump transients can adjust how pump speed gradually ramps up/down. Uncontrolled pump transients, however, require changes to the pump itself or the surrounding system to mitigate surge.
For routine uncontrolled transients, an operational procedure to change surrounding valves before startup or shutdown may reduce water hammer effects. Similarly, incrementally turning pumps on and off in multipump systems may smooth the overall system response.
In reactive cases, the system must instead be modified to passively reduce potential for surge. These modifications might add a surge vessel to supplement flow, increasing pump inertia with a flywheel, using stronger pipes, switching to nonslam check valves or sizing relief systems to accommodate pressure increase.
In all cases, it is recommended to use software to model a predicted transient response, considering routine and worst-case scenarios, to confirm the physical system will operate within requirements. Due to the complexity of interacting components and interacting wavefronts, surge analysis is understandably difficult, and simplifying hand calculations are not always conservative.
Software could assess many causes of surge to help in developing mitigation strategies, such as justifying a VFD or advocating for additional equipment.