Users can avoid potential pitfalls with this software.
Engineered Software
02/15/2018
Editor’s Note: Dominik Fry is a member of Ray Hardee’s team at Engineered Software Inc. This month, he is a guest columnist in Hardee’s place, discussing efficient pumping station design.
The need for water and wastewater capacity is continually growing on a global scale, and with rising energy costs and a greater emphasis on being green, the users and designers of pumping systems in this industry are realizing the need for more efficient designs and practices. It is estimated that water/wastewater facilities account for 35 percent of typical municipal energy budgets.1
With pumping systems responsible for much of this power consumption, design optimization can result in significant energy savings.
In fact, a considerable number of users, suppliers and designers in all industries, as well as government agencies and industry consortia, are developing and implementing strategies to improve the energy efficiency of industrial equipment. In most cases, the potential savings are significant. With a 10 percent increase in the energy efficiency of U.S. drinking water and wastewater systems, the nation would collectively save approximately $400 million and 5 billion kilowatt hours (kWh) annually.1
According to the Environmental Protection Agency (EPA), “incorporating energy efficiency practices into their water and wastewater plants, municipalities and utilities can save 15 to 30 percent, saving thousands of dollars with payback periods of only a few months to a few years.”2
With the number of pumping stations found throughout water distribution and wastewater collection systems, there are many opportunities for improving energy efficiency. However, with the seemingly endless variety of design options, finding the optimal solution can be daunting. Fortunately, fluid piping software provides the necessary analysis to design an efficient pumping system or evaluate current installations for improvements.
Though fluid piping software has been in existence for more than 35 years, it has only recently received considerable attention. The software allows engineers to conduct the type of rigorous design evaluations that they have not previously been able perform.
In the past, engineers often relied on standard designs for new pumping system installations. For example, typical design practice for lift stations involved specifying a duplex pumping arrangement in which each pump is sized for peak capacity. The units alternate operation to ensure even wear and the duplex configuration allows one pump to be taken offline for maintenance. This basic design has not changed much in the past 50 years, and for good reason—it works and provides redundancy to avoid major failures.3
Clearly, the inherent design is sound, but software allows the user to look at ways of improving the system, which may lead to greater energy efficiency and lower maintenance and operating costs.
For example, consider a case in which an existing lift station could be evaluated to optimize the design for improved energy efficiency. The current system includes a wet well lift station with two 40 horsepower (hp) submersible pumps pumping into a 5,000 foot, 8-inch force main. There is an elevation gain of about 55 feet from the discharge of the submersibles to the inlet of the gravity sewer.
Image 1 shows a schematic of the lift station model. The daily capacity of the system is approximately 320,000 gallons and the pumps are sized for a peak design flow rate of 800 gallons per minute (gpm) at 101 feet of head.

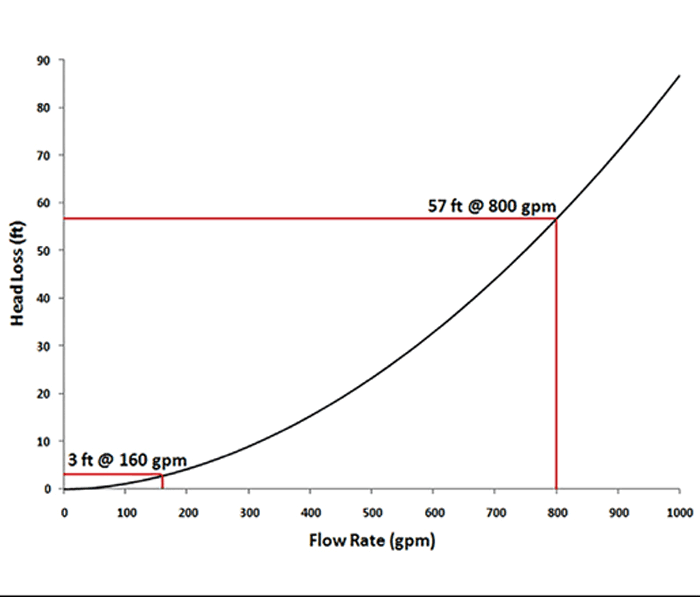
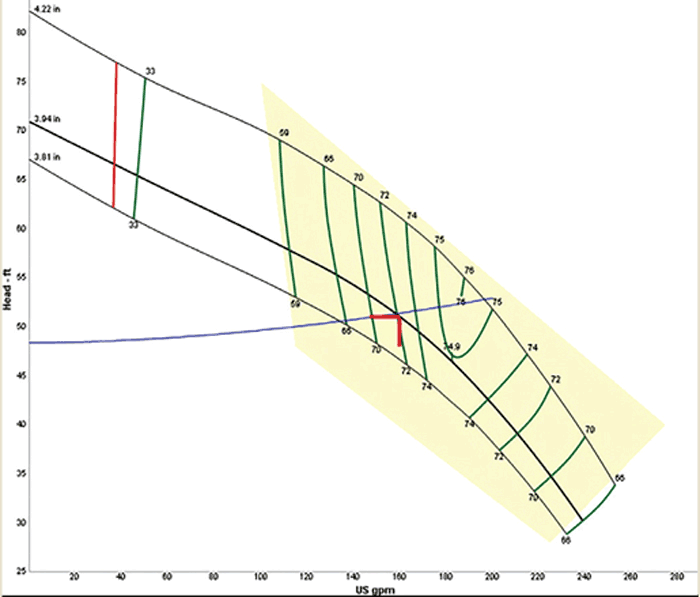

To read more Pump System Improvement columns, click here.