Chemical metering is the act of adding chemicals to another process at a repeatable and consistent rate. The consistent and repeatable aspect of the process is what distinguishes it from any other type of fluid transfer. There are hundreds of applications requiring the transfer of liquid from point A to B. But none require the consistency and accuracy at the level chemical metering does. Too much of a chemical being metered into a waterline could cause it to be more acidic or basic than is safe. Also, too much of a chemical being metered can alter the result of a liquid application that is intended to create a new substance, and vice versa—under metering of a chemical can be just as detrimental to the process at hand. One type of pump used for chemical metering is a diaphragm-type metering pump. This article will review five chemical metering applications, what they are, where they are seen, as well as why chemical metering pumps are the most appropriate for this application and how they work.
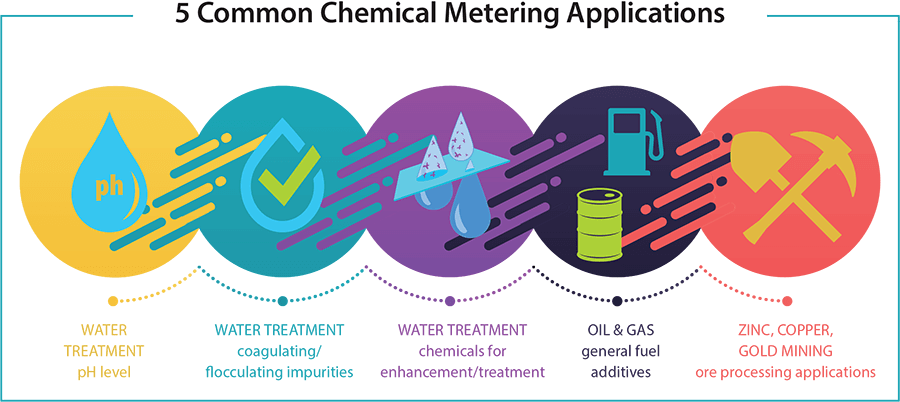
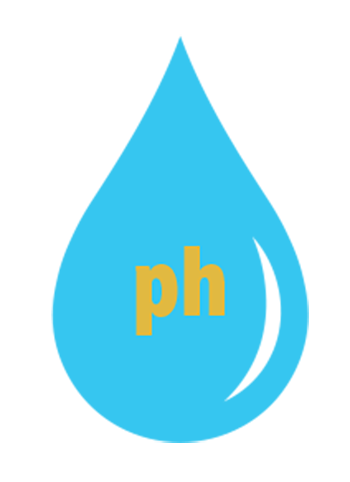
Water Treatment—pH Level
When it comes to wastewater treatment applications, whether it be municipal water or industrial plants treating their own water, pH balancing is a mainstay. If water remained very acidic, or very alkaline, processing equipment would suffer. High or low pH levels can damage equipment, corrode piping and, at certain levels, is dangerous. Often, chemical metering pumps are metering sulfuric acid or caustic soda to help balance pH levels. Sulfuric acid helps reduce high alkalinity, and caustic helps neutralize acidic water. There are many other chemicals that can be used to balance pH, but these are two of the most common. Sulfuric acid and caustic soda are corrosive chemicals and can be hard for some materials to handle. Diaphragm metering pumps are suited for this, offering a wide range of wetted end material setups.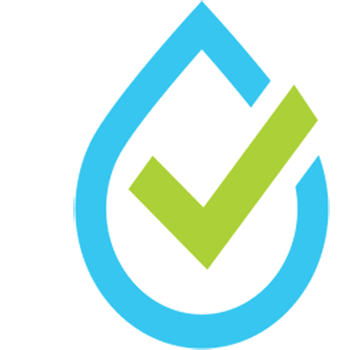
Water Treatment—Coagulating/Flocculating
Wastewater, or water in general, can be contaminated with small particles and other impurities. The act of coagulating, or flocculating, in general is the process of metering a chemical into the water, which helps these impurities and particles cling together and settle within the water, making it much easier to remove them. Polymers would be a common flocculent used in most wastewater treatment plants. Polymers can be more viscous than other water treatment chemicals, yet diaphragm metering pumps can be tailored to handle this well.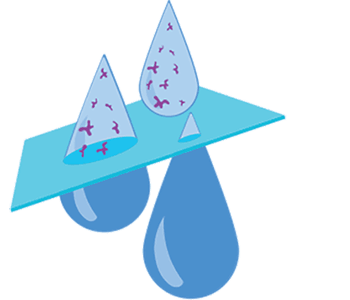
Water Treatment—Enhancement or General Treatment
This last section is more or less “all encompassing” for the remaining reasons you would use chemical metering for water. From adding fertilizers to an agricultural sprinkler system; adding corrosion inhibitors to boiler water to prolong piping and heating tube service life; to adding chlorine to kill germs in the water; and everything in between, chemical metering arises in nearly all water processes.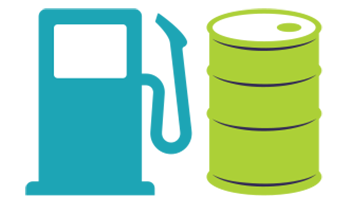
Oil & Gas—Fuel Additives
Fuel additives in the oil and gas industry cover a broad range of specific applications within this general category. Metering pumps are used throughout these plants, including water treatment.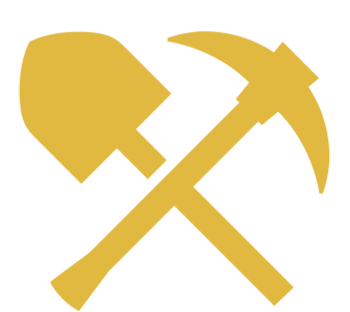
Zinc, Copper, Gold Mining—Ore Processing Applications
In general, these mining applications remove these precious metals from the ore (rock), and chemicals play a large role in this. Much like the oil and gas applications, this is a broad topic with many chemical metering processes within it—one also being water treatment. No matter the application, whether common or unique, chemical metering is a pertinent process. Below explains why diaphragm-type chemical metering pumps are suited for chemical metering applications.Diaphragm-Type Chemical Metering Pumps
There are many reasons diaphragm-type metering pumps are one of the most common pump designs for injecting chemicals at a consistent rate, but the two most important reasons are their wetted end material flexibility and the actuating process of the diaphragm and inlet/outlet valves. Wetted end material flexibility—This is as simple as it sounds. Diaphragm-type metering pumps offer a wide range of materials to allow for a durable wetted end no matter the chemical being metered. The wetted end is a term used to describe the pumping head on the chemical metering pump. It includes the diaphragm, the pump head and thevalve assembly. Because these are separate components, manufacturing processes can easily make each piece in multiple materials. For example, the following options are available for the wetted end (generic names for the materials are listed; brand names are often used within the industry):- Solution head materials: polyvinyl chloride (PVC), polypropylene, polytetrafluoroethene (PTFE) and 316 stainless steel
- Diaphragms: polychloroprene or pc-rubber (Neoprene), chlorosulfonated polyethylene (CSPE) synthetic rubber, synthetic rubber and fluoropolymer elastomer (FKM) and PTFE-faced
- Valve seats and balls: polychloroprene or pc-rubber, CSPE synthetic rubber, FKM, PTFE and 316 stainless steel. The valve balls are also available in ceramic and Hastelloy C (nickel-molybdenum-chromium superalloy with tungsten).