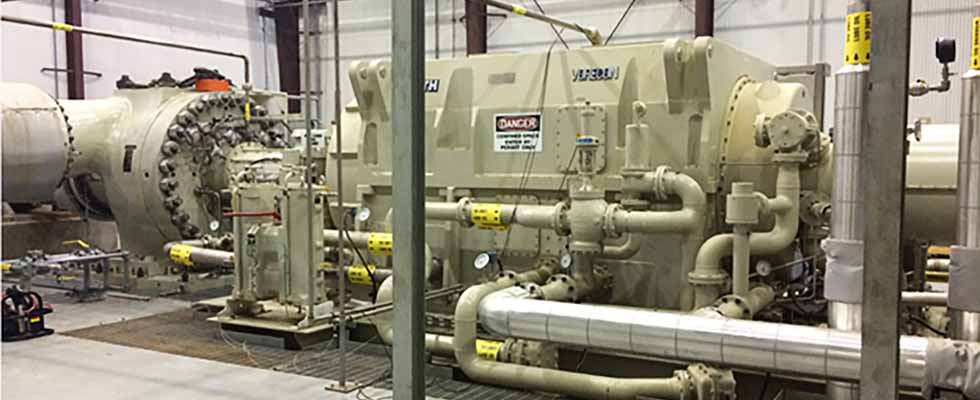
Uptime is everything.
That is why it pains most operators to pull down a system for any reason, even routine maintenance. As soon as a line goes down, money is lost, and routine maintenance is especially costly because many times that maintenance is not actually needed. It is performed to stay ahead of a real, unplanned outage, which, of course, is especially disastrous.
For many operators, vibration analysis is the answer to avoid unexpected downtime. It gives operators an opportunity to spot operational irregularities and points out necessary maintenance needs.
With the right placement of sensors and a well-documented baseline, vibration analysis can pinpoint mechanical faults early and extend the life of certain components while also providing insights on the status of the entire machine. As a result of these insights, operators can make informed decisions on the available options.
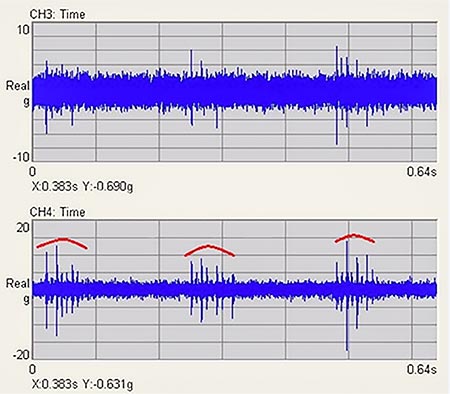
vertical measurements, the red arcs highlight the vertical measurements with impacting spaced at +/- 0.234 seconds. The output speed is 10,470 rpm.
Revelations Through Waveforms
At Florida Gas Transmission Co. (FGT), the benefits of vibration analysis became particularly evident during regular monitoring on one of their variable speed drives (VSDs).
The drive in question was in use by FGT to deliver gas from the Gulf of Mexico and into Florida. The 22,000-horsepower (hp) drive had planetary gear sets arranged for input at 1,800 revolutions per minute (rpm) and output at 11,000. The gear sets are arranged so that during operation the rotors function at eight different speeds.
As part of a regular check on the drive by the OEM, a vibration survey was performed on the unit and data was taken with permanently mounted proximity probes on the input and output shafts as well as magnetically mounted 100 millivolts per gravity (mv/g) accelerometers that are moved around the machine housing. Vibration was measured at two output speeds with the maximum test speed being 10,470 rpm due to pipeline conditions.
Time waveform and fast Fourier transform (FFT) data was taken at the outboard bearing housing. It showed a short duration impact that varied amplitude with the output speed—it revealed an 8 g swing at 10,000 output rpm and a 30 g swing at 10,470 output rpm. The time period of the impact also varied with speed.

The waveform data showed the impact occurred in bursts over a fairly long time period: Impacting within these bursts of energy was happening at approximately 0.008 seconds or 125 hertz (Hz), while the time period between the impacts was approximately 0.234 seconds or 4.27 Hz.
This helped determine the place to look for the cause of the impact; using spectral data, calculations of the fundamental bearing frequencies and other factors, the OEM was able to make the call.
Avoiding an Unplanned Outage
If the bearing had continued operating until it failed, FGT would have suffered disastrous consequences. At minimum, the unit would have needed a complete overhaul due to the debris created by a shattered bearing— a catastrophic failure that could mean downtime of approximately six to eight months.
Instead, the vibration analysis allowed FGT to purposely take the unit down for a much shorter term—just four days.
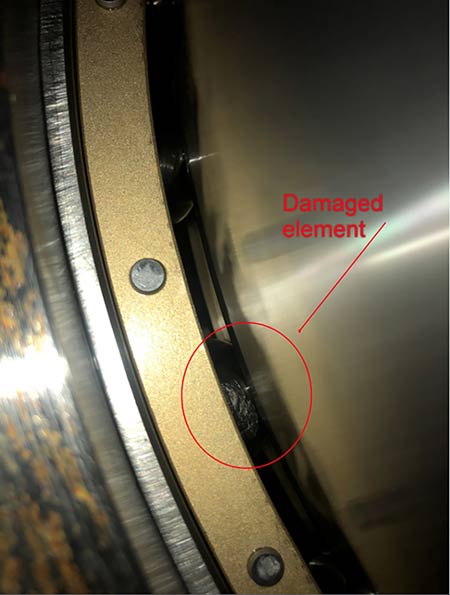
To achieve this turnaround, the OEM and a team from FGT performed a partial disassembly on the drive, where they removed the planetary gear set, inspected the unit and replaced the rolling element bearing supporting the outboard end of the gear set. With the bearing exposed, fatigue failure of two bearing rollers was discovered, which affirmed the recommendations based on the vibration analysis. It was requested that the bearing be sent back to the manufacturer for analysis.
FGT had a bearing available at a warehouse facility. It was an eight-hour drive to bring that to the site and two days to pull the VSD apart. The failing bearing was replaced and the machine was then put back together and running in the following two days.
In their review of the report from FGT and the OEM, the bearing’s manufacturer found wear of the rollers, scuffing and pitting of the bearing races in the load zone. There was also some wear at the bearing cage pockets and suspected axial movement of the cage.
Recommendations for Vibration Analysis
It is important to establish a baseline on the operational signature of key machines. However, this is not always the case.
While vibration analysis is helpful with critical components, it can also be a useful tool to curb the need for routine maintenance. Instead of performing this work at regular intervals, vibration analysis can dictate when such maintenance needs to be done.
For example, according to a routine maintenance plan, a component needs to be replaced every six months.
Through vibration analysis, that same part would only be replaced when its performance begins to decline, delivering helpful savings to the operation.
For FGT, the evidence is clear enough. A months-long emergency repair coupled with the logistical mess created by a drive outage versus a four-day part swap out? The best option is obvious.
When it comes to predictive maintenance, vibration analysis can be the difference between thousands of dollars and millions lost to downtime and repair.