Effective predictive maintenance requires a commitment to a comprehensive program, which can result in cost savings.
07/27/2016
Editor’s Note: This article is part of an ongoing series by the author covering topics related to predictive maintenance.
When pump professionals discuss condition-based maintenance (CBM)—or predictive maintenance (PdM) as it is referred to in most circles—vibration monitoring is generally what comes to mind. While it may be a popular topic of discussion, vibration monitoring is arguably the least understood PdM technology out there. It is a complex science made even more complicated by a focus on the tools rather than the fundamental reason the tools are used.
Much of the discussion surrounding vibration monitoring focuses on what the different technologies can and cannot provide while ignoring the importance of a comprehensive maintenance program that can improve the dynamic condition of rotating equipment.
Failure Prevention
When meeting with pump professionals who are interested in starting a vibration monitoring program, I begin by asking the following question: What is your motivation behind obtaining a vibration monitoring program? What do you want this PdM technology to accomplish? I would love to hear people say, “I want to monitor the dynamic condition of my rotating equipment and enhance overall machine condition over time. This will improve my bottom line by minimizing the probability of failure. It is an investment in good maintenance practices.” Instead, this is what I often hear: “I want to find bad bearings.” The few who provide the first answer likely have a management style of preventing or mitigating failure. Those who give the second answer are usually in a reactive mode. At this point, they are not looking to prevent failure or extend service life; they just want to build a schedule around equipment failure. The attitude behind the second answer is predominant on an international scale, crossing disciplines in all industries. When CBM/PdM monitoring goals are failure-based, the technology provides only partial benefit. With the limited goal of detecting failure, operators only maintain profitability by managing production outages. In other words, a facility still has the same number of outages with the sole benefit of fewer unplanned events. Embracing failure prevention as a business goal, however, extends service life and allows facilities to reduce the number of outages. This goal improves profitability.Understanding Vibration Monitoring Technology
Regardless of a facility’s goals—either failure prevention or failure detection—understanding the following categorizations of vibration monitoring technology can help users save significant amounts of money on monitoring equipment and training. This allows the facility to focus its resources on developing a structured and effective maintenance program. Please note that the following discussion is focused on equipment that uses rolling element bearings and situations where vibration is measured at the bearing cap. This discussion is not specific to machines that use sleeve-type bearings, where shaft vibration is generally measured directly using a proximity probe. While bearing type and measurement locations differ depending on the application, discussions about measurement technology typically still apply. Vibration monitoring technology is broken down into two basic frequency ranges: low-frequency and high-frequency.Low-Frequency Monitoring: 0 to 2 Kilohertz (kHz)
This range of the frequency spectrum is used to determine equipment condition. Specifically, alignment, balance and structural deficiencies (including resonance) are identified in this range. These conditions shorten bearing life, crack housings and cause ergonomic issues. Generally, a thorough spectrum analysis within this frequency range is completed early in the machine’s life (for example, at startup or acceptance, after installation). Any corrected deficiencies are considered to be one-time efforts. A quick check of overalls (peak or root mean squared [RMS] signal amplitude, commonly called broadband or filter out) should be completed semi-annually, after major repairs and alterations are made to the machine or its associated system. This task ensures that any material changes do not inadvertently cause vibration problems. A thorough or full spectrum analysis need only be repeated when a large jump in the overall is detected.High-Frequency Monitoring: 5 to 40 kHz
Several technologies are specific to this frequency range. Two predominant commercial technologies are shock-pulse and high-frequency enveloping (signal demodulation). Both are based on pulse theory. Simply stated, pulse theory looks at a constant amplitude across an infinite frequency range caused by a single impulse in the time domain. Monitoring this range of the frequency spectrum using these technologies is specific to identifying rolling element bearing defects and, in some cases, may be applicable to gear train faults. Depending on the technology used, bearing faults can be detected as early as 12 months in advance of an actual audible indication. Shock-pulse and simple envelope amplitude monitoring are easy to teach, work well with formal lubrication programs and fit within most autonomous maintenance efforts. At a minimum, bearing condition should be evaluated by one of these technologies on a monthly basis.Technology Options
The next important concept to understand is the different types of devices that can monitor in these frequency ranges. For low-frequency monitoring, there are two basic choices: a digital box or an analog device. There is a major difference in cost, training and the experience required to use each. One should also note that the majority of existing vibration-related national and international consensus standards (ISO, ASME, ANSI, AMCA, Hydraulic Institute, API) that help define factory and field acceptance, as well as performance criteria, are based on the use of an analog device. Many standards were never written or intended for the digital world.Low-Frequency Meters
An analog vibration meter is a low-frequency vibration measurement device that is basically a simple voltage meter designed to monitor the output of an inexpensive accelerometer. The meter uses op-amp(s) to integrate acceleration to velocity (first integration) and displacement (second integration). The meters generally provide peak, peak-to-peak and RMS values. The frequency range is limited to 1 to 2 kHz through the use of a simple low-pass filter. Some of these analog-based meters may include signal conditioning for high-frequency monitoring. This meter, based on its circuit simplicity and limited display options, is inexpensive and easy to train on. A digital vibration analyzer is a computational device that digitizes an analog alternating-current (AC) signal and then, through software or firmware, provides a visual reproduction of that AC signal (time domain). Through a fast fourier transform (FFT) algorithm, the device provides a visual representation of frequencies within a selected bandwidth (frequency domain). The device can be programmed to provide peak, peak-to-peak and RMS overall values and to calculate the conversion between acceleration, displacement and velocity. This digital vibration analyzer can be used with various input devices—virtually any AC voltage input. Some of these analyzers include signal demodulation (enveloping) circuitry. In other words, the device may include analog high-pass or band-pass filters plus a rectifier circuit as an AC signal conditioner for high-frequency monitoring. This type of meter, based on the sound boards that digitize the signal, processor, memory, display and generally proprietary firmware, is expensive and can be 10 times the price of analog devices. Plus, any associated software is typically licensed to each user. These meters also require a dedicated training effort (at least 40 hours) and many hours of experience.High-Frequency Meters
Two variations of high-frequency meters are the shock-pulse device and the enveloping device. A shock-pulse device is basically an analog voltage meter that measures broadband background noise. Through a mechanically tuned accelerometer (spring-mounted accelerometer), the meter also measures voltage spikes caused by ball-to-race impacts (pulses) in a bearing. The pulses raise the noise floor across the frequency spectrum, exciting the accelerometer assembly into resonance and giving a momentary higher voltage indication. The resonance frequency of the accelerometer assembly is approximately 32 kHz, well above the noise (vibration) floor of general equipment operation. An enveloping device is a high-frequency demodulating device that is based on AM radio technology. This device is a basic analog voltage meter that measures the AC signal from a standard accelerometer. The analog signal is processed through a high-pass filter and a rectifier. Generally, the high-pass filters on these devices only allow frequencies above 5 kHz to be monitored. Noise from the ball impacts is filtered, amplified and measured as voltage amplitude. Like with shock-pulse devices, the filtered frequency range is well above the noise (vibration) floor of general equipment operation. As the signal amplitude increases, a correlation between general bearing condition and noise (voltage) can be assumed. Both shock-pulse and enveloping devices, based on their circuit simplicity and limited display options, are inexpensive (similar in price to an analog vibration meter) and easy to train on. While there are exceptions to these generalities, the devices listed are typically what is available in terms of handheld and installed monitoring technology.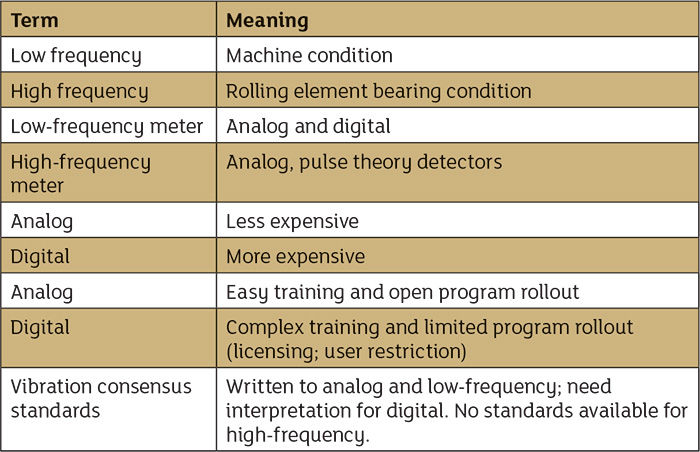
Deciding on a Solution
For those developing vibration monitoring programs, a chrome-plated digital analyzer with a single-user license at $17,500 may not be the best place to start. Instead, a $1,700 low-frequency analog meter and a $1,700 high-frequency bearing checker may be a better initial investment. To kick off a program, there is nothing wrong with using business-critical equipment to monitor and an Excel Workbook to trend data. For those who insist on a program just to “find bad bearings,” two or three high-frequency bearing checkers, four hours of training for your entire maintenance staff and an Excel Workbook to archive the data are all you need—an open rollout (multiple users) bearing failure detection PdM program for under $5,000, which is less than one-third the cost of just one digital analyzer. While vibration monitoring should be about more than “finding bad bearings,” this example shows that more is not always better. Regardless of your overall maintenance goal, a basic understanding of available technology can help your facility improve the bottom line. A commitment to enhancing the condition of your rotating equipment, combined with the implementation of an effective predictive maintenance program, is necessary for maximum savings.
See other Maintenance Minders articles here.