Rotating liquid pump shafts that are originally sealed with soft packings mostly use contacting face seals, also known as mechanical seals. Typical rotational speeds are roughly between 1,000 and 3,600 revolutions per minute (rpm). In turbomachinery—such as compressors and expanders—the rotational speeds are higher and mechanical seals would not immediately appear to be an option, due to greater rubbing speeds along with a lack of liquid cooling and lubrication. Nevertheless, from the late 1970s when they were first marketed, noncontacting mechanical seals, known as dry gas seals in cartridge form, have been used in most gas turbomachinery. The first, and still the bulk, of these dry gas seal applications are through-shaft or beam machines where the shaft, carrying multiple closed impellers, is supported at each end, also known as “between-bearings” compressors. Shaft speeds range from near 20,000 rpm down to under 3,000 rpm for the biggest machines. The latter have shaft sizes up to 350 millimeters (mm), approximately 13 3/4 inches diameter.
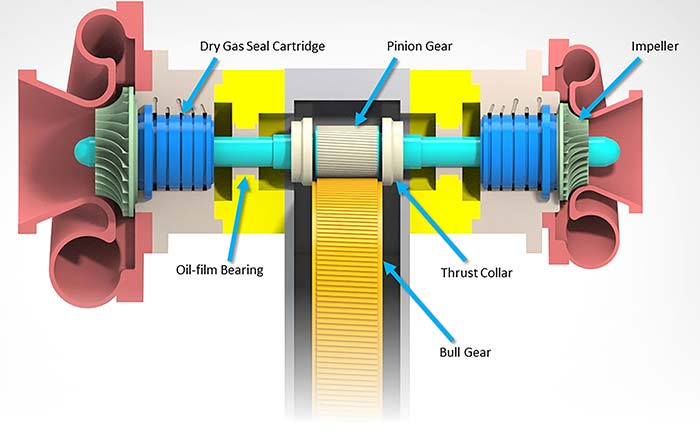
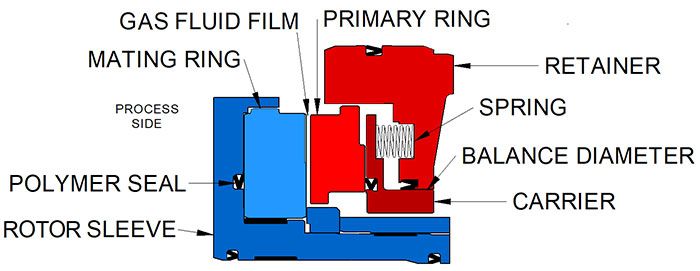
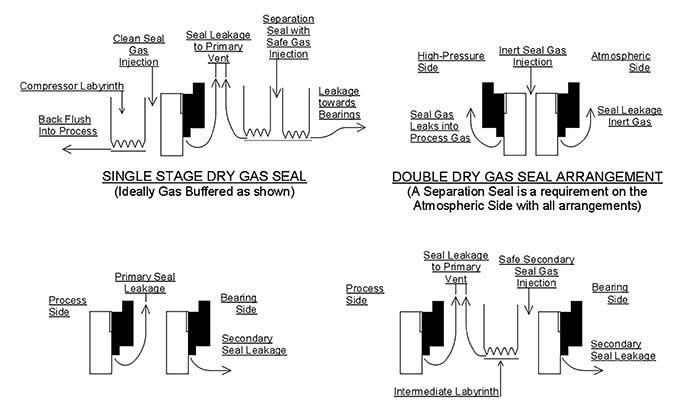