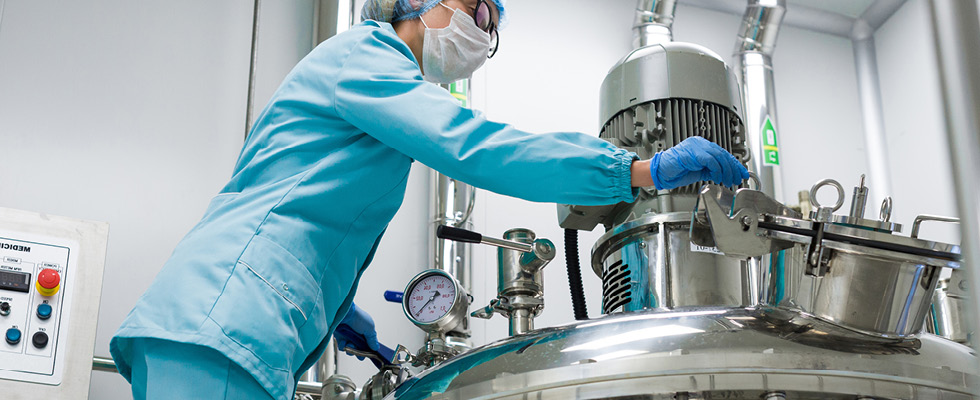
Ongoing labor shortages have hit the food and beverage industry hard, leaving many manufacturers without the skilled workers to effectively maintain operations. However, production demands are accelerating, and maintenance and reporting needs have increased, with many operations getting larger and more complex. Today, successful food and beverage maintenance operations are finding solutions by leveraging industrial Internet of Things (IIoT) technology paired with cloud-based asset management software to extend equipment life span, boost maintenance team efficiency and increase safety.
For decades, condition monitoring has been a key aspect of any predictive maintenance strategy. The approach uses handheld measurement tools and IIoT sensors to continuously monitor asset vibration and temperature, among other early indicators of failure. This was once a manual process that required expert staff. Increasingly, manufacturers are finding solutions to these challenges through “connected reliability,” a framework that lets maintenance teams combine a wide-ranging array of hardware and software in one cloud-based ecosystem.
Today, IIoT sensors can stream asset condition data in real-time to a computerized maintenance management system (CMMS) or enterprise asset management (EAM) system, which can analyze the data and pinpoint new and developing faults. Beyond wireless sensors, some maintenance software providers also offer easy integration to other enterprise systems, like production and facilities software. These systems are often underutilized by maintenance teams and can offer key predictive insights.
By identifying problems before they escalate to failure, food and beverage manufacturers can move to condition-based maintenance and focus their energy on the activities that matter most. This reduces the risk of unplanned downtime and saves the expense of needlessly servicing equipment. Maintenance management can be automatically integrated with data acquisition and analysis, giving businesses real-time visibility to make data-driven decisions.
IIoT condition monitoring sensors paired with CMMS software are already helping a host of companies in the food and beverage industry overcome challenges and successfully scale production. For example, the Jack Daniel Cooperage in Trinity, Alabama, uses vibration sensors to monitor the health of critical assets at their busy plant. Because dust collection is a key part of any woodworking business, the cooperage must ensure their dust collection equipment remains in optimal condition. They also need their woodworking tools to stay in top shape so they can meet the demanding production schedule. This data integrates with their CMMS, so the analysis of incoming vibration and temperature data can be compared against an established baseline, and work orders can be automated when thresholds are exceeded.
As another example, the Valley Queen Cheese company in Millbank, South Dakota, shifted to a condition monitoring strategy when they ramped up operations to meet increased demand. As part of this expansion, Valley Queen added several critical new pieces of equipment, including a blower essential to the process of moving products along to the packing room.
Without properly running equipment, the production line would go offline. That could lead to real consequences, including lost production time and wasted product. To keep production running, the team decided to install vibration sensors on the large blower and other critical assets.
Integrating these condition monitoring sensors with their CMMS lets Valley Queen plan and schedule maintenance as soon as any issue comes up with the monitored assets. As soon as the data shows vibration levels are rising, Valley Queen knows they need to schedule maintenance to prevent an unexpected shutdown.