What is a Safe NPSH Margin for a Centrifugal Pump?
The Hydraulic Institute NPSHA Margin Work Group (1) recommended NPSH margins ranging from zero to four times the NPSHR (NPSHA÷NPSHR = 1 to 5). The higher values apply to pumps with high to very high values of suction energy, a term defined as the product of the diameter of the pump suction nozzle, pump RPM and the suction specific speed.
McGuire (2) has provided a similar set of recommendations, seen in Figure 1, based on the service, pump size and peripheral velocity of the impeller eye.

Figure 1. Recommended centrifugal pump NPSH margins (J.T. McGuire [2])
Sloteman, et.al., (7) reported field experience with a four‑stage, barrel type, boiler‑feed pump, rated at 33,500 hp, 11,000 gpm and 5,800 rpm. The 3 percent NPSHR was 250 ft. The power plant, with a booster pump, provided 500 ft, twice that "required" by the pump. Impellers were made of CA6NM stainless steel. Because of cavitation damage, the first‑stage impeller experienced a life of about 12 months. Although a 100 percent NPSH margin was provided, the cavitation damage rate was unacceptable.
Can You Provide Too Much NPSH?
Well, it does seem so.
As we have just proven, conventional wisdom is to provide some margin of NPSHA over NPSHR. Unfortunately, the facts indicate that if the pump is operating near the 3 percent head‑drop NPSHA, an increase in NPSHA will result in a noisier pump with a higher rate of damage.
Grist (3) reported that maximum cavitation‑erosion rate corresponded with maximum cavitation noise. Based on the information available, he postulated that this occurs when the NPSHA is about two times the "3 percent" NPSHA. Figure 2 is a reproduction of Figure 2 from Grist's paper (3). Note that this ratio of "two" occurs only at (or near) the BEP. At both lower and higher capacities, the ratio increases. The ratio of two should be taken as typical, for the literature indicates lower ratios for pumps with low suction specific speeds and higher ratios for pumps with high suction specific speeds.
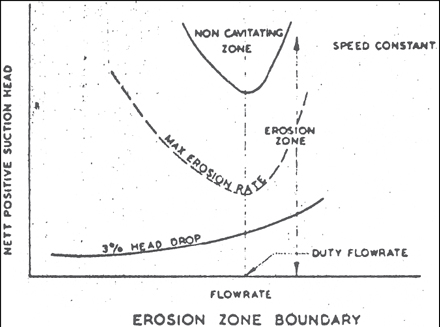
Figure 2. From Grist's "Nett Positive Suction Head Requirements for Avoidance of Unacceptable Cavitation Erosion in Centrifugal Pumps" (3)
Vlaming (4) came to similar conclusions, publishing the graph seen in Figure 3. The major difference is that Vlaming, while acknowledging a reduction in cavitation noise at lower values of NPSHA, did not acknowledge a reduction in cavitation damage at the lower values of NPSHA.
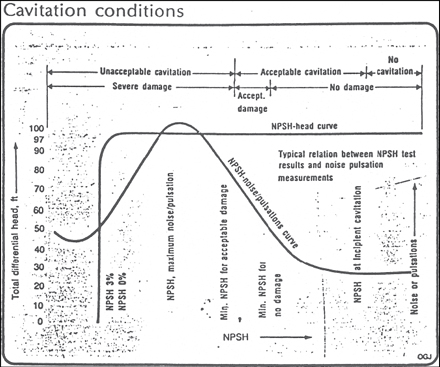
Figure 3. Pump Head & Noise as a Function of NPSHA (D.J. Vlaming [4])
Igor Karassik (5) enjoyed telling the story of his experience with condenser hot well condensate pumps, with the performance seen in Figure 4. These pumps were typically installed in systems that allowed the water level in the hot well to control pump capacity. Water in the hot well, at its bubble point, would readily flash (cavitate) in the impeller eye. A lower water level would result in lower NPSHA, which would result in a lower pump head (more flashing) and lower pump capacity. Pumps operating along a vertical segment of their head curve(s) are said to be operating in the break. Pumps made of standard iron/bronze construction had acceptable component life in this service.
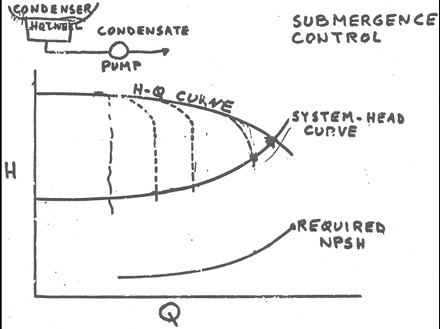
Figure 4. Pump Capacity Controlled by NPSHA (I.J. Karassik [5])
When these systems were changed to control pump capacity by throttling the pump discharge, cavitation damaged the pumps at a higher rate of erosion. The higher NPSHA caused the rate of cavitation erosion to increase.
McGuire (2; Figure 6.6) confirms that cavitation erosion occurs at a value of NPSHA above the 3 percent head‑drop value.
How can a greater amount of cavitation create less noise and erode the metal at a lower rate? A number of theories exist. Some authorities speculate that the greater amount of gas creates a cushion for the collapsing bubbles. Others speculate that the larger bubbles, associated with the greater cavitation, collapse with less intensity. This author speculates that the larger bubbles are swept from the metal surface and collapse in the fluid stream, away from the metal. Nobody really knows.
As I think back on the field problems I have seen, I recall a few that left us scratching our heads. There were cases of pairs of apparently identical pumps, where one "cavitated" louder than the other, and the bad actor was the one that appeared to have more NPSHA than the quieter pump. Could it be that the noisier pump was noisier because it had more NPSHA?
Would it be heresy to suggest that it might be advantageous, under the right conditions*, to reduce the NPSHA to a "cavitating" pump? Based on the facts, this seems to be a reasonable approach.
So what is a safe margin for a centrifugal pump? Figure 2 shows that the NPSHA must be pushed well above the value for maximum erosion rate, and this can be in the range of five to ten times the NPSHR3, normally a value that is not obtainable. It therefore appears best to keep NPSHA near or slightly above (5 to 10 percent above) NPSHR3.
*The right conditions would include current operation with NPSHA in excess of the 3 percent head‑drop NPSHA and being able to avoid vortexing in the suction vessel, to control the NPSHA and to accept a slight drop (up to 3 percent) in pump head.
References
1. "Cavitation Problems?", Hydraulic Institute NPSHA Margin Work Group, Plant Services, August 1997.
2. McGuire, J. T., "So You Need Pumps for a Revamp!", Pumps & Systems Magazine, August 1996.
3. Grist, Edward, B.Sc., "Nett Positive Suction Head Requirements for Avoidance of Unacceptable Cavitation Erosion in Centrifugal Pumps", Paper No. C163/74, 1974.
4. Vlaming, D. J., "Analysis of Cavitation Provides Advanced NPSH Estimates for Centrifugal Pumps", Oil & Gas Journal, November 19, 1984.
5. Karassik, Igor J., Centrifugal Pump Clinic, Marcel Dekker, Inc., New York, NY, 1989.
6. McGuire, J. T., Pumps for Chemical Processing, Marcel Dekker, Inc., New York, NY, 1990.
7. Sloteman, Donald P., Wotring, Timothy L., March, Patrick, McBee, Dan, & Moody, Larry, "Experimental Evaluation of High Energy Pump Improvements Including Effect of Upstream Piping," Proceedings of the 12th International Pump Users Symposium, March 1995.