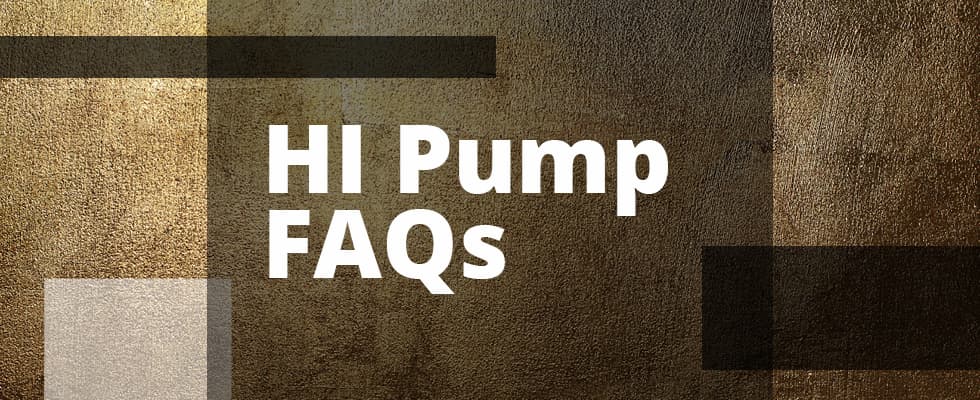
What drives are used in sealless pumps?
In a sealless pump design, the inner rotor assembly is directly driven by either a canned motor or by a synchronous or an asynchronous magnetic drive. A portion of the pumped liquid is required in the drive section for lubrication and cooling.
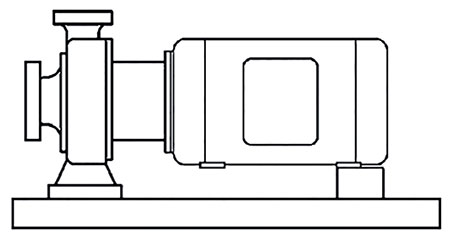
The design does not use a dynamic shaft seal as a primary containment device. Static seals are used to isolate the process liquid from the external environment. Since these pumps are designed without a mechanical seal, the chance of the process fluid being released to atmosphere is lessened. Secondary control or containment can be part of the design, which further lessens the chance of the pumped liquid releasing to atmosphere if the primary containment is breached.
However, to eliminate the mechanical seal, the method for transmitting power to the pump shaft is different than a mechanically sealed pump. It is achieved with a canned motor or magnetic drive that transmits torque through a primary containment shell.
The canned motor type has a common shaft to link the pump and motor (close-coupled) in a single sealed unit. The pumped liquid is circulated through the motor but is isolated from the stator by a corrosion-resistant stator liner and is isolated from the rotor by a corrosion-resistant rotor liner.
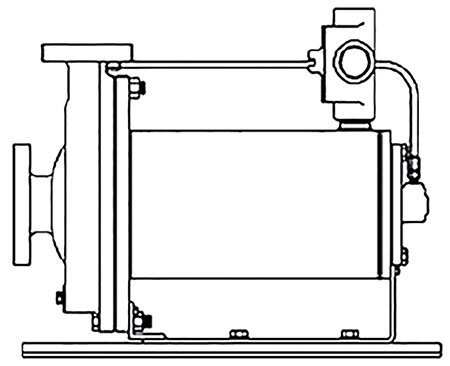
The magnetic drive type uses an outer ring of permanent magnets to drive an internal rotating assembly through a corrosion-resistant containment shell. This allows magnetic drive pumps to be driven by a standard motor or drive shaft coupled to the magnetic drive. There are two types of magnetic pump couplings: synchronous and eddy current.
Synchronous magnetic couplings contain permanent magnets inside and outside of the containment shell that rotate the pump shaft in synchronized motion with the driver shaft. These couplings do not slip—the pump shaft turns at the same speed as the outer magnet assembly.
Eddy current magnetic couplings consist of a permanent outer magnet ring and an inner torque ring containing a network of copper rods supported on a mild steel core. The rotating magnet ring generates eddy currents in the copper rods, which convert the core to an electromagnet. The difference between the two shaft speeds is defined as magnetic slip.
Synchronous magnetic drive sealless pumps use either ceramic, ferrite, or rare earth magnets, such as neodymium iron boron or samarium cobalt. The outer steel portion of the outer magnet assembly should be coated with a corrosion/heat-resistant paint or coating.
For more information about sealless pump drives and vibration analysis, refer to ANSI/HI 4.1-4.6 and ANSI/HI 5.1-5.6, which cover nomenclature, definitions, application, operation, and tests for sealless rotary and rotodynamic pumps.