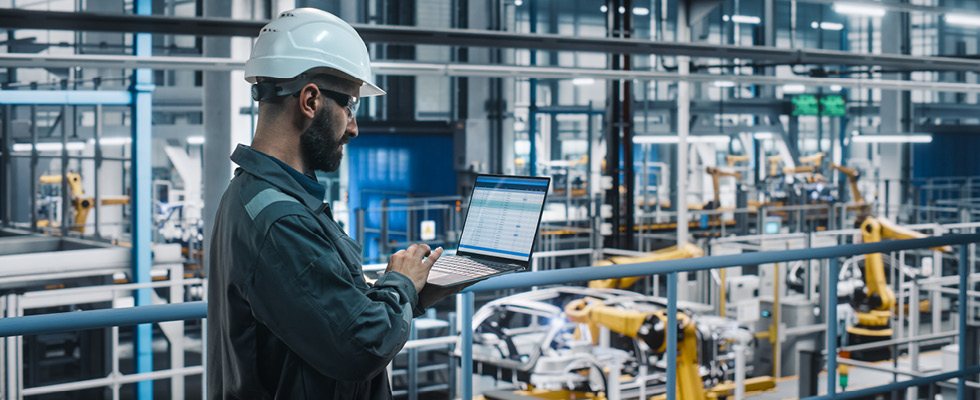
Part 1 ran in the September issue of Pumps & Systems.
1. Seamlessly integrate with SCADA
Many facilities already use supervisory control and data acquisition (SCADA) systems to monitor their daily operations. SCADA is a network of hardware and software, consisting of wireless sensors that gather data, software that analyzes that data and interfaces that allow managers to monitor the status of key assets. SCADA is usually associated with overseeing production; however, the system can also be harnessed for condition monitoring and predictive maintenance purposes. In fact, SCADA can be connected directly to a computerized maintenance management system (CMMS) so the SCADA data is immediately available for scheduling, issuing work orders and tracking asset health.
With an integration tool, the motor can be linked to directly in SCADA, thereby integrating the data into the maintenance management platform. From there, maintenance teams can use the data as part of a proactive, condition-based maintenance strategy.
With SCADA and CMMS integrated, teams will be able to:
- Choose which data to collect
- Decide how often to check machine health
- Set parameters to define asset health
- Issue work orders when vibration or temperature exceeds normal levels
2. Make smart decisions from anywhere
In today’s labor landscape, many key workers are operating remotely. Using industrial Internet of Things (IIoT) sensors and CMMS allows decision-makers to schedule maintenance, even when they are not on location. CMMS can automatically issue work orders when assets show signs of developing faults. Managers can also use the data to make smart decisions, even from a distance.
Managers can log in to their CMMS to check key indicators of asset health as well as existing maintenance schedules, cleanings and planned shutdowns. This makes it easy to make informed decisions about when to send in technicians.
3. Comply with regulations & prepare effectively for audits
A CMMS can include easy audit dashboards that demonstrate preventive maintenance compliance for all of the relevant national and international food safety regulations, including Safe Quality Food, British Retail Consortium, U.S. Food and Drug Administration and International Organization for Standardization 22000 food safety certifications.
A CMMS stores work orders, time-stamped records of all maintenance activities and historical sensor data. Some CMMS software offers preset audit dashboards or allows teams to customize reporting based on their requirements.