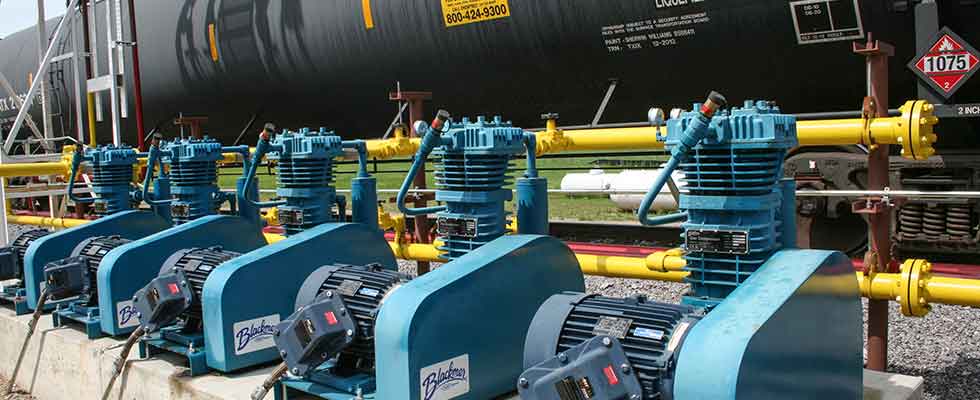
No self-respecting chef would attempt to make a new recipe without first having a list of ingredients. Anyone who is trying to piece together a jigsaw puzzle would like to know what the finished product is supposed to look like.
The same logic can be applied to industrial manufacturers: No one should acquire a compressor (or any piece of equipment) without first knowing all of the operational parameters of the application.
This article will discuss in general terms the transfer of all types of commodities in industrial applications via a reciprocating piston compressor.
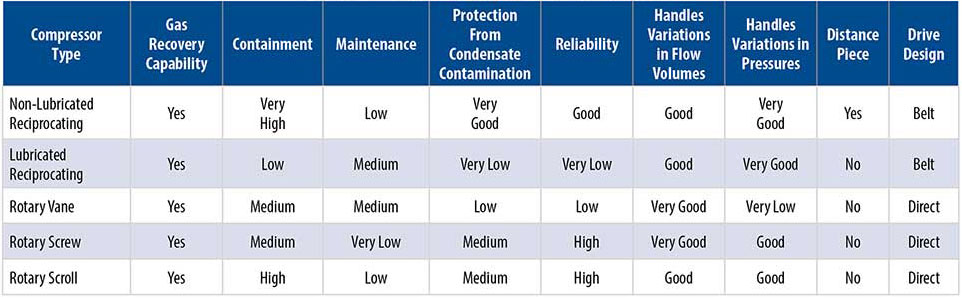
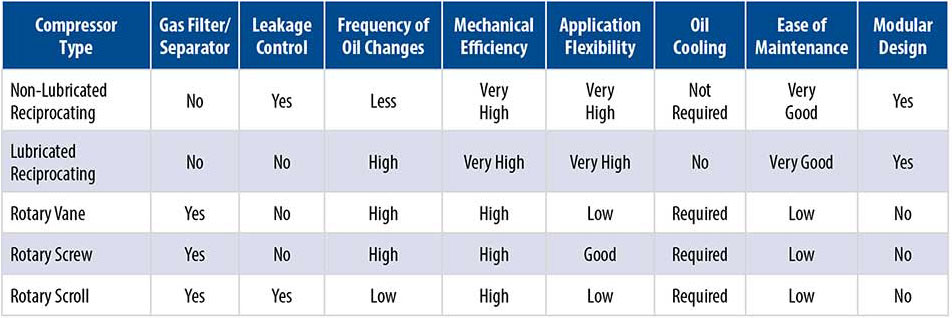
Know the Landscape
Commodities as wide-ranging as industrial gases, whether petrochemical, liquefied gas, inert or others, are commonly transferred for process boosting, loading, unloading, and/or vapor recovery. Because all of these substances have specific handling characteristics, the operator must perform due diligence to ensure that the proper style of compressor is selected for the proper operation.
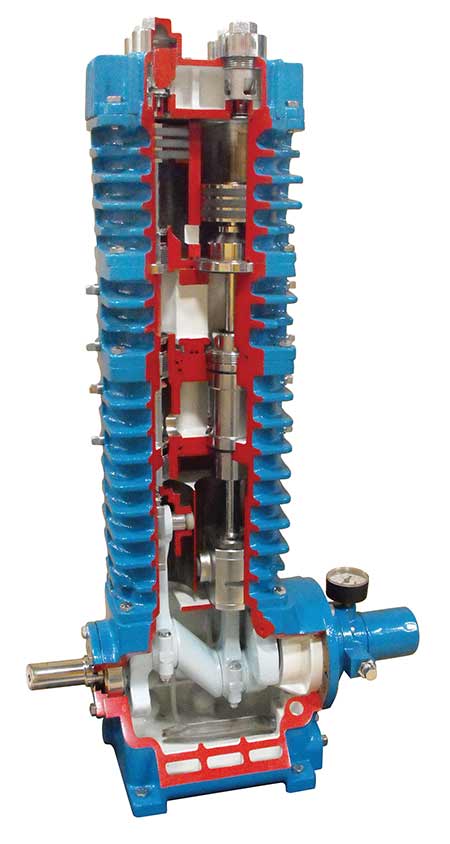
Some operational parameters to consider include:
1. Compression Ratio
This is a measurement that determines the amount of work a compressor must do in order to transfer a certain amount of product and is defined as absolute discharge pressure divided by absolute suction pressure. It is represented as a ratio of X:X. In general, a higher compression ratio means more work for the compressor, so decisions have to be made on the number of stages required and whether air-cooled or liquid-cooled equipment is a better choice. There is no one-size-fits-all rule when selecting a compressor. So, if the compression ratio is between 1:1 and 5:1, a single-stage compressor is likely the best choice. At 5:1 to 8:1, a single-stage machine may still work, but a two-stage compressor may need to be considered. A two-stage unit is the best choice from 8:1 to 12:1, and anything higher than 12:1 usually requires a three-stage or higher compressor.
2. Heat of Compression
The specific heat ratio of the product being compressed plays a factor in compressor selection. This ratio dictates how a gas behaves with respect to the heat of compression, and ultimately determines the number of stages required and whether air- or water-cooled equipment should be used.
3. Duty Cycle
This illustrates how often the compressor will be required to operate. For instance, will it be running 24/7 in continuous-duty operation, or just intermittently throughout a period of time?
4. Packaging
Determining what is needed, required or desired besides the actual compressor itself is a big decision to consider in all applications. What type of base/skid is needed? What about drivers and controls to meet the needs and safe operation of the equipment? If the unit is lubricated, what type of lubrication system is required and what are any associated filtration needs?
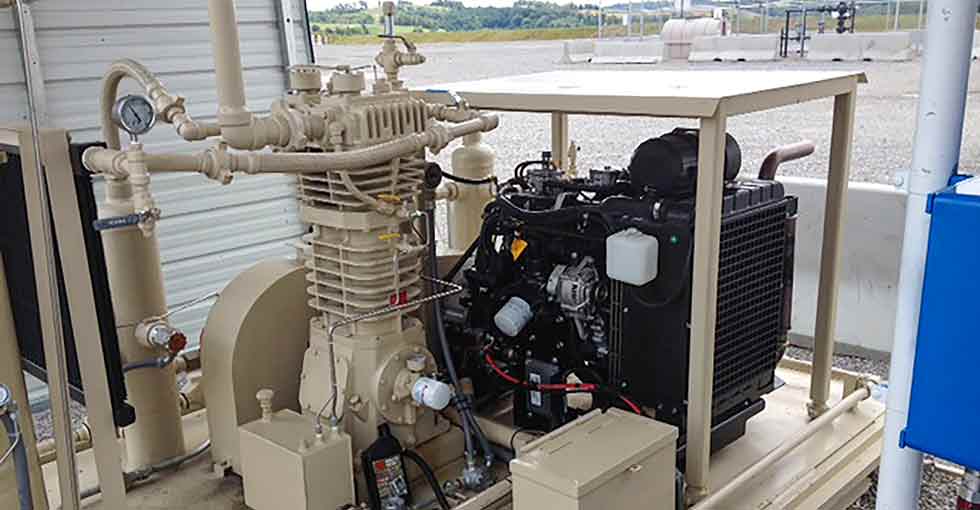
These are some of the considerations to take into account before a final selection can be confidently made. Since each specific application has different needs and requirements, work with the supplier or the compressor manufacturer itself to determine what package components are available and which ones will work best with the application.
5. Location
In other words, where will the compressor be installed? Ambient temperatures and elevation can also affect the compressor’s operation, so a model that is just right for colder climates like those in northern Russia or Canada, may not be the best choice in the hotter operating conditions found in desert countries or those situated along the equator.
6. Lubrication System
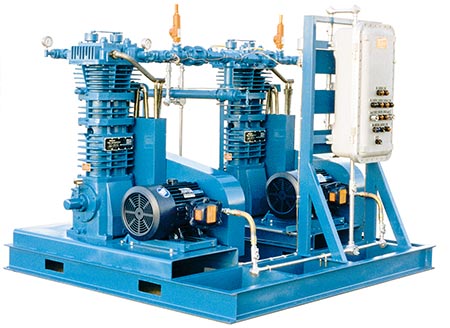
There are two primary types of reciprocating piston compressors: lubricated and nonlubricated (also known as oil-free). If the product-handling system can handle small traces of oil, a fully lubricated unit should be considered. If the system is incapable of handling small traces of oil, then an oil-free unit is the best choice. Note that “oil-free” means that no oil is present in the area of the machine where the product flows, though oil may be used to lubricate other parts in the machine that do not come in contact with the transferred commodity.
Also, another lubrication-related item to consider is the compressor’s leakage-control capability. In an age where the reduction or elimination of fugitive emissions to the atmosphere is becoming increasingly important, some compressor designs that require lubrication in the upper cylinder and valve area do not have a gas-sealing section, known as a “distance piece.” This method of design might produce a compressor with higher leakage rates, which can be viewed as an environmental hazard.
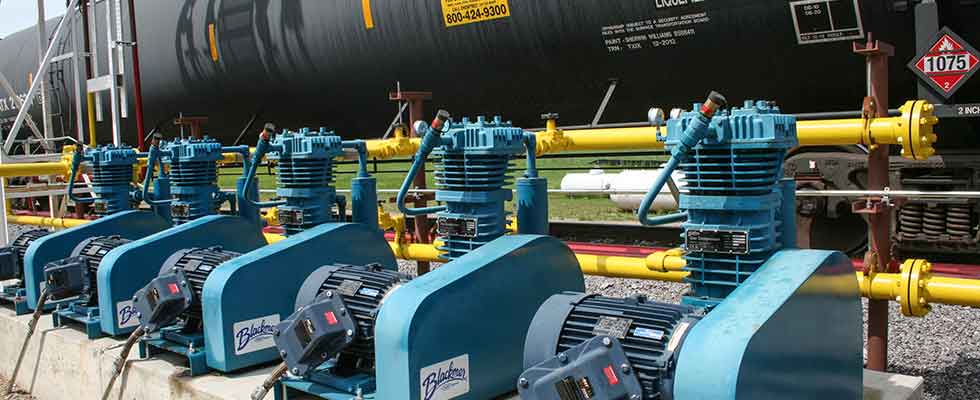
Knowing the needs, parameters and peculiarities of any type of product-transfer application is a must for anyone who wants to optimize overall operation. Information is key in making the right compressor choice.