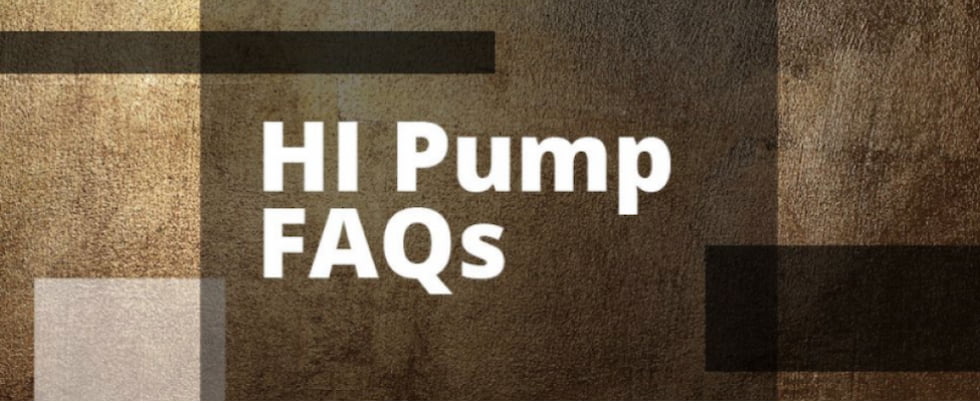
What are common problems that cause excess pump system vibration?
Pump vibration is related to the pump’s rotational and hydraulic forces, and the dynamics of the pump’s rotor and structure. Typical forced vibration from the pump are related to the speed of rotation in rotations per minute (rpm) and multiples of rpm, such as:
- 1 x rpm
- 2 x rpm
- number impeller vanes (N) x rpm

Some causes for these forced vibrations are misalignment of the pump and driver shaft, imbalance, bent shafts and damaged impeller vanes. Vibration sources can come from system-related issues, such as cocked or damaged bearings, and inadequate piping supports and other sources of excessive nozzle loading.
Vibration can increase in severity when improper installation and foundation exists, such as improper grouting, inadequate tie-down bolts, inadequate baseplate material, inadequate baseplate rigidity and the lack
of proper internal locking of the baseplate to the foundation.
Another consideration is that resonance can occur. Resonance is a condition where the forced vibration frequency aligns with a structural or rotor natural frequency resulting in amplified vibration. Even low forced vibration can result in an amplified vibration that is unacceptable.
When resonance results in undesirable vibration, the frequency of the forced vibration will need to be changed or avoided, or the natural frequency of the system will need to be modified.
For more information, refer to HI’s Pump System Optimization Guidebook, ANSI/HI 9.6.8 Rotodynamic Pumps – Guideline for Dynamics of Pumping Machinery, and ANSI/HI 9.6.4 Rotodynamic Pumps for Vibration Measurements and Allowable Values, at pumps.org.