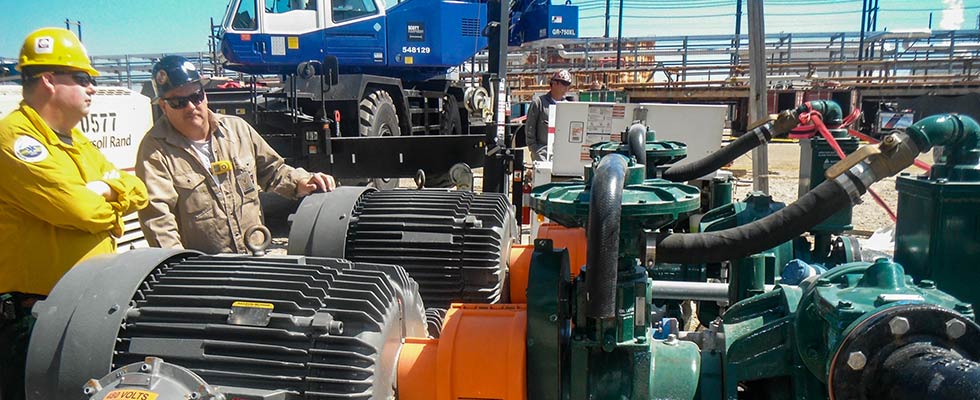
When a new oil and gas plant is built or remodeled, new pumping systems for industrial process water and waste are inevitable. This was the case at one company in Port Arthur, Texas, and St. Charles, Louisiana. The requirement was two identical above-grade, skid-mounted systems that need to deliver 540 gallons per minute (gpm) against 80 feet of total dynamic head (TDH) in existing force mains.
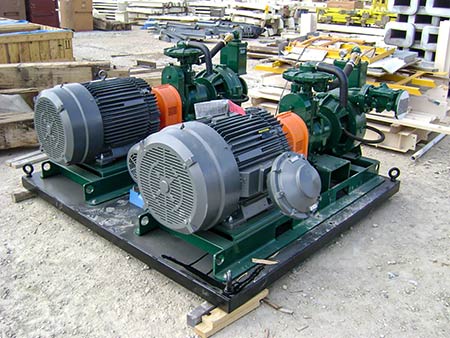
Working with an engineering firm, one pump station design and supplier prefabricated, delivered and commissioned both systems.
Pumping into a high-pressure existing force main required an above-grade, self-priming end suction centrifugal pump for several reasons. First, there are more motor/pump combinations to select from for a given duty point. Additionally, how the pump is coupled to the motor will dictate the speed at which the impeller rotates. High impeller speeds (to a point) help to overcome large duty points (gpm at TDH). An above-grade pumping skid is also ideal for pumping into a high-pressure existing force main because it keeps the pumps out of the process fluid and allows for easy maintenance as all aspects of the pump are accessible.
On any construction site, the time it takes to construct is critical, and on a construction site such as a refinery in Port Arthur, there is no room for errors. That is why it was necessary to handle the complete design and supply of the system that will be integrated into the site to ensure the project’s overall success.
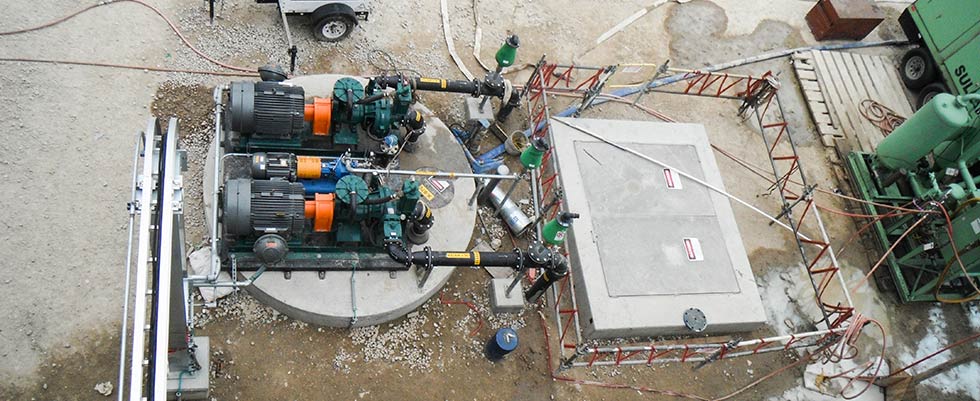
The design criteria must be considered, along with the larger system, before designing the best pumping system to meet the application. These criteria must be considered instead of just providing a model that is expected to fit into the application of the facility. This is also in addition to using the staff’s preferred equipment, since they will be owning and maintaining the pumping system.
After the design is complete, the sump (wet well) is prefabricated along with the pumping skid, the valve vault and the controls. This allows for an easy installation on-site. This is critical at an oil and gas facility as space can be limited and precise construction is needed. All aspects of the system also need to be easily maintained to ensure the facility can maintain production.
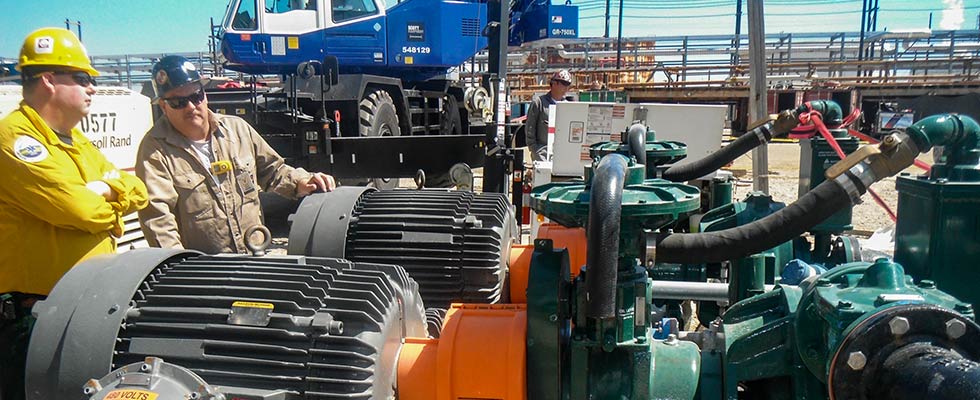
To ensure the installation and startup are handled correctly, pump station design and supply personnel are sent to the construction site. A refined commissioning process is followed, working through all aspects of the system (controls, structural/mechanical, electrical, etc.) while adhering to safety policies at the facility. Before leaving, the responsible personnel is trained to guarantee the long-term success of the system.
Oil and gas facilities are complex and involve incorporating the use of many equipment types and manufacturers. For these locations to operate seamlessly, everything needs to be integrated and designed to the standards of the end user.
In addition to being functional, these facilities need to be safe and easily operated and maintained. To accomplish this, it is important that the user knows exactly what is needed and that they have a good understanding of how the equipment operates.
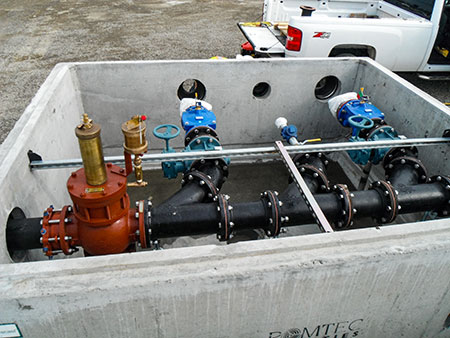
While there may not be many design preferences in structural and mechanical terms, the end user interfaces primarily with the system’s control panel, which is where it is important to design according to the user’s standards. In the case of the refinery project in Port Arthur, a complete control panel centered around a programmable controller, ultrasonic transducer primary level sensor and an automatic dialer. All components were approved by the user to meet the operators’ needs.
Pump station controllers are selected by the user’s standards and requirements, which in this case was an ultrasonic transducer to be used for the primary level sensor. Ultrasonic transducers are common within industrial applications and provide many advantages versus other forms of level sensing such as floats and pressure transducers. One of the primary advantages of an ultrasonic transducer is that it is a noncontact level sensing device. In other words, the transducer does not come into direct contact with the media that is being pumped. In an environment where fluids with extreme pH and temperatures are being pumped, this can prove to be useful in the life span of the unit.
In any environment, compliance with and integration into an existing supervisory control and data acquisition (SCADA) is a must. Oil and gas plants typically have existing and well-oiled control and communication standards that must be adhered to. Building consistency in an industrial facility is key to developing a safe and efficient working environment.
Regarding SCADA/telemetry in the case study, the owner of the facility chose to incorporate the use of an automatic dialer to call out specified alarms. Automatic dialers are an accepted form of telemetry that provide the ability to both report and often acknowledge alarms remotely. In an oil and gas facility, maintenance personnel may not be able to respond immediately to an alarm; so, having the ability to be notified of a specific issue will help drive the sense of urgency of their response.
An oil and gas application requires precision and flexibility—in terms of components and mechanical and structural design, as well as precision in terms of engineering and installation. It is important to understand the application and the existing systems in place to then design, supply, install and start up the correct system type with the correct components, all while taking the owner’s preferences into consideration. The right components can be the difference between a system’s success and failure.