07/31/2014
Q.What are “nonclog pumps,” and in what applications are they used?
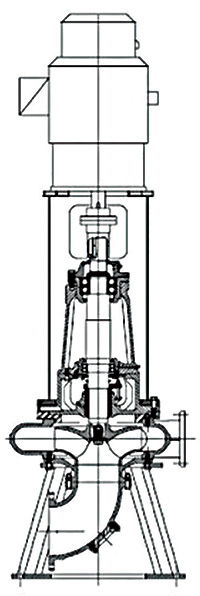
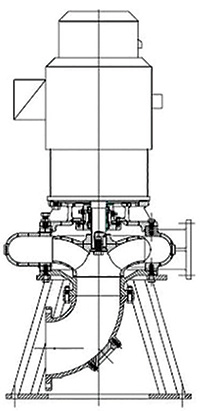
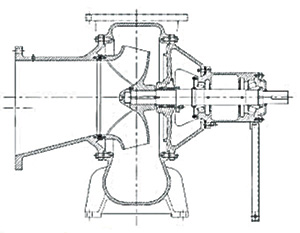
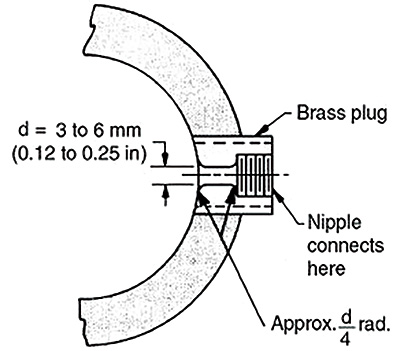
- The opening in the pipe should be perpendicular to the wall of the liquid passage.
- The wall of the liquid passage should be smooth and of unvarying cross section for a distance of at least the larger of two pipe diameters or 12 inches (300 millimeters) preceding the orifice. All tubercles and roughness should be removed with a file or emery cloth.
- The opening must be of a diameter between 0.125 and 0.25 inches (3 to 6 millimeters) and a length equal to twice the diameter.
- The edges of the opening should be provided with a suitable radius tangential to the wall of the liquid passage and should be free from burrs or irregularities. Figures 3.6.9a and 3.6.9b show two suggested arrangements of taps or orifices in conformance with the above.
- Manometers, when used on very viscous products with wet lines interfacing directly or indirectly, require larger inlet taps into the pipeline to avoid excessive lag time for fluid to stabilize in the measuring system.
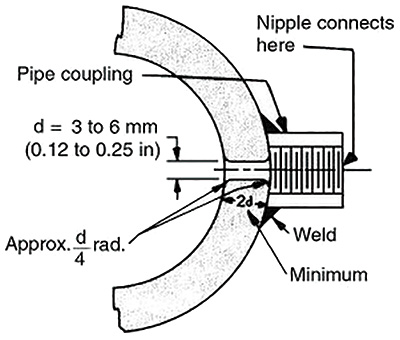
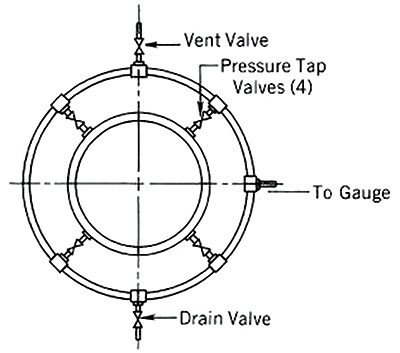