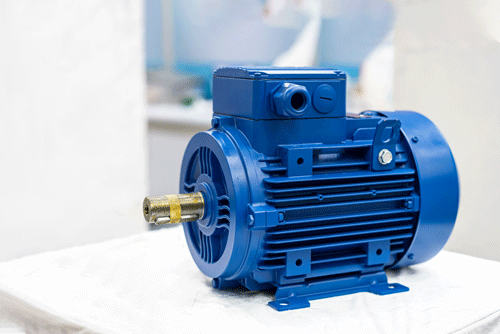
Modern technology is powerful and capable of bringing about fundamental change. So, where is the technology transformation in the world of electric motor driven systems?
Motor driven systems are maintained and operated essentially the same way they were 50 years ago. Granted, there have been improvements during that time. Motors are designed to be more efficient, control systems are more sophisticated and a variety of monitoring and information technologies have become available. However, a broad transformation of this space seems to be missing.
Many electric motor driven systems are still operated until catastrophic failure. Too many motor system operators have little or no information about the health and efficiency of their motor driven systems. Unexpected downtime and costly loss of productivity is still common.
Industrial electric motors are the prime movers of modern societies, consuming 47% of global electrical energy production. The massive economic and environmental impacts of electric motor systems are challenging to quantify and difficult to overestimate.
So, why has technology not fundamentally transformed such an important area? Is it because maintenance and operation of motor systems is already optimized? Has efficiency been maximized and downtime minimized to the limits of modern technology? Numerous studies, such as from the United States Department of Energy, show this is clearly not the case.
A Proposed Answer
How has fundamental change come about? While the full answer to this question is complicated, the enabling mechanisms are clear: (1) ubiquitous data connectivity enables (2) a nearly continuous flow of rich information to and from (3) powerful information systems—think Apple, Google, Amazon, Facebook, etc. Personal, detailed information is constantly provided to these systems, which enables a host of providers to dramatically impact lives. The life blood of this system is constant rich information.
So, what about the world that is driven by electric motor systems? What’s missing? Not data connectivity or powerful information systems, but rich information. Tapping into truly rich sources of constant information about motor driven systems has been unsuccessful thus far. There is an information gap.
First Step Toward Transformation
Transformation of how motor driven systems are maintained and operated is possible. Advanced monitoring and analysis of the power usage patterns of all critical electric motor driven systems is
one component that could be essential to transformation in this space. This source of constant, rich information can go a long way toward filling the missing information gap.
Many users already have an overwhelming amount of data, including values from power-related monitors. This existing large volume of data has generally produced little value.
Reconsider the potential for advanced electric power monitoring. Correctly done, and coupled with advanced information technologies, monitoring the power feed to an electric motor will reveal virtually everything a user wants to know. Users will learn not only about the motor itself, but the mechanical load it drives, the control system that starts and stops it and the surrounding plant infrastructure. Conventional monitoring, such as vibration and temperature sensing, do not contain adequate information, no matter how sophisticated the related data analysis may be.
Diagnostic Information Contained in Power Monitoring
The following is a partial list of actionable information that can be extracted from advanced monitoring of a motor’s electric power feed and has been compiled from actual field demonstrations.
- motor starter, variable frequency drive (VFD) and control system misoperation
- external wiring degradation/failure
- internal motor wiring failures
- motor overloading
- excessive motor starting stress
- misalignment leading to mechanical failure
- motor bearing failure
- belt drive failure prior to full
- system failure
- belt slippage enabling pre-failure adjustment
- pump/fan blockage
- motor single phasing failure
- excessive supply voltage unbalance
- excessive motor current unbalance
- various electric power disturbances, including both internal plant and utility grid issues
- energy savings opportunities
Actual Field Experience
A large percentage of motor driven systems are misoperating in ways that are unknown to the operator, resulting in negative impacts on energy consumption and reliability. These impacts can be readily identified, well before failure, using advanced power monitoring and analysis. Motor starting mechanisms are routinely found to be misoperating, including VFDs.
Misalignments and degradations associated with the driven mechanical systems can be detected surprisingly early, including diagnostic indications of the specific mechanical component requiring attention. Voltage supply problems have been identified, including those caused by both the utility grid and by internal plant problems. A wide range of emerging problems can be detected well before loss occurs through a single monitoring type that can be installed in approximately two hours by plant electricians.
What Type of Power Monitoring Is Required?
Some of the diagnostic information that can be extracted from power monitoring is readily available in traditional power monitors that provide basic trending data. Such data may be accessed via open protocols and will include timestamped values averaged over fixed trend intervals (five minutes, etc.), such as volts, amps, watts and volt-amps reactive. Many
plants already have several monitors of this type, which may already serve as data sources for existing building or asset performance management software systems. With support from IT staff, it should be practical to prepare reports or trigger alerts based on this trending data coupled with recommendations provided in published guidelines or standards such as NEMA MG-1.
Here is the more challenging part: The richest source of diagnostic information is contained within power transitions, such as motor starts and stops. These transitions occur asynchronously, driven by each specific production process, with the information contained in voltage and amperage waveforms sampled at the subcycle level. An intelligent monitor will be able to automatically detect significant changes in motor power usage and will transmit the resulting information for further analysis. Unfortunately, methods for capturing, transmitting and analyzing this type of information are not simple to implement today. Cost-effective technologies should become available for mass use as the transformative value of this type of monitoring and analysis is recognized. Emerging artificial intelligence technologies will amplify the diagnostic potential of advanced power monitoring.