Size will have a major impact on all essential parameters.
Meccom Industrial Products
04/10/2019
Gathering all the information available regarding a system using an expansion joint is of utmost importance. It is the only way to reach the design life expectancy of any expansion joint. There is no such thing as too much information when it comes to the selection process. The acronym “STAMP” can be beneficial in remembering all the essential parameters. STAMP stands for:
- Size
- Temperature
- Application (movements—axial, lateral and angular)
- Media
- Pressure
- The elastomer itself
- The reinforcement material
- The design and interaction of the different material
- The interaction with the flange attachment
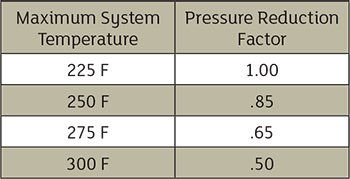
Material Considerations
All elastomers have temperature limits. There is a range of temperatures in which elastomers will remain pliable and elastic. If the temperature is below the glass temperature, the elastomer will lose elasticity and will not be able to respond to the required motion. When temperatures get near or exceed the higher limit, the elastomer can get hard and brittle, leading to cracking, and expansion joint failure is bound to occur. The most sophisticated and strongest reinforcement material could be used, but it will be ineffective if the elastomer is not maintained within its temperature range.Temperature & Pressure
Maximum pressure and temperature limits cannot be considered separately. As temperatures increase, the pressure capabilities of an expansion joint are reduced. Image 1 shows a general guideline of derating the pressure capability based on temperature level for ethylene propylene diene monomer (EPDM) or butyl elastomer. Thus, at 300 F the catalog-rated pressure limit must be reduced in half to ensure reliability and operating life. If the temperature exceeds the capability of an elastomer, a different compound with a higher temperature limit can be selected. Image 2 lists temperature limits for common elastomers.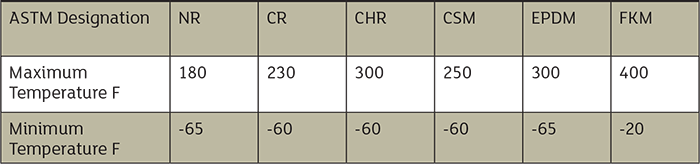
Reinforcements
There are four basic fabrics used as reinforcements in elastomeric piping expansion joints: polyester tire cord, aramid fiber (Kevlar), fiberglass and nylon. Nylon is rated at a max temp of 230 F, polyester tire cord 300 F and Kevlar/fiberglass up to 400 F, which is higher than any other elastomer except fluoroelastomer. It is important to match the max elastomer capability with the maximum fabric reinforcement capability to achieve the highest expansion joint capability. Due to differences in the coefficient of thermal expansion for the various material, conservative evaluation should prevail.PTFE Molded Expansion Joints
Polytetrafluoroethylene (PTFE) is generally rated for over 400 F, but this limit is not for expansion joints when used for pressure retention. It is not recommended to use molded PTFE joints at over 300 F.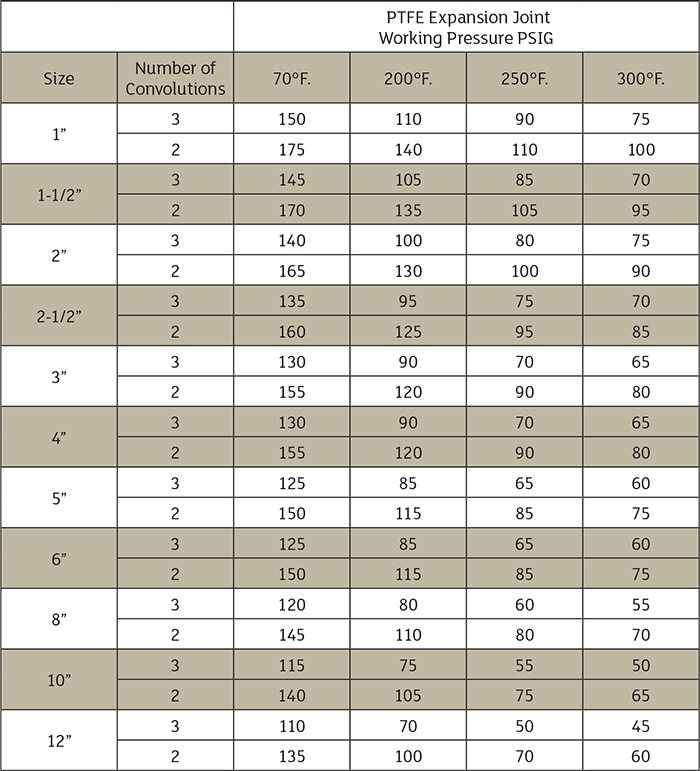
Expansion Joint Size
Another factor is expansion joint size. The larger the size, the lower the ability to handle pressure, including negative pressure or vacuum conditions. This must be added to the limitations from the reduction in pressure capability at elevated temperature conditions. Image 4 shows the pressure limits to be used considering process temperature and the size for an elastomer expansion joint.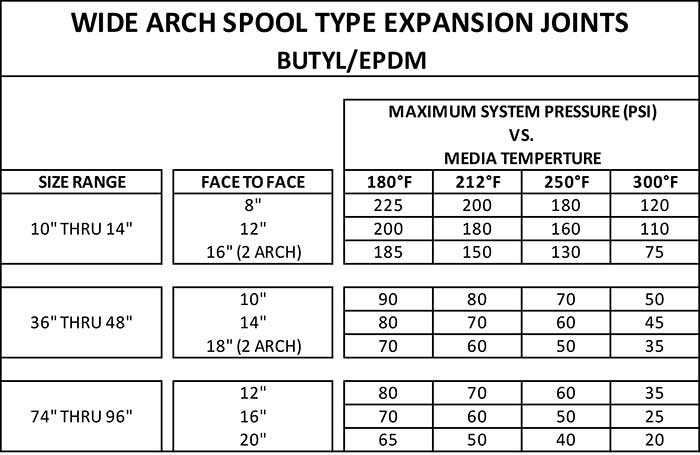