Submersible shredder pump offers a solution to problems caused by ‘flushable’ wipes and other fibrous material in Alabama facility.
BJM Pumps, Morrow Water Technologies Inc, Municipal Consultants Inc
03/03/2017
Clogs, especially those caused by wipes, can be a major headache for wastewater treatment plants. One city in Minnesota has even filed a lawsuit against makers of “flushable” wipes. Excessive clogging issues at a wastewater treatment plant in Alabama sent the facility’s team on the hunt for a solution to this pressing maintenance issue.
.jpg)
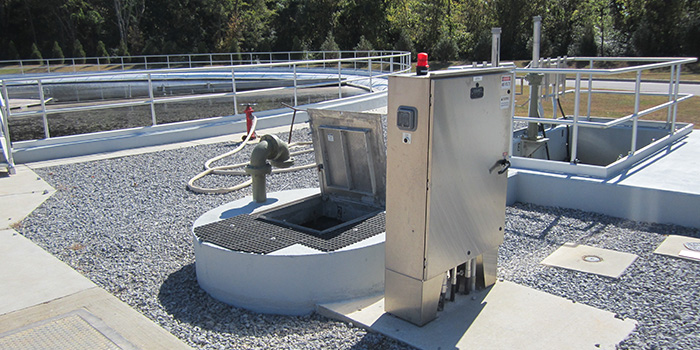
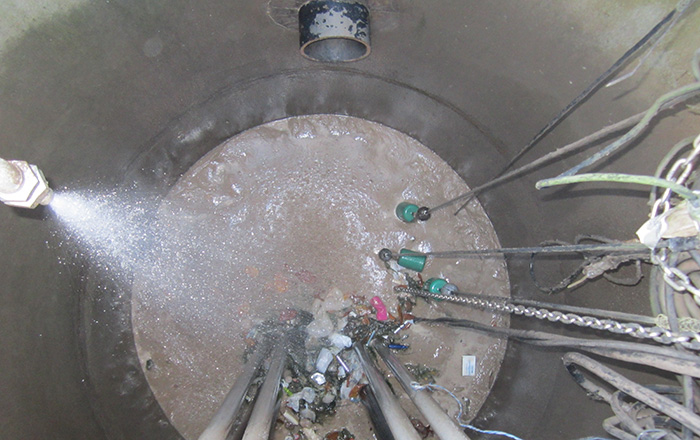
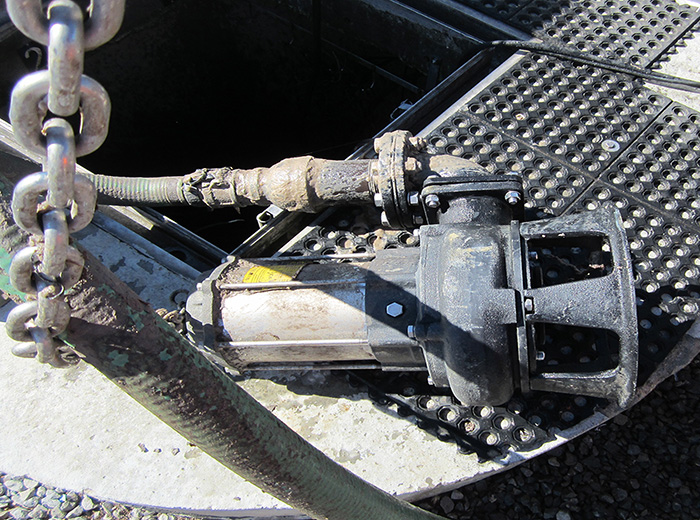