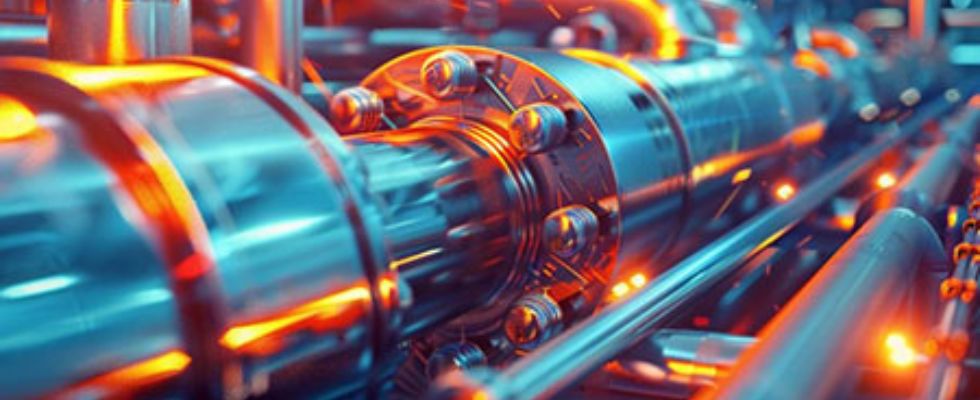
Dive into the captivating world of fluid dynamics, where the complex dance of liquids within piping systems often leads to cavitation—a common yet destructive force. For engineers tasked with maintaining the integrity of fluid systems, understanding and combating cavitation is a crucial skill that can prevent costly failures.
This comprehensive guide navigates through the watery world of cavitation in pipes—not within pumps or impellers—offering insights, strategies and preventive measures for ensuring system robustness.
A Deeper Look at Cavitation in Piping
Cavitation, at its heart, is the formation and subsequent collapse of vapor cavities in a liquid flow. When the local pressure passes through a restriction orifice plate and/or flow control device and the fluid drops below the vapor pressure, tiny voids, or “bubbles,” form.
These vapor bubbles travel with the fluid’s flow and, upon encountering higher pressure areas, collapse with great force—a process known as implosion. In piping systems, this repetitive formation and collapse of bubbles can lead to a host of complications, ranging from noise and vibration to severe damage to pipe infrastructure.
The significance of cavitation in fluid dynamics
The implications of cavitation extend beyond mere mechanical failures; it is a critical parameter in the performance and efficiency of many fluid systems, from hydraulic equipment to maritime propulsion. In pumps and valves, for example, cavitation can reduce flow efficiency, increase erosion and even alter the mechanism’s response to control signals.
How cavitation affects piping systems
Cavitation-induced problems vary based on factors such as fluid properties, system design and operating conditions. An innocuous case could manifest as a hum or a gentle water hammer, providing early warning signs, while severe, sudden onset cavitation can lead to the catastrophic failure of system components.
Detecting Cavitation
Cavitation in piping can be caused by high flow rates (gallons per minute [gpm]) needing a slight pressure reduction (pounds per square inch [psi]) through a restriction orifice or flow control valve. This can lead to vapor bubble formation and collapse, which can damage the system. Advanced flow control technologies and proper system design are essential for preventing this issue.
The earlier users detect cavitation, the more effectively they can intervene to prevent damage. Recognizing the red flags and utilizing appropriate detection tools is pivotal in the quest to keep piping cavitation-free.
Common signs and symptoms
Common signs include unusual noises, vibrations and degraded system performance, which can be attributed to cavitation’s influence on energy dissipation and flow characteristics.
The Impact of Cavitation
Cavitation goes beyond creating noise and disorder; it acts as a vital sign of deeper problems threatening the structural integrity and operational efficacy of piping systems. This exploration examines the detrimental effects of cavitation, using real-world examples of failures in piping systems to underscore the insights.
How to Mitigate Cavitation
Mitigating cavitation requires a multipronged approach that starts with understanding its root causes and contributing factors. Be it design changes, material improvements or operational adjustments, preventing cavitation is a team effort that relies on engineering expertise and careful planning.
Strategies to Mitigate Cavitation
Mitigating cavitation requires a multifaceted approach that includes design improvements, operational adjustments and, at times, system modifications. Effective measures typically ensure the fluid’s pressure remains above its vapor pressure throughout the system, preventing vapor bubble formation. Strategies for achieving this include:
- Maintaining adequate pressure: By tweaking operational parameters, it is possible to keep the fluid’s pressure above its vapor point, thwarting vapor bubbles.
- Pump selection and placement: Selecting pumps that match the fluid’s characteristics and the system’s requirements can significantly diminish the risk of cavitation. Moreover, strategically positioning pumps within the system can help sustain the necessary pressure levels.
- Pipe sizing and layout optimization: A well-designed piping layout that minimizes abrupt directional changes or fluctuations in flow rate can help preserve uniform pressure levels, thereby reducing cavitation potential.
- Cavitation suppression devices: In certain scenarios, when the above three fail, integrating cavitation suppression solutions like anti-cavitation restriction orifices and/or electronic flow control valves offers a targeted and effective means to combat pipe cavitation.
Prevention is always better than a cure, especially when dealing with cavitation. Let’s walk through the tactics and technologies engineers can employ to sidestep cavitation’s destructive path, from system design considerations to operational best practices.
Engineering solutions for prevention
Designing systems with cavitation in mind, such as using properly sized components, designing for smooth and uniform flow and incorporating energy-dissipating features, can greatly reduce the likelihood of cavitation occurring.
Operational and maintenance best practices
Observing proper operating conditions and performing regular maintenance can go a long way in mitigating cavitation’s effects. This includes monitoring and controlling fluid pressure, temperature and cleanliness, as well as ensuring mechanical components are aligned and operate within design specifications.
Future Trends & Technologies
Exploring emerging trends and technologies unveils potential futures in cavitation management. The advent of predictive maintenance and state-of-the-art materials marks the beginning of an era aimed not just at repairing systems but proactively protecting them from the effects of cavitation.
The study of cavitation in piping systems is currently fascinating, driven by numerous experiments and insightful articles by innovative engineers. These valuable contributions are paving the way for new solutions and deeper insights into cavitation dynamics.
Recent research highlights a shift toward using advanced simulation tools and harnessing machine learning to predict cavitation more accurately. By embracing these state-of-the-art technologies, engineers are crafting sturdier piping systems that can withstand cavitation challenges while maintaining efficiency.
Advancements in Fluid Flow Management: Beyond Multistage Restriction Orifice Plates
The evolution of fluid flow management technology has advanced beyond the use of multistage restriction orifice plates or manual flow control valves, which were once common for managing high-pressure drops in fluids.
Today, more efficient and effective solutions have taken precedence, including three-dimensional, single-stage restriction orifice plates with anti-cavitation properties, updated flow control valves and precision pumps equipped with variable speed drives (VSDs).
These innovations offer improved performance, precision in fluid control, energy efficiency and reduced operational costs. The shift toward these advanced technologies reflects a broader industry move toward more reliable, sustainable and cost-effective fluid management solutions, leaving multistage restriction orifice plates or manual flow control devices a method of the past.