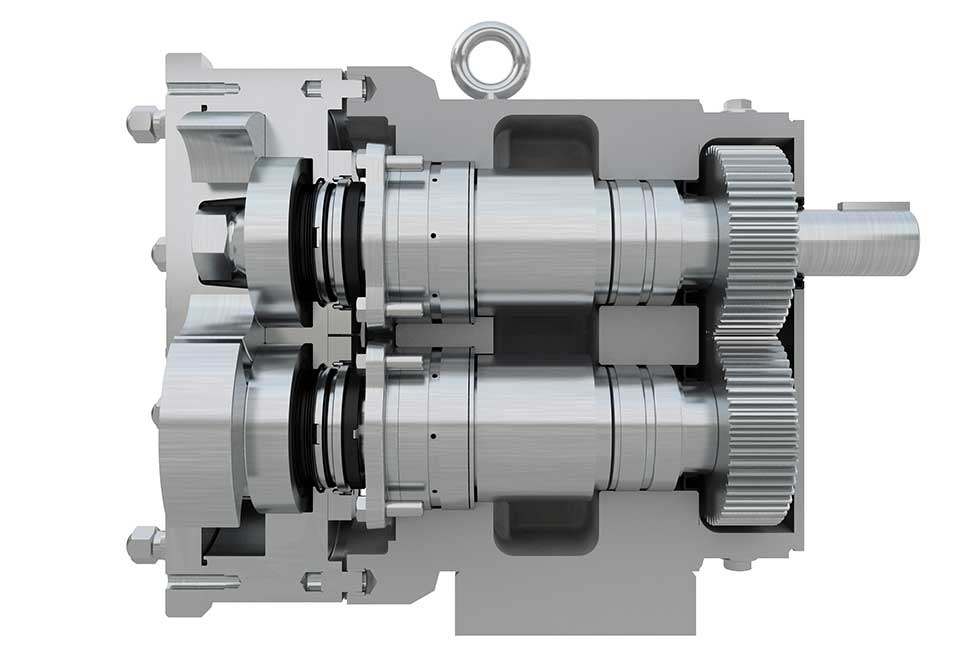
In the food and beverage industry, many pumping applications require strength and reliability, but they also require gentle handling to preserve the integrity of products. Customers do not want to receive ground beef that is more like liquid than meat, and they do not want apple pie filling that looks like applesauce. Clear understanding of the needs of the application is critical to finding a solution or resolving an issue that is affecting productivity or efficiency.
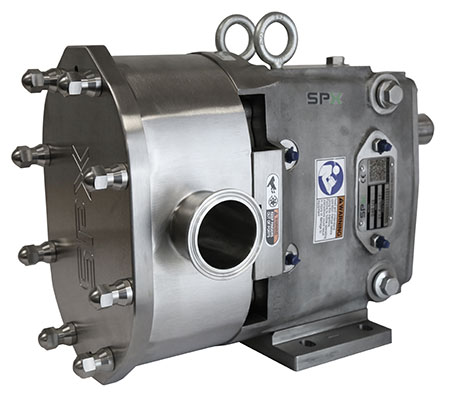
Pumps serving the food industry need to handle difficult product flows and ensure hygienic performance. How the product is handled can affect texture, taste and product appearance. An optimum solution also needs to provide efficiency, consistent performance, reliability, cleanability and straightforward maintenance.
Positive displacement (PD) pumps provide smooth, pulse-free pumping and modern designs offer cleanability, making them a popular choice in food applications. Large rotor fluid cavities and anticavitation ports mean PD pumps can handle viscous flows and products with large particles. Units that are designed with tight internal tolerances also have low slippage, which increases pumping efficiency and sanitary performance. Clean-in-place (CIP) models further lower maintenance overheads and increase availability by reducing the need to disassemble and reassemble units, which additionally lowers the risk of introducing maintenance errors.
Pump seals can be a problematic area in food processing. Any product residues that remain in the pump after cleaning present a potential risk of contamination for subsequent product batches and can become an ideal breeding ground for microorganisms.
Completely sealing the pump rotor and shaft from the product zone will further improve hygienic performance of a PD pump. Not only does this help to stop any contamination of the product flow, but it also can assist in preventing corrosion of pump internals, especially if acidic or abrasive products are being handled. Keeping such products away from the pump internals helps increase reliability and extend pump life. Another sealing area that can present issues when pumping products with fruit seeds and/or spices is the cover O-ring. It can create a pinch point that will trap these small particles. Using an L-gasket with a flat face removes the opportunity for particulates to accumulate, while allowing the CIP solution to reach all areas of the pump cover. This ensures the best cleaning outcome.
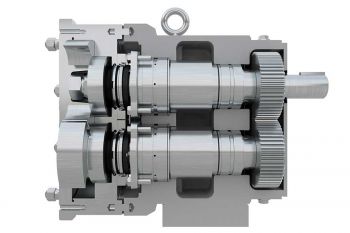
A reliable pump is needed to maintain productivity and control production costs. A robust frame design is fundamental to protecting the pump from damage. Large diameter shafts and reduced overhung loads help increase pump life. Positive lubrication of bearings, double tapered bearings and designs that do not have bearings in contact with process fluids are other features that can extend service life.
Some food processes can be challenging and require specific pump features to achieve the required performance.
These examples show some challenges with ground beef, glaze for sweet snacks, and yogurt, all of which were overcome with a change to PD pumps or by adding a pump with a specific feature.
Ground Beef
This application involved pumping cooked ground meat from a cooker to the holding tank on a package filling machine. A PD pump with external circumferential piston-style rotors offers a good solution for this type of application as the large pump cavities reduce shear and help to keep the form of the meat. The hot grease from the cooked meat acted as carrier fluid and tight clearance on the pumps ensured the grease was pumped along with the meat. The customer application problem was that meat was packing behind the rotor, requiring regular disassembly and manual cleaning of the pump and resulting in loss of productivity. The more the meat became packed, the more grease was being squeezed out of it and the harder it became.
After investigation, it was found that more flow was required behind the rotor to allow increased circulation of product. A slotted rotor was devised and added to create more space and increase circulation behind the rotor hub. This stopped the meat from becoming trapped and made CIP cycles effective, removing the need to regularly disassemble the pump for cleaning. The improvement greatly increased productivity and reduced maintenance overheads.
Glaze & Coatings
For all their sweetness and appeal, glaze and coatings on sweet snack foods can be one of the toughest applications. They are sticky and abrasive and pose a real challenge for processors. Whether it is going on a snack cake, honey bun or donut, viscosities can change during processing. In some cases, a processor may be able to use a centrifugal pump to transfer the coating or glaze to a curtain or bath, but in other cases, a PD pump is a better option. For example, chocolate glaze used on products such as donuts is a dilatant, or shear thickening material.
The shear created from a centrifugal pump means the glaze will get thicker during the day and operators may need to add oil to the recipe to keep it pumpable. The problem is that, over the course of the day, this changes the recipe. By changing to a PD pump, the gentler handling of the glaze negates the need to add oil throughout the day. Narrow face seals work well against the sticky, chocolate frosting, and the increase in reliance greatly reduces the need to open the pump, thereby minimizing risk of manual errors in the process line.
Yogurt
If a yogurt contains pieces of fruit, it requires gentle handling to preserve texture and form. But the seeds from this fruit, particularly strawberry and raspberry seeds, can accumulate in the “pinch point” around the cover O-ring. Even after CIP, one yogurt processing plant had to remove the front cover for manual cleaning. This slowed productivity as the plant could not immediately move on to the next product, as well as introduced more risk of human error because of the manual cleaning operation. Changing to a PD pump with a flat, profiled cover gasket instead of an O-ring stopped the seeds from accumulating. This reduced maintenance overheads, increased productivity, and provided a solution that was cleaned more thoroughly during CIP cycles.
PD pumps offer a solution for transferring difficult, viscous fluids that require gentle handling. Advances in this technology address challenges that arise from modern food processing applications. They can provide low slippage and low shear; provide a robust, reliable solution; and, cleanability for those that are designed specifically for hygienic applications. Whatever pump model is selected, a detailed understanding of the application and process is required to overcome some of the tough challenges in food applications.