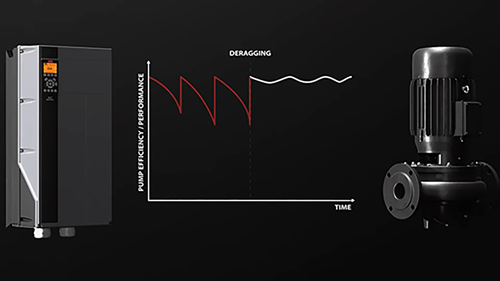
The impact of variable frequency drives (VFDs) on pumping applications is moving beyond the process efficiency associated with varying motor speed. New technologies are helping to reduce the cost of ownership throughout a product’s life cycle, both at implementation and while operating. Often, new VFDs are packed with ancillary capabilities and edge computing that allow for connectivity and replace many different types of controls and relays that were commonplace years ago. Further, their ability to monitor motor signatures and incoming power and integrate additional sensors has improved their capability to protect systems, motors and themselves.
A Sound Investment
When investing in VFDs, users can no longer just look at the initial cost of the unit. The mindset should shift to consider the total cost of ownership (TCO) of the system in which a VFD is integrated (from purchase to end of life/replacement). These units are packed with intelligence that can often eliminate the need for additional controls and generate new value through system monitoring tools.
Investing in a VFD, which costs 5% to 10% more than another version but has features and technology which can reduce or predict problems, may end up paying for itself when comparing it to an incumbent. These savings could be realized in reduced downtime, reduced scheduled maintenance or even reduced trips to sites by providing data that enables service teams to arrive with the correct tools and parts to address the issue at hand.
Proactive Motor Monitoring
Traditionally, people have viewed the relationship between VFDs and motors as unidirectional, with current and voltage monitoring focused more on what energy is going to the motor. Growing advancements allow the VFD to monitor the motor feedback to help with better performance and, more recently, the motor signature. This bidirectional approach enables the VFD to see what information is coming from the motor via the pulse width modulation (PWM) to enable it to predict small failures which previously would have gone unnoticed.
Identifying a small winding problem before it turns into a complete failure allows owners to plan for a scheduled shutdown to replace or repair the motor. Another example looks at the load profile of the application. With growing onboard intelligence, a motor’s load can be monitored, and a user can set limits to help identify when possible mechanical issues like bearing failure, pipe bursts or possible clogs occur. This data can be fed back to operators who can more efficiently respond to problems as they develop.
VFDs can also adapt to and learn about site conditions. This can include learning periods where motor data is collected in the VFD and a normal operational baseline is established. This helps to develop a window of normal operating conditions that if exceeded can alert owners to potential problems before they turn into system failures. The data is unique to the site conditions, stored locally in the VFD, and reflects the operating profile of the equipment. It can be easily tailored to meet the needs of an individual system.
Ancillary benefits of monitoring the load on a pump can enable operators to better detect if pumps are dry through no load or low load operation or if there are mechanical or electrical system issues developing.
Integration With the System
Onboard digital inputs and outputs (I/O), combined with new digital functions, are enabling VFDs to integrate more equipment and interact with more aspects of the system. Additional proportional integral derivative’s (PID’s) and extra I/O can allow operators to use a VFD for damper control or level control, processes which are outside of the motor control. These additional I/O also allow for it to perform more system-related analysis. With the right inputs and programming, VFDs can help monitor a pump’s capacity, alerting users if loads are reaching maximum system limits due to high demand or even a leak. Sensors can be used to enable functions like automatically slow-filling pipes with water before full-speed operation to prevent water hammer or to reduce stress on piping during a system start.
Alongside traditional sensors such as pressure, flow or temperature, VFDs are also integrating sensors that can monitor equipment vibration. This data can be used to monitor bearing wear or imbalances on propellers by looking for abnormal mechanical movements. Once this data is in the VFD, it can be transmitted to the programmable logic computer (PLC) or other control system via fieldbus. No separate communication point or controller is needed, which can help increase the efficiency of integration into a building’s automation system.
VFDs are coming equipped with drive-to-drive communication to help with cascading pumps, balancing runtimes and even multiple lead pumps with redundant control. This can be as simple as connecting two drives’ communication ports together and adjusting a few parameters to have them work in tandem, reducing the need for external controllers and programming to stage pumps to meet demand.
It can also help to balance run times on multiple motors in the system and allow for an operator to take a unit offline for maintenance, while the remaining pumps automatically adapt to the reduced number of pumps which are available.
VFDs have increasing numbers of internal sensors, enabling the VFD to provide feedback to operators on its health and life expectancy. By monitoring internal temperature, a unit can alert maintenance staff to a potential airflow issue, allowing an operator to schedule downtime to clean air channels of dirt or debris. With the onboard sensors, the VFD can better identify problems and help with troubleshooting. Many units even include troubleshooting data and parameter explanations built into the operator interface. Based on runtime, VFDs can trigger automatic alerts for maintenance of itself or other components, such as bearings, and even send reminders to change serviceable parts. For example, VFDs can log runtime of motors and pumps and alert maintenance teams when lubrication or inspection intervals are due.
Growing technology is enabling owners of VFDs to reduce operating costs by allowing systems to run at variable speed to meet demand. VFDs are also increasingly generating new system installation and operational efficiencies throughout the life cycle of a product.
By using increasing onboard digital tools as well as internal and external sensors, they can help with system performance, reduce installation costs and provide valuable data to operators, especially when installed remotely. Their technology often reduces the need for external controllers. Many are even including some basic PLC functions. These new capabilities challenge how users view the upfront cost of a VFD. The benefits post sale and a VFDs impact on a system’s design are generating new value and new ways to view potential return on investment.