A major pipeline transmission company found itself reconsidering the effectiveness of its maintenance strategy. The company faced a challenge: optimizing asset visibility and implementing remote condition monitoring of equipment health while avoiding a high-cost investment and installation disruptions. This particular pipeline transfers a variety of products, ranging from gasoline to jet fuel, serving customers via pump stations and storage tanks across the United States. For this customer, it is imperative to ensure that pumping assets are efficient, reliable and safely maintained consistently. The pipeline supports the needs of more than 50 cities, thus making the pumping assets critical to the availability and overall operation. Technology plays a vital role in day-to-day operations in supporting end user activities, ensuring strict safety regulations, optimizing maintenance and providing data on equipment health. In this case, the pipeline company wanted to significantly improve and innovate upon its current maintenance approach in two ways: by monitoring asset visibility in real-time and trending data for their critical pumping equipment.
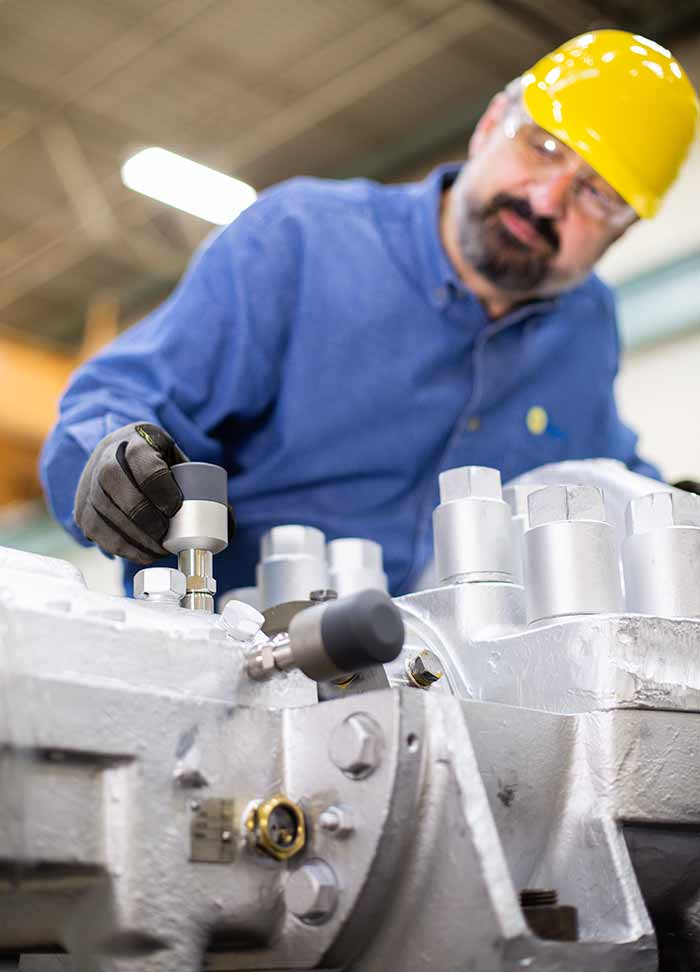
From Route-Based to Remote Monitoring
To transition from route-based, condition-based maintenance to remote-based, the company focused on machine vibration and temperature as primary early condition indicators. The cost to procure sensors, perform the installation (including power, conduit and data acquisition (DAQ) system) and implement a data analysis platform for those sensors proved to be exorbitant in the past, as compared to a state-of-the-art wireless system. In partnering with an aftermarket pump service provider with domain expertise in pumps, the pipeline company can extract maximum value from the collected data with confidence in support for their pumping assets. An IIoT-based solution gave the company a real-time measurement of machine vibration and temperature, as well as increased sampling or trending of machine health. The real-time data allows for users to make educated decisions regarding asset maintenance and associated schedules. It also allows decision-makers to identify issues before escalating and leading to unplanned equipment shutdowns.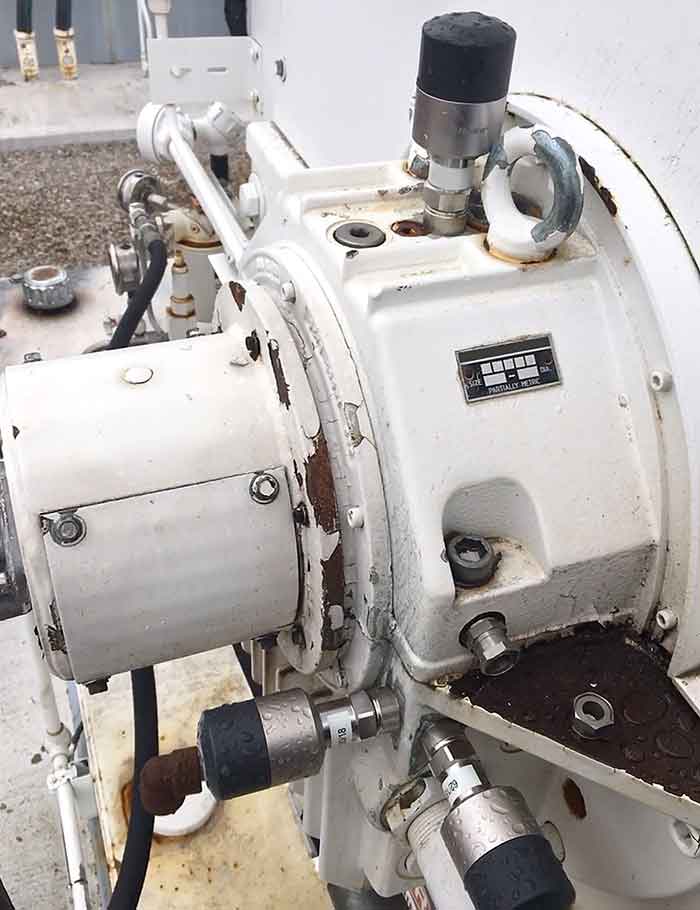
Real-Time Vibration & Temperature Data
In this case, the aftermarket pump service provider supplied a total solution by using wireless condition monitoring for the pumping assets while also offering pump repair, engineering and upgrades as opportunities for improvement. This newly executed system included wireless sensors mounted on pumps, motors and other critical machinery. Collection gateways were then provided to communicate with the sensors, collect data and transmit data to a cloud-based server. Once data is transmitted to a cloud platform, reliability engineers can access it from web-based software, regardless of their device or operating system. Access to the web-based predictive maintenance (PdM) platform allowed engineers to view data from anywhere, anytime—creating the flexibility required for their day-to-day operations. The specialized software allows users to monitor and trend condition indicators that are customizable for each sensor and machine. The main features include overall vibration amplitude and temperature trend data. The software also offers tools to perform time waveform analysis, FFT spectrum analysis and cross-phase analysis as part of a full suite of vibration analysis tools (Image 3). As machine data is collected, algorithms develop baseline levels of vibration and determine alarm threshold levels for each asset. Alternatively, user-determined alarm thresholds may be used based on historical data. If a sensor collects data that crosses a specified alarm threshold, an automatic notification is triggered by the software via email or text message.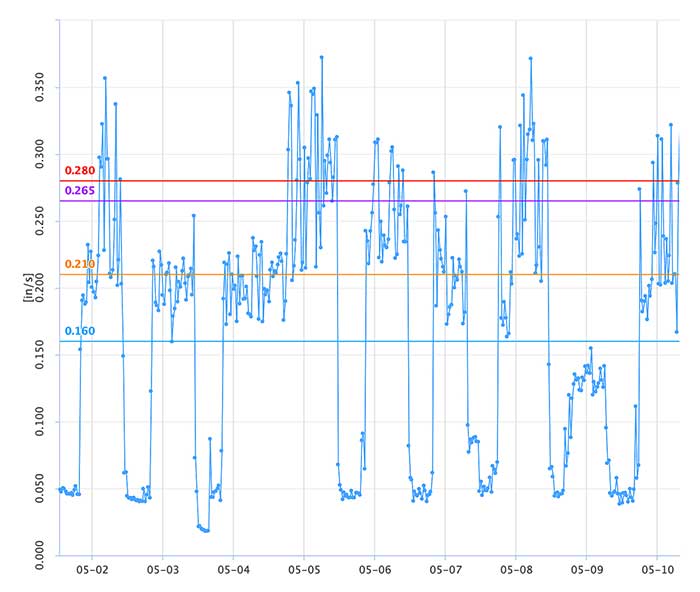
Benefits of Wireless Condition Monitoring:
- real-time data—not dependent on next route cycle
- high-frequency data collection (no missed events or issues)
- increased resources for data analysis and reduced data collection time
- customized alerts and alarms
- optimized maintenance schedules based on machine condition