Hydraulic Institute answers questions on rolling element bearings and grease as a lubricant.
06/13/2019
What viscosity oil should be used with rolling element bearings?
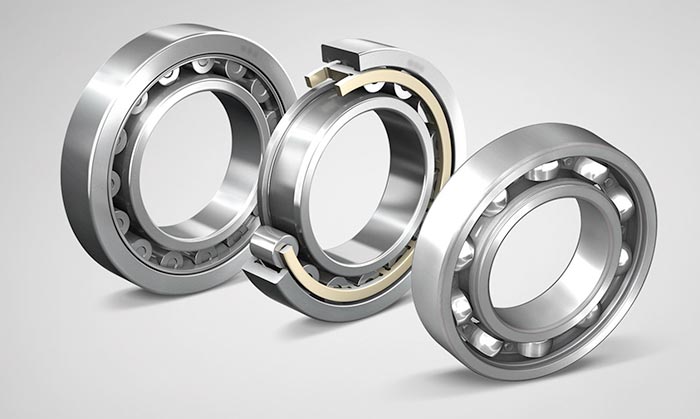
- Full film denotes the presence of enough lubricant to ensure complete separation of the moving surfaces. They are also known as hydrodynamic full film.
- Elastohydrodynamic (EHD) is when a hydrodynamic film is formed by applied pressure or load. They are predominantly found in rolling element bearings.
- Boundary layer is sometimes referred to as thin film lubrication and is usually the result of insufficient lubricant supply. Although lubrication is present, there is not enough to prevent metal-to-metal contact.
- limited heat dissipation
- overpressurization during regreasing that can damage bearing shields (to avoid, follow manufacturer procedures to prevent overpressurization)
- higher frictional heat from grease used with sealed bearings that can lead to accelerated oxidation of the grease