A seal manufacturer addresses common end user confusion and offers a crash course.
Carbide Derivative Technologies Inc.
02/12/2018
I recently attended the Turbomachinery and Pump Symposium, produced by the Texas A&M Turbomachinery Lab. I’ve been attending this conference off and on for 25 years and always sit in on the discussion groups for pump users and mechanical seal users. The same topics come up year after year. Those topics are new for some of the people in the room, but those with decades of experience have heard them all before. There are two reasons why this happens:
- Centrifugal pumps were designed more than 100 years ago, mechanical seals about 80 years ago, and their basic design has not changed.
- New people are entering the industry and need to learn from those with decades of experience. If mechanical seal users keep my “top 5” in mind, they will avoid many of the problems I have been hearing about for 25 years.
1. Mechanical Seals Need Lubrication and Parallel Faces.
A mechanical seal is mysterious to most users, but its design is very simple. It consists of two parallel faces sliding past each other. Image 1 is an example of a 90-year old mechanical seal patent (USPTO#2,100,220, issued 23 Nov 1937).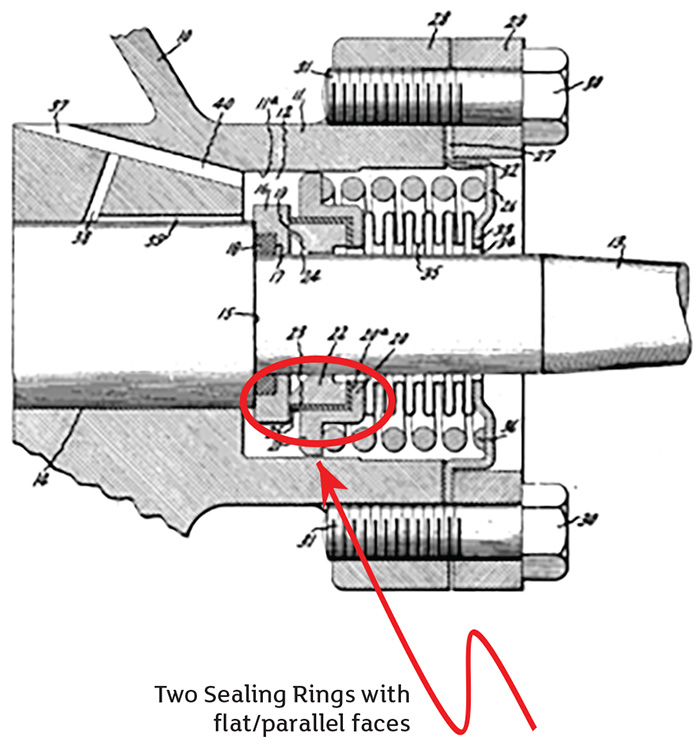
2. Seals Naturally Leak and Wear.
The hydrodynamic lubricating film will separate and the sealing faces, which provides a leakage path. This is natural, normal and held to a minimum with proper design. The film’s separation and lubrication also prevents wear in normal operation. Theoretically, the seal would last forever in normal operation. Wear occurs in stop/start conditions when the film collapses and the faces come into contact. Abrasives between the sealing faces can also cause accelerated wear, so seal support systems are used to minimize this. Wear also occurs in process upset conditions.3. Seal Failure Is Usually An Indication of Problems Other Than The Mechanical Seal.
If all conditions of No. 1 and No. 2 are met, a mechanical seal will not fail but will only need to be replaced due to normal wear. If a seal fails prematurely, it is because it was robbed of lubrication or the face parallelism was upset. The seal cannot do this on its own, so a seal failure is usually an indication of something else in other parts of the fluid loop that robbed the lubrication or upset temperature or pressure. Dry running due to a lack of pumpage in the pump is a typical failure mechanism. Excess pressure against the seal due to process upset causes mechanical deformation and is a typical cause of the faces going out of parallel. Image 2 shows such deformation, which causes the out-of-parallel condition and the outer diameter (OD) edge of the rotating face to come into contact with the stationary face.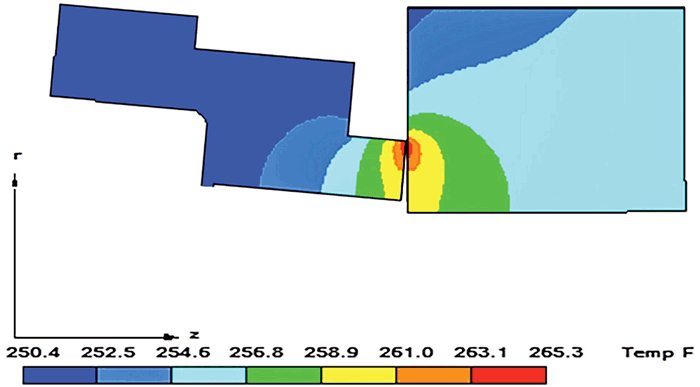