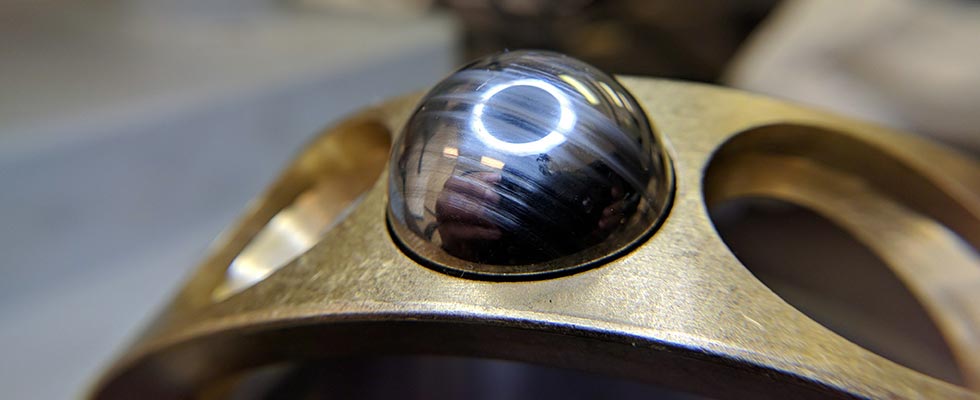
Did you know that 90 percent of pump failures can be attributed to a seal or bearing failure? Improving the life of machines starts with making sure these crucial components can do their jobs properly. Here are four factors that can help users increase the life of bearings and prevent pump failure from bringing the operation to a standstill.
1. Oil Contamination
Wind-blown sand, dust, steam and rain as well as condensation from thermal cycling—contamination can come from anywhere in an industrial environment. And it does not take much to do a lot of damage. Less than 1 percent water by weight is enough to emulsify the bearing oil and degrade its lubricity by a significant amount. What’s worse, all issues compound when it comes to bearings. So, even small difficulties can lead to big problems over time. For these reasons, the top concern should always be to remove contamination from the bearing oil—and remove it quickly.
Luckily, leading pump manufacturers are supportive. They have developed new bearing housings with cartridge filter assemblies built right in. These assemblies work in concert with the pump’s normal lubrication function to remove contaminants before they can damage the bearings. When the pump’s oil ring distributes oil within the housing to lubricate the bearings, some of it is caught by a collection mechanism within the housing. Gravity then draws the oil through the filter, which removes particles down to 10 microns in size and scrubs out dissolved water using specifically engineered moisture-absorbing material built into its fibers. If the filter becomes clogged, oiling of the bearings will continue before and during filter change.
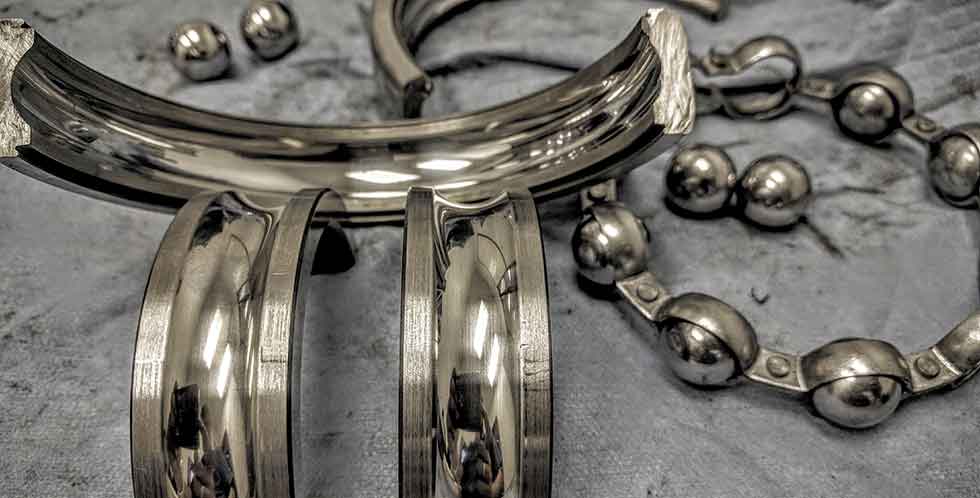
It is nearly impossible to address every potential source of contamination in an industrial setting, but with the added protection of a filter, risks are minimized.
2. Oil Viscosity
One of the biggest misconceptions about pumps in the industrial market is that as operating temperature goes up, the viscosity of the oil should go up with it.
The reasoning is that high temperatures decrease viscosity, so users need to increase the starting viscosity to compensate.
This belief is so persistent because, to a certain extent, it is true. But only to a point. After that point —which varies from pump to pump and across applications—higher viscosity is like honey in the bearing housing. The bearings cut right through the oil, displacing the essential fluid film between the balls and race. As a result of increased metal-on-metal contact, the localized heat will increase, decreasing the viscosity of the oil where it is needed most—at the contact patch. This leads to contact, skidding, and steel contamination of the oil, which increases overall oil temperature and decreases lubricity and viscosity over time.
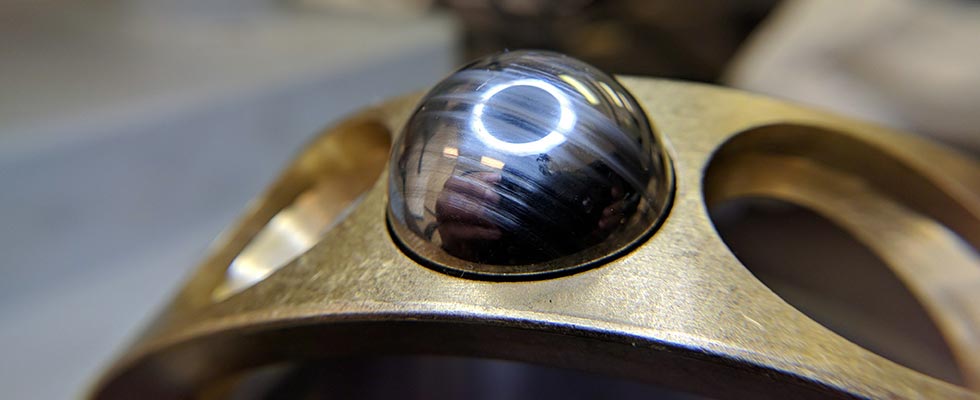
The oil used to lubricate bearings always needs to have a viscosity that makes sense for the load and environment. There is no better viscosity choice than the right one. Correct oil viscosity is best worked out in coordination with the machine manufacturer with all variables known, which is not often possible. But taking samples of the oil at regular intervals can be a useful way to check oil performance.
The point is to diagnose and correct problems early. Too many people wait until a bearing fails completely before they try to fix problems and are unable to determine if a lack of lubrication or a momentary event caused the failure.
3. Air Cooling
Modern industry demands modern methods of cooling. Without them, bearing temperature can fluctuate widely, increasing chances of oil contamination and promoting the onset of spalling.
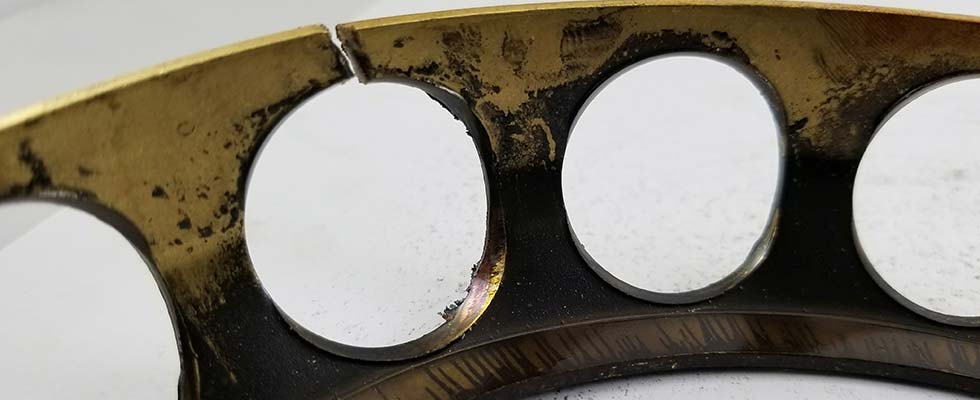
In the 1980s and 1990s, water cooling was the most common method of regulating pump temperature. This predictably led to problems with humidity and water in the bearing housing, oil emulsification and corrosion contamination. Since then, the industry has moved on from water cooling. But many organizations with legacy pumps have not.
If the organization still relies on water cooling—or even early forced-convection cooling systems—it is time for an upgrade.
The latest bearing housings have enhanced air cooling with axial fans and an effective cooling fin design. Updated air cooling can achieve oil and metal temperature reductions of up to 30 F over previous designs. Even better, these fans come standard with a guarded extension for easy retrofitting. So, if the process needs change, a new fan can be fitted without the need for expensive pump disassembly.
4. Monitoring Bearing Failure
It is important to keep the big picture in mind when it comes to bearing failure. Users need to look at the entire system—the oil, installation, process, load and environment.
The good news is users do not have to do it alone. Leading pump manufacturers can provide analysis and recommendations, modify solutions to meet specific requirements, or develop custom high-performance designs that fit within a desired budget.
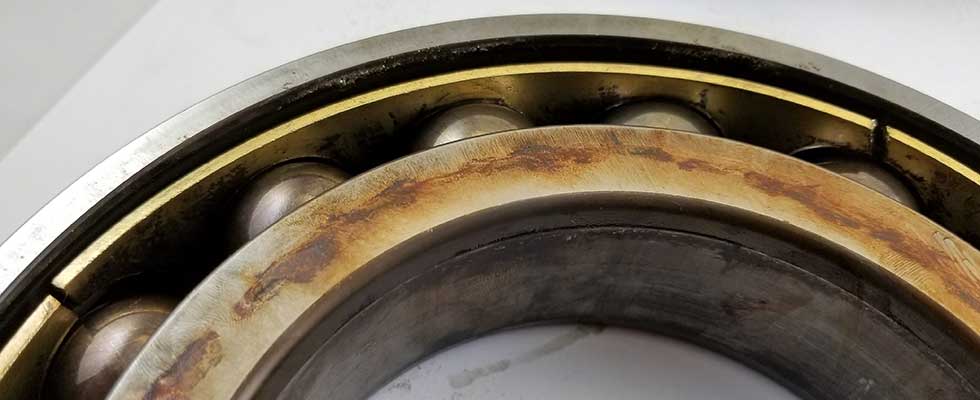
By partnering and working side by side with these experienced companies, users may be surprised to see how they can anticipate needs and provide proactive solutions to challenges.
It is this type of collaboration that achieves the best possible results in the industry, increasing the life of bearings and pumps and preventing expensive machine failures down the line.