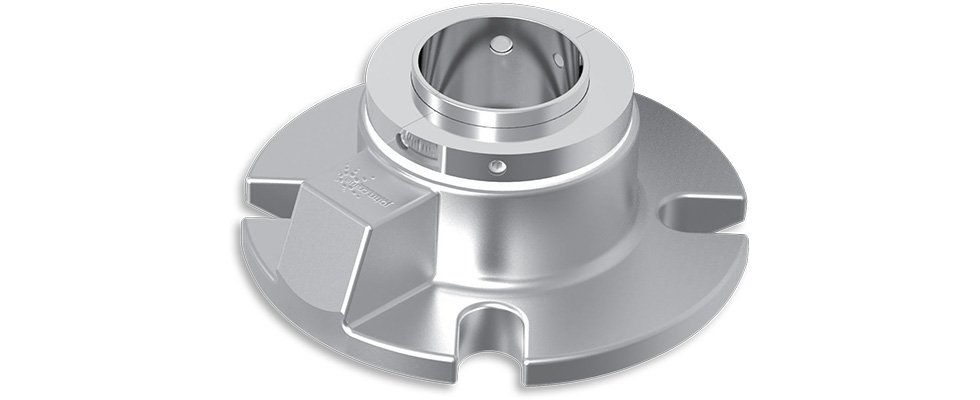
A United States oil pipeline operator placed a new 24-inch, 400-mile-long crude oil pipeline into service. Pipeline construction was completed in 2018 and included 36 mainline BB1-type centrifugal pumps operating at 10 pumping stations and two terminals. Each pump was fitted with traditional crude oil pusher seals.
However, startup inspections identified reoccurring failures caused by contaminates, pump performance issues and improper installation procedures. Gross shaft movement was also identified as a main contributor to premature wear of the main dynamic sealing component.
The combined effects of contaminates, shaft movement and the high-pressure environment caused seals to leak and fail within three to six months. Generally, meantime between failure (MTBF) for these types of pusher seals is three years or more in North American crude oil pipeline applications.
Originating in Midland, Texas, the pipeline would feed the company’s Gulf Coast network with a potential capacity of 450,000 barrels per day (bpd). However, without a dependable seal solution, the operator faced production delays and other costs.
At the same time the seal issues were identified, the seal supplier was completing the design concept of a nonpusher, elastomer seal that could withstand exposure to contaminates, elevated operating pressures and high axial movement levels.
The new seal was developed for the difficult operating conditions of pipeline pumping stations, like those originating in Midland. As the original seals failed, the operator replaced the pusher seals with the new seal that incorporates a nonpusher secondary element.
Since March 2018, every assembly placed into service has performed well without a single seal-related failure and has saved the operator an estimated $500,000 in seal-related and pump repair costs in one year.
Will It Work on NGLs?
Pipeline engineers wondered if the new seal would also work on natural gas liquids (NGL) pipelines.
Following crude oil cleansing, NGL leftovers are captured for refining and processing into a basic raw feedstock. Where there are crude oil pipelines, it is not uncommon to have a parallel NGL flashing hydrocarbon pipeline operated by the same company.
Over the coming months, the seal supplier developed variations of the seal—a noncontacting, high-pressure containment seal for NGL pipelines and product pipelines.
The new seals handle the NGL issues associated with crude oil pipelines, including shaft movement and particulate buildup, but also unique contaminants that cause an O-ring to swell. The NGL versions incorporate the same basic dimensional design as the standard seal.
While there are some critical internal design differences in the variations, much of the hardware and internal core components are shared across the various seal platforms.
The same dimensional design also affords the operator flexibility and interchangeability to a certain degree with how spare parts are inventoried within the operator/vendor business units. This allows for quicker and more cost-effective retrofit opportunities as pipelines shift in moving one liquid to the next due to changes in market demand. This allows the operator to streamline maintenance while tackling the tough pipeline sealing challenges.
Both the crude oil and new NGL pipeline seals are available to the liquid hydrocarbon pipeline market, offering users improved asset usage, lower life cycle costs and decreased maintenance requirements. The reduced leakage can improve equipment integrity as well for the two-thirds of North American pipelines that transport noncrude hydrocarbon products.