The term wire-to-water efficiency has been used in the pumping industry for years, but what does it really mean? Simply put, it is a way to determine how efficiently an electromechanical system uses electricity to perform work, such as pumping. In hydraulic terms, it is the ratio of water horsepower (hp) output to true horsepower, or kilowatt, input to the motor. Wire-to-water efficiency considers the efficiency of the pump, motor and variable frequency drive (VFD), if applicable, at a series of operating points that simulate historical conditions, so a baseline efficiency, or energy intensity in kilowatt-hour per million gallons (kWh/mg), can be established. The kWh/mg can then be compared to the other pumps in the system to determine which have the highest potential for energy savings and optimization. Not only do users want feedback about inefficient pumps, they also want to know what may be causing the inefficiency, even if it is a high-level overview of items that should be addressed. These suggestions are called energy efficiency measures (EEMs). See Image 1 for a depiction of inefficient pumping causes and symptoms and potential EEMs.
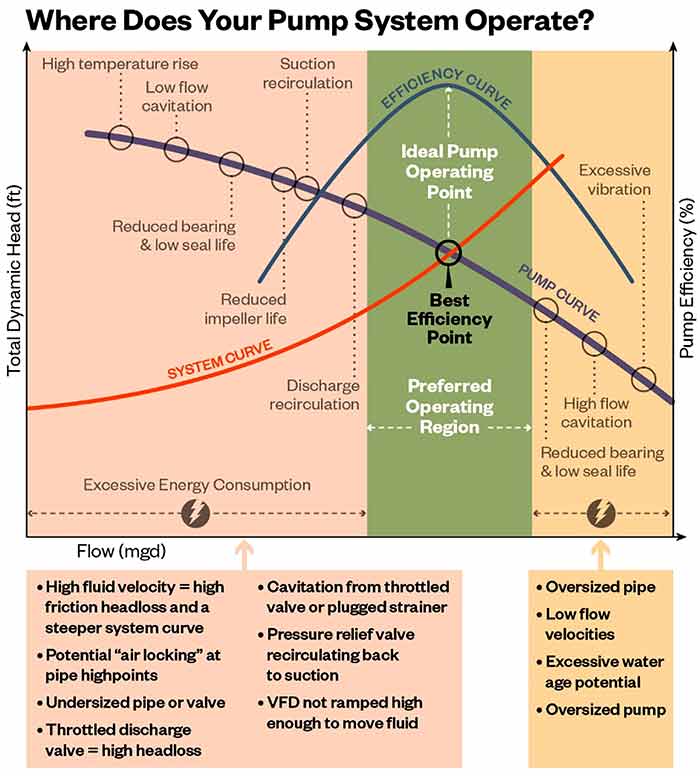
Wire-to-Water Testing: The How & Why
First, identify which pumps to test. Users often ask, “How do I know which pumps to invest in for wire-to-water testing?” It is recommended that a high level energy intensity evaluation be performed prior to the field testing, so a shortlist can be ranked from highest kWh/mg to lowest. This evaluation involves taking the monthly consumed kWh (from the electric bill) and dividing by the total flow in million gallons pumped during the same billing cycle. If there is no flow metering at the pump station, a properly specified portable flow meter should be installed on the pump(s) so totalized flow data can be correlated to power consumption. Often the pump(s) being tested are served by the same billing meter as other electrical loads (for example, water and wastewater process equipment at treatment plants). In these situations, submetering is not typically available to trend the power consumption, so installing temporary power quality monitors (PQMs) on pump motor control centers (MCCs) is a good idea. Pumps that have a history of excessive maintenance, significant historical runtime, and/ or are greater than 40 hp tend to be good candidates for submetering with the PQMs so the kWh can be trended. More rudimentary techniques can help determine a rough estimate of percent contribution of power consumption for those situations that do not have submetering. One technique is developing a nameplate motor hp ratio of the pump(s) being analyzed compared to the total connected hp at the facility; but, a historical runtime is still required. Once the shortlisted pump systems are identified, a scoping visit typically follows. During the scoping visit, a feasibility evaluation of the wire-to-water testing opportunity should be performed. This evaluation should:- inventory what existing instrumentation is available for accurate readings and what is needed to acquire total dynamic head (TDH), flow, pump speed, line-to- line voltage, phase amperage and phase power factor
- determine if essential data is available to help discover historical runtime, energy usage and costs
- determine the availability of mechanical as-builts to support hydraulic evaluation and EEM development
- provide the pump tester with the operational knowledge of the pump system so a safe and accurate field test can be performed to show the historical operating conditions
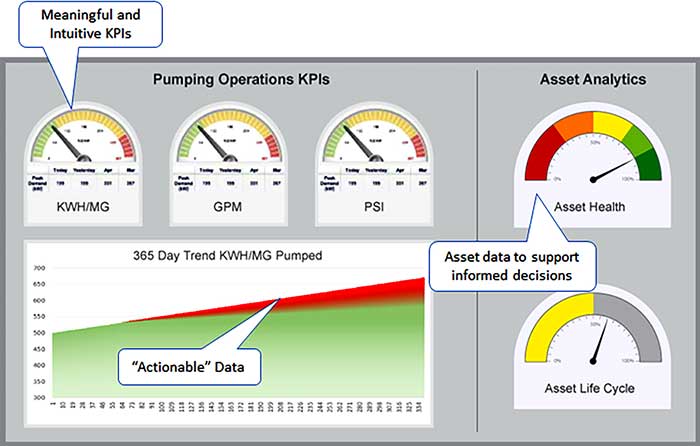
Things to Consider
Follow these wire-to-water testing tips for success.- Determine the boundary conditions for the test with respect to where Bernoulli’s Equation will be applied to determine the site system curve.
- Record the operating condition of the pump being tested prior to de-energizing the pump to install the PQM, so the same operating condition can be measured when the pump is re-energized for testing.
- Observe if other pumps are pumping into a common discharge manifold with the pump being tested or if there is flow going to other demands not being recorded by the flow meter for the test, such as plant water. Not accounting for all the flow will skew test results.
- Follow proper arc flash and safety precautions when installing, using and removing the portable PQM.
- Allow pump operating conditions to stabilize before recording data.
- If a pump driven by a VFD is being tested, the PQM should be installed on the line side of VFD to record the “true” power consumed. Never install the PQM leads on the load side of the VFD since this will not account for variations in VFD efficiency at different speeds.
- Verify that hydraulic instrumentation is calibrated, installed per manufacturer standards and operable.
- If possible, record worst and best case static head when the flow is 0 gpm. If not, establish static head from as-builts.
- Collect previously measured hydraulic and electric data at various speeds if the pump is on a VFD.
- Verifying pump curve performance at various throttled valve positions, while keeping pump speed constant, is a good practice when performing wire-to-water tests.
- Collect hydraulic and electric field data simultaneously.
- Collect at least three separate data points at each speed ensure ample data for a regression analysis.
- Run wire-to-water, power calculation and system curve polynomial regression analyses to ensure data accuracy to as indicated by an R2 value greater than 0.9. If the R2 value is less than 0.9, consider repeating the test. If the tests continuously result in R2 values less than 0.9, it is likely due to inaccurate flow, pressure, level or power measurement. It is important to also recommend a visual inspection of the data against the regression analysis to confirm a good fit.
- If performing wire-to-water tests for a pump station with multiple pumps operating at the same time with only one flow meter on the manifold, it is inaccurate to assume the flow for the pump being tested is the total flow from the pump station meter divided by three, due to varying hydraulic losses, pump wear, etc.
- Using pump pressure differential and a shop test pump curve to estimate flow will introduce uncertainties in the analysis and should not be practiced.
- If the pump tester notices an obvious mechanical or electrical issue with the pump being tested prior to performing the tests, do not attempt to fix the problem as this will void the test. Wait to implement the fix, or EEM, until after collecting data so the testing can simulate typical operating conditions. Feel free to collect wire-to-water test data after implementing the EEM. You will likely see a reduction in kW if the fix worked.
- Listen to the operator. He or she likely knows the system best. Only operate at flows and pressures the operator is comfortable with so as not to cause harm to the system.